Parking Structures
Arcosa’s Lightweight Aggregate Elevates Costco Wholesale Headquarters Campus
- Teaser:When Costco decided to add an eighth level and 290 additional parking spaces to the original parking structure at their headquarters in Issaquah, WA—while the structure was already designed and under construction—Arcosa Lightweight provided the solution. The parking deck, which had been planned as a seven-level structure, was able to be modified mid-construction to accommodate the extra level thanks to Arcosa’s lightweight aggregate.
- Article Body Text:
At the time, Costco was struggling to fit within its limited campus footprint, forcing the company to maximize the use of space within its existing boundaries. The successful use of Arcosa’s lightweight aggregate allowed the additional parking level to be built without significant changes to the foundation, supporting the growing demands on parking infrastructure.
Paving the Way for Campus Expansion
Since then, Costco has received the necessary land use approval from the City of Issaquah to proceed with a long-awaited 1.2-million-square-foot expansion of the Costco Wholesale Headquarters Campus. This expansion includes a new 10-story parking structure and a nine-story office building, designed to consolidate thousands of employees from surrounding leased properties back onto the main campus.
The successful implementation of lightweight construction materials in the original parking structure laid the groundwork for this broader campus expansion, demonstrating the value of Arcosa’s lightweight aggregate in managing space and structural efficiency.
Lightweight Post-Tensioned Concrete Unique in the Northwest
“Using lightweight, post-tensioned concrete on the last three levels of the parking structure allowed us to go from seven to eight levels on the original foundation,” explains Tom Whiteman, Vice President of Sales and Marketing at Ferguson Construction Inc.. He adds that the use of lightweight concrete in a post-tensioning application is somewhat unique in the Northwest.
“This was the first job in this area that I know of that has used post-tensioned lightweight concrete in this way.”
Post-tensioning involves the placement of prestressing steel cables, or tendons, inside plastic ducts or sleeves in the forms before the concrete is placed. Once the concrete has gained strength, but before service loads are applied, the cables are pulled tight, or tensioned, and anchored against the outer edges, providing reinforcement.
Ready Mix producer Cadman Inc., a company that has been supplying concrete in the Puget Sound region for over 75 years, was supplier for this project. “Our slumps were dialed in from the start and we exceeded our strength requirement for 3-day stressing,” Whiteman says.
“In addition, the concrete pumped great, and the finish was even better. Cadman and Arcosa Lightweight provided a very consistent and high quality product throughout the job,” he adds.
This early use of innovative construction techniques at Costco’s campus helped address immediate parking needs while setting the stage for the broader expansion.
Future Outlook
The original parking structure project marked the beginning of Costco’s strategy to scale its headquarters infrastructure to accommodate long-term growth. Today, as the Costco Wholesale Headquarters Campus undergoes a transformative expansion, the innovative solutions provided by Arcosa Lightweight continue to play a pivotal role in ensuring that the company can meet its operational and workforce needs in a sustainable, efficient manner.
- The Issue: Expand an already under-construction parking structure from seven levels to eight, using post-tensioned concrete, without altering the original foundation.
- What Arcosa Did: Arcosa provided lightweight aggregate that allowed the parking deck to expand mid-construction by reducing the overall weight of the structure, enabling the addition of an eighth level without changing the foundation.
- Why Lightweight Works: Lightweight aggregate enabled the use of post-tensioned concrete on the top three levels, a unique approach in the Northwest, making the structure lighter without compromising strength.
- Result: The modified design resulted in a successful eight-level parking structure, with the use of lightweight post-tensioned concrete helping achieve early target strengths for the upper levels and reducing the weight on the foundation
- Key Quote: “Using lightweight, post-tensioned concrete on the last three levels of the parking structure allowed us to go from seven to eight levels on the original foundation.” – Tom Whiteman, Vice President of Sales and Marketing, Ferguson Construction Inc.
- Industry Context: The use of lightweight concrete in post-tensioning is rare in the Pacific Northwest, but it proved critical for expanding the parking structure at the Costco headquarters without significant alterations to the original design.
