Internal Curing
A Look Back at the Union Pacific Dallas Intermodal Terminal (DIT)
- Teaser:The Union Pacific Dallas Intermodal Terminal (DIT) project stands as a testament to the transformative benefits of lightweight aggregate in improving the durability, strength, and overall performance of concrete paving. Notably, it remains one of the largest internal curing paving projects in the United States, with over 250,000 cubic yards of concrete used.
- Article Body Text:
Located south of Dallas, Texas, this expansive facility endures daily use by heavy trucks transporting millions of tons of cargo annually. The DIT supports numerous businesses that depend on intermodal rail freight to export Texas-made products and receive global imports.
Reflecting on the project’s success, Clint Chapman, Western Region Marketing & Technical Manager at Arcosa Lightweight, shared insights into the innovative approach taken during construction:
“What made the concrete paving mix unique was the incorporation of a medium gradation of lightweight aggregate, used in combination with limestone aggregate and concrete sand. The addition of lightweight aggregate facilitated internal curing for the low-slump, low water-cement ratio, high-strength concrete mix.”
Construction Highlights
The construction phase presented a range of challenges, spanning Texas’ seasonal extremes from cold, wet conditions to hot, dry climates. Despite these environmental variations, the 3-inch maximum slump concrete mix proved easy to place and finish, consistently exceeding expectations. The specified 28-day compressive strength surpassed its target by an average of 1000 PSI, and the 28-day flexural strength was achieved within just 3 days.
The UP DIT pavement was also among the first large-scale concrete paving projects to utilize internal curing techniques.
In a 2007 Concrete international article entitled Better Pavements Through Internal Hydration, Victor H. Villarreal, P.E., MBA, FACI (now with Master Builders Solutions) noted that the 2005 paving project used concrete from a double central-mix batch plant set up at the site.
Villarreal wrote that the Union Pacific project was, at the time, “the largest project in the world that took advantage of the internal hydration concept of prewetted lightweight aggregate in low-slump paving.” and that “in contrast to conventional paving mixtures, cracking has been extremely minimal.” He goes on to say:
“The slow release of moisture from the LWA to the concrete matrix resulted in the mitigation or elimination of plastic and drying shrinkage cracking, as well as limiting the effects of self-desiccation.”
How Internal Curing for Pavements Differ
Concrete mixtures typically utilized for rigid pavements typically have a lower cement content than bridge deck concrete mixtures.
In the report Evaluation of Internally Cured Concrete for Paving Applications, researchers Chetana Rao, Ph.D., and Michael I. Darter, Ph.D., P.E. concluded that:
“The two key benefits determined for ICC in concrete pavement is structural longevity and durability. Structural longevity is improved with ICC due to its small reduction in unit weight, elastic modulus and coefficient of expansion and a small increase in strength.”
These effects when combined lead to significant positive impact on slab fatigue damage and slab cracking in jointed concrete pavements.
Thanks to this method, and the superior performance of the concrete mix, the pavement remains virtually crack-free after years of continuous use.