- Lessons Learned: Consistency in the mix, workability, and meeting early target strengths are key when using lightweight concrete in post-tensioning applications.
- Call to Action: Learn more about Arcosa Lightweight’s solutions for improving construction efficiency and enabling mid-project design modifications.
- Project: Costco Wholesale Headquarters
- Location: Issaquah, WA
- Customer: Ferguson Construction Inc.
- Client: Costco Wholesale
- Project Size: Eight-level parking structure with 290 additional spaces
Quick Facts:
•
•
•
Key Insights:
Quick Facts:
•
•
•
How Arcosa Helped:
•
•
Final Results
Key Quote
Context:
•
•
Explore Further
Additional Case Studies
Truist Park: Maximizing Parking Efficiency and Durability with Lightweight Precast Elements
- Teaser: Like many mixed-use developments, Truist Park thrives on its ability to accommodate the need to live, work, play—and park—all in one location, which is crucial to its success. Arcosa Lightweight provided the essential lightweight aggregate for the park’s parking structures, ensuring efficient use of space while meeting strict fire-rating and structural requirements.
- Article Body Text:
Metromont, a leading producer of precast concrete products, was responsible for supplying the precast panels, beams, and columns for both the stadium itself and its multiple parking garages. Angela San Martin, P.E., Sales & Business Development Manager at Metromont, shared the excitement of their contribution:
“We supplied all of the structural precast for the stadium as well as five parking garages. It was especially exciting for us since all of it was produced at our Hiram, Georgia plant.”
Double-Tee Beams and Lightweight Concrete