- Project: Union Pacific Dallas Intermodal Terminal (DIT)
- Location: Hutchins, Texas
- Project Size: 250,000 cubic yards of concrete
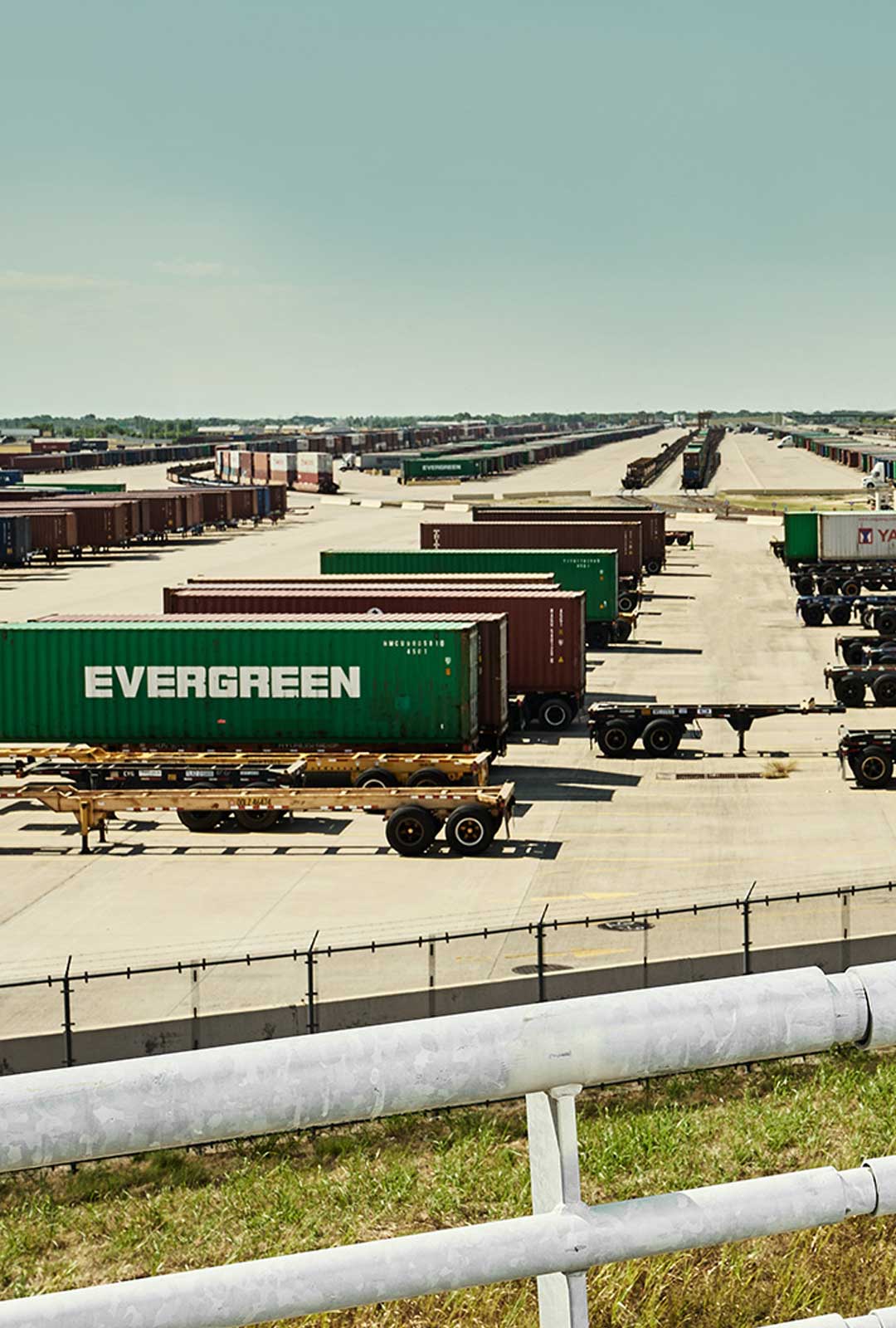
Quick Facts:
•
•
•
Learn More
Internal Curing Gains Ground in Highway Construction: A Durable Solution
- Teaser:
Internal curing is being recognized as a significant advancement in concrete technology. Today, the integration of lightweight aggregate (LWA) into concrete offers enhanced performance by reducing cracking, improving durability, and extending the service life of critical infrastructure. From bridge decks to highway pavements, this innovative technique is delivering longer-lasting solutions with lower maintenance costs. - Article Body Text:
Internal curing is accomplished by incorporating pre-wetted lightweight aggregates (LWA) into a concrete mixture. Pores in the LWA function as reservoirs that readily release water as needed for hydration or to replace moisture lost through evaporation or self-desiccation. By maximizing cement hydration throughout the interior of concrete, internal curing can contribute to increased strength while reducing autogenous stresses and strains.
Concrete pavements often face challenges such as shrinkage, cracking, and curling, which can severely affect their durability and service life. As moisture evaporates from the surface during the curing process, shrinkage stresses develop, leading to cracks that allow water and deicing salts to penetrate. This can cause corrosion of steel reinforcement and eventually shorten the pavement’s lifespan.
Pioneering research from experts like Dr. Jeffery R. Roesler and successful field applications by agencies such as the Illinois Tollway demonstrate the growing adoption of internal curing across the nation. As transportation authorities increasingly incorporate this method into their projects, internal curing is poised to become a standard practice in modern concrete construction.
Research Insights from Dr. Jeffery R. Roesler
Dr. Jeffery R. Roesler, a professor of Civil and Environmental Engineering at the University of Illinois Urbana-Champaign, has been at the forefront of internal curing research. He first became involved with internal curing technology during his studies of the challenges faced by concrete pavements in coastal and dry climates, where slab curling and cracking are prominent issues.
“We started with a belief that [internal curing] could have a significant impact on moisture curling in concrete pavements. As water is lost from the surface early on after construction, it causes the slab to curl up such that it loses support at the edges. That can lead to premature cracking and some long-term performance problems. We hypothesized that internal curing would reduce this phenomenon, because the moisture content would be more uniform through the slab thickness.”
“Our tests have shown that internal curing can reduce slab curling by as much as 50% in laboratory conditions,” says Dr. Roesler. “With more uniform moisture throughout the concrete, there is less cracking and less stress at the surface, resulting in a smoother, more durable pavement.”
Field Applications and Practical Benefits
Encouraged by these laboratory findings, the Illinois Tollway Authority conducted field tests to examine the benefits of internal curing on continuously reinforced concrete (CRC) pavements. These tests, overseen by Steve Gillen, then Deputy Program Manager for Materials, involved the use of a 10.5-inch CRC pavement incorporating internally cured concrete.