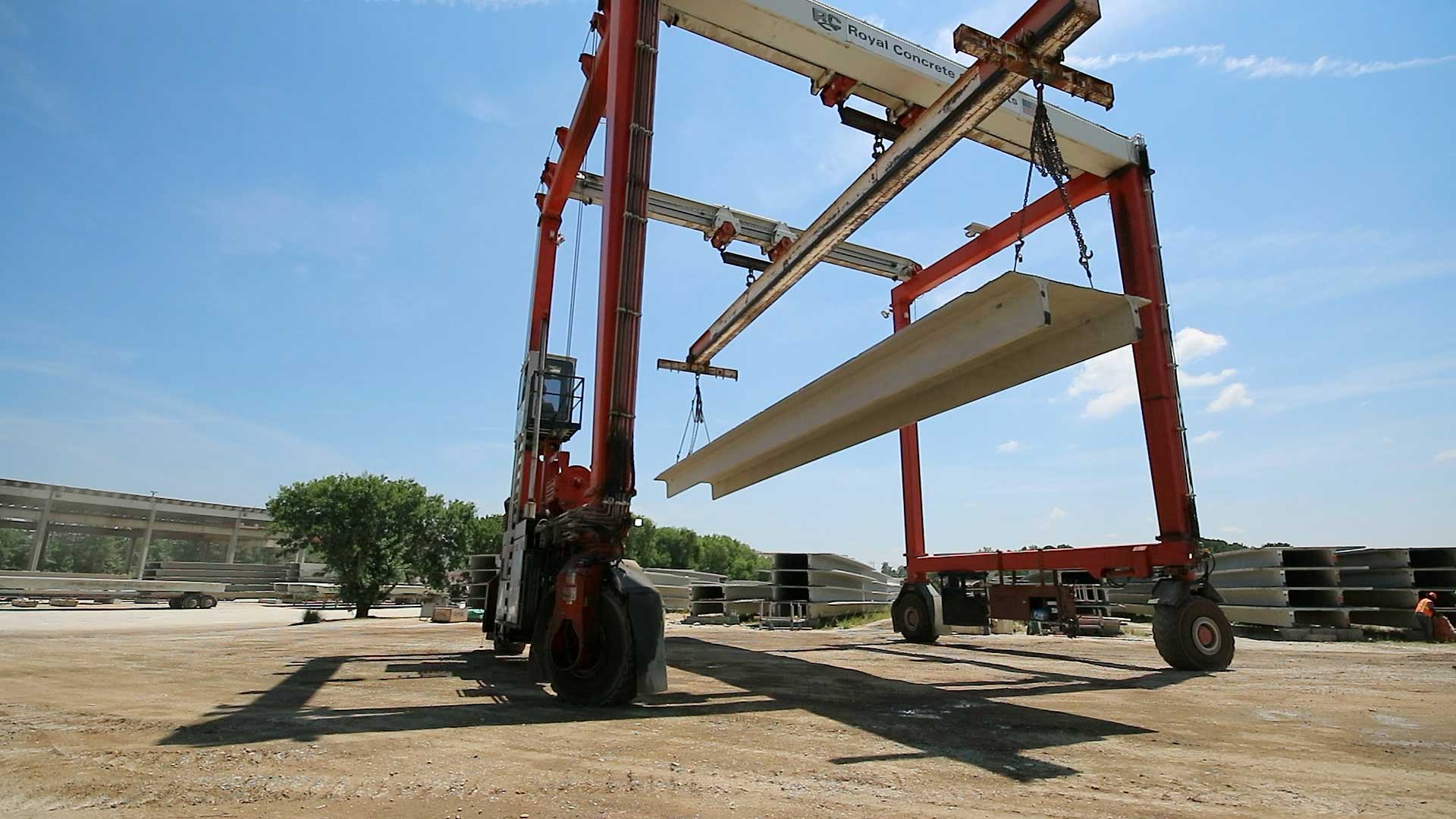
One of the most critical components in parking deck construction is the double-tee beams, which form both the floors and ceilings of parking garages. To meet fire-rating requirements and reduce the weight of these large pieces, Arcosa Lightweight provided lightweight aggregate for the concrete mix used in Metromont’s Hiram yard.
“On a few of the parking decks at Truist Park, the fire-rating requirements dictated our use of lightweight concrete,” said San Martin. “Lightweight concrete provides over two hours of fire protection based on the building type classification.”
Transporting these oversized double-tees safely across busy Atlanta required careful coordination. Lightweight concrete helped Metromont reduce the weight of each piece, allowing more efficient transportation and placement on-site. San Martin explained:
“We try to put more than one piece on a truck to reduce the number of shipments, which ultimately saves costs for the owner. Lightweight concrete allows us to do that.”
Lighter and Just as Strong
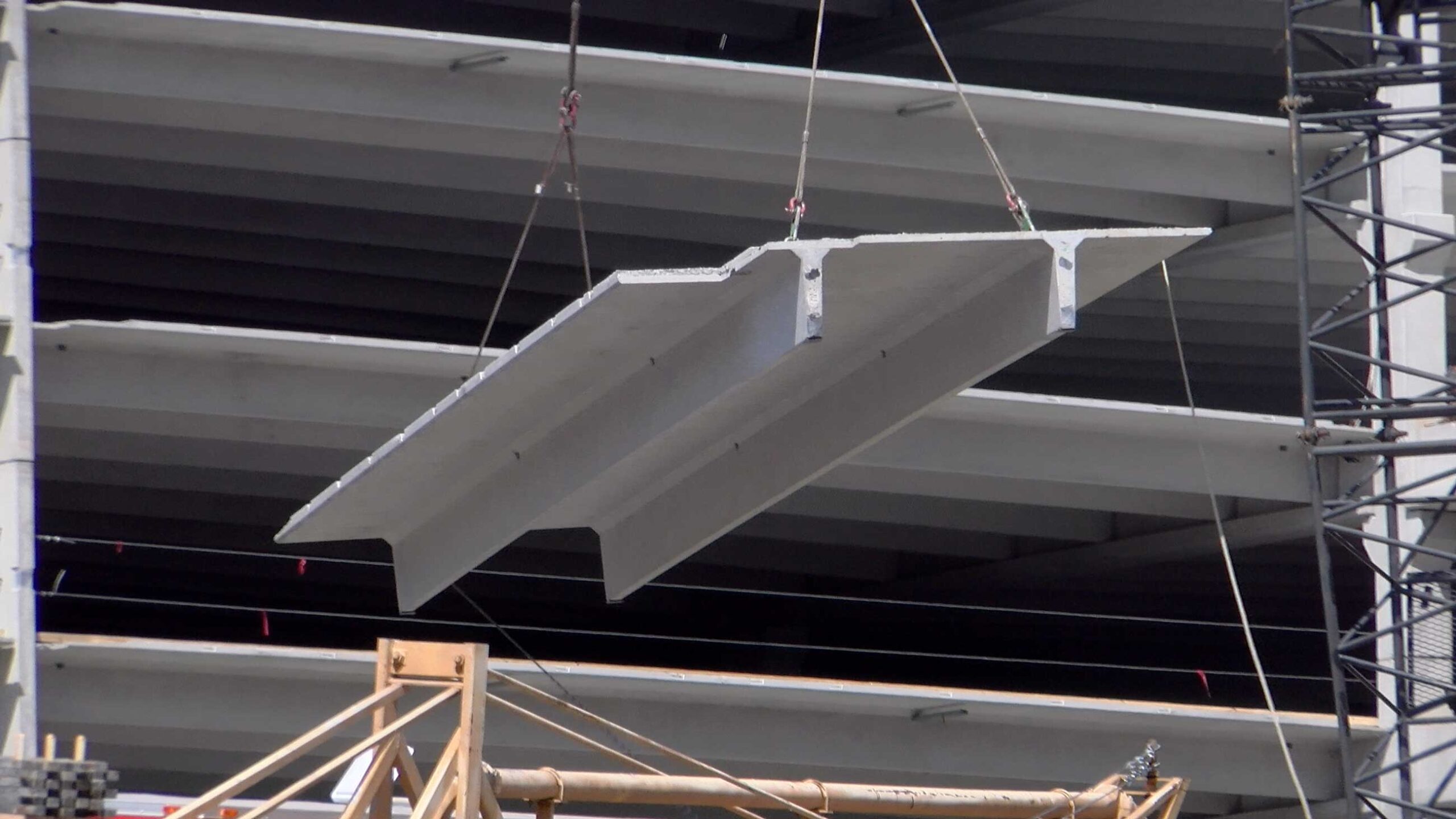
Lightweight concrete made a significant impact on Truist Park’s construction. San Martin noted: “The typical double-tee weighs about 35,000 pounds. Lightweight concrete keeps the structure’s overall weight down, which can be a significant cost savings when hauling and placing these oversized components.”
By using Arcosa Lightweight’s expanded shale aggregate, the overall weight of each precast piece was reduced by 25 to 35% compared to normal weight concrete, without sacrificing strength. The precast elements were easier to transport and install, and the lightweight concrete met fire-rating requirements, ensuring the safety and durability of the structure.
- The Issue: Build parking structures that accommodate thousands of fans at a busy sports and entertainment venue, while meeting fire-rating and structural requirements.
- What Arcosa Did: Arcosa provided lightweight aggregate for the precast concrete used in the parking structures, helping reduce the weight of the double-tee beams and ensuring efficient transportation and placement.
- Why Lightweight Works: The lightweight concrete provided over two hours of fire protection and reduced transportation costs by allowing more pieces to be hauled per truck.
- Result: The use of lightweight concrete reduced the weight of the precast components by 25 to 35%, enabling cost-effective transportation and efficient installation on-site.
- Key Quote: “Lightweight concrete keeps the structure’s overall weight down, which can be a significant cost savings when hauling and placing these oversized components.” – Angela San Martin, P.E., Sales & Business Development Manager, Metromont
- Industry Context: Lightweight concrete provided the necessary fire protection and structural performance while reducing costs related to transportation and installation.
- Lessons Learned: Using lightweight aggregate in precast elements can lower overall project costs, improve logistics, and meet stringent fire safety regulations.
- Call to Action: Discover more about how Arcosa Lightweight can optimize concrete solutions for large-scale projects and improve efficiency.
- Project: Truist Park
- Location: Smyrna, Georgia
- Customer: Metromont
- Client: Atlanta Braves
- Project Size: 60-acre site
Key Insights:
Quick Facts:
•
•
•
How Arcosa Helped:
•
•
Final Results
Key Quote
Context:
•
•