According to Gillen, the thinner slab depth, along with the use of a cement-treated base, led to cost savings in materials, particularly steel, without compromising pavement performance.
“With the continuously reinforced concrete (CRC) pavement subbase and internal curing, we’ve reduced the internally cured slab depth to 10.5 inches rather than the 12-inch slab depth used for the last major reconstruction project in 2008. That allowed for a reduction in the overall material costs, but the most significant cost impact is the reduction in steel costs,” he says.
Today, Steve Gillen serves as Engineering Manager, Transportation at Horner & Shifrin in St. Louis, Missouri, and brings his 27 years of experience at the Illinois Tollway to new projects.
Growing Adoption Across Transportation Authorities
Since the early adoption of internal curing, its application has expanded across various state departments of transportation (DOTs) and municipalities. Agencies such as New York, Indiana, Louisiana, North Carolina, Ohio, and Utah DOTs have successfully implemented internal curing in bridge decks, while Kansas and Texas DOTs, as well as the North Texas Tollway Authority, have used it in pavement projects. Additionally, cities like West Lafayette, Indiana, and municipalities in Michigan have embraced internal curing for pavement patches and repairs.
This growing list of applications highlights the versatility and effectiveness of internal curing for improving the performance of concrete infrastructure across a variety of climates and conditions.
A Look to the Future
Research into the long-term benefits of internal curing is ongoing, with agencies continuing to monitor field test sections for cracking, warping, and overall pavement durability. As more data becomes available, researchers and transportation authorities are refining their design methods to further optimize the use of internally cured concrete.
Jason Weiss, professor and head of the Civil and Structural Engineering School at Oregon State University, points out that internal curing is transitioning from research to mainstream use:
“Decision-makers should look at internal curing as another tool in the tool belt. It offers tangible benefits for reducing cracking, improving pavement durability, and minimizing long-term maintenance costs.”
Concrete producers and contractors are also finding that the adjustments required for internal curing—such as pre-wetting lightweight aggregate and modifying mix designs—are relatively straightforward. As internal curing specifications become more standardized, it is expected to become a common feature in large-scale infrastructure projects.
Conclusion: A Durable, Cost-Effective Solution
The adoption of internal curing marks a significant step forward in the quest for more durable and cost-effective concrete pavements. By reducing shrinkage and slab curling, internal curing extends the lifespan of pavements while also offering smoother, safer rides for motorists. As research continues and field data is collected, internal curing is poised to become a cornerstone technology in the design of modern concrete infrastructure.
As Dr. Weiss notes, “[Internal curing] means people can install infrastructure elements that should provide longer-lasting and improved service. You reduce maintenance costs, but you also reduce inconvenience for the traveling public so the social costs go down. In most instances, it’s a more sustainable option because you’re not replacing things so often and using as much repair material.”
- The Issue: Premature cracking, shrinkage, and slab curling are common issues that affect the durability and service life of concrete pavements, leading to higher maintenance costs and a reduced lifespan.
- What Arcosa Did: Incorporating pre-wetted lightweight aggregates (LWA) into concrete to provide internal curing, reducing shrinkage and cracking.
- Why Lightweight Works: LWA releases moisture as needed throughout the concrete, reducing moisture differentials, which mitigates cracking and curling while increasing durability.
- Result: Internal curing improved pavement performance, reducing slab curling by up to 50% in lab tests and leading to cost savings in field applications through thinner slab designs and reduced steel usage.
- Key Quote: “[Internal curing] offers tangible benefits for reducing cracking, improving pavement durability, and minimizing long-term maintenance costs.” – Dr. Jason Weiss
- Lessons Learned: Internal curing can offer cost-effective solutions for long-lasting concrete pavements, especially in areas prone to moisture-related cracking and warping.
- Call to Action: Internal curing is being adopted by state departments of transportation and contractors for highway, bridge, and pavement projects, positioning it as a standard tool for improving concrete infrastructure durability.
Key Insights:
Quick Facts:
•
•
•
How Arcosa Helped:
•
•
Final Results
Key Quote
Context:
•
•
Additional Case Studies
Internally Cured Concrete Enhances Water Tank Durability in Denver Water Projects
- Teaser:Denver Water is committed to ensuring safe and reliable water for its customers. To achieve this, the utility continually upgrades its system by replacing aging, large-capacity water storage tanks with more durable designs that are less susceptible to leaks. One way they have done that is through the use of Internally Cured Concrete (ICC).
- Article Body Text:
This material has been successfully employed in multiple major tank replacement projects, including the Lone Tree, Highlands, and Ashland facilities, where it has helped to significantly reduce cracking and improve long-term performance.
At Lone Tree, a new 10-million-gallon underground water tank was constructed, providing a reliable water supply for the Southgate Water District and meeting fire response needs. In Highlands, Denver Water built a 7-million-gallon circular post-tensioned concrete water storage tank. At Ashland, two 20-million-gallon tanks were replaced as part of a major upgrade.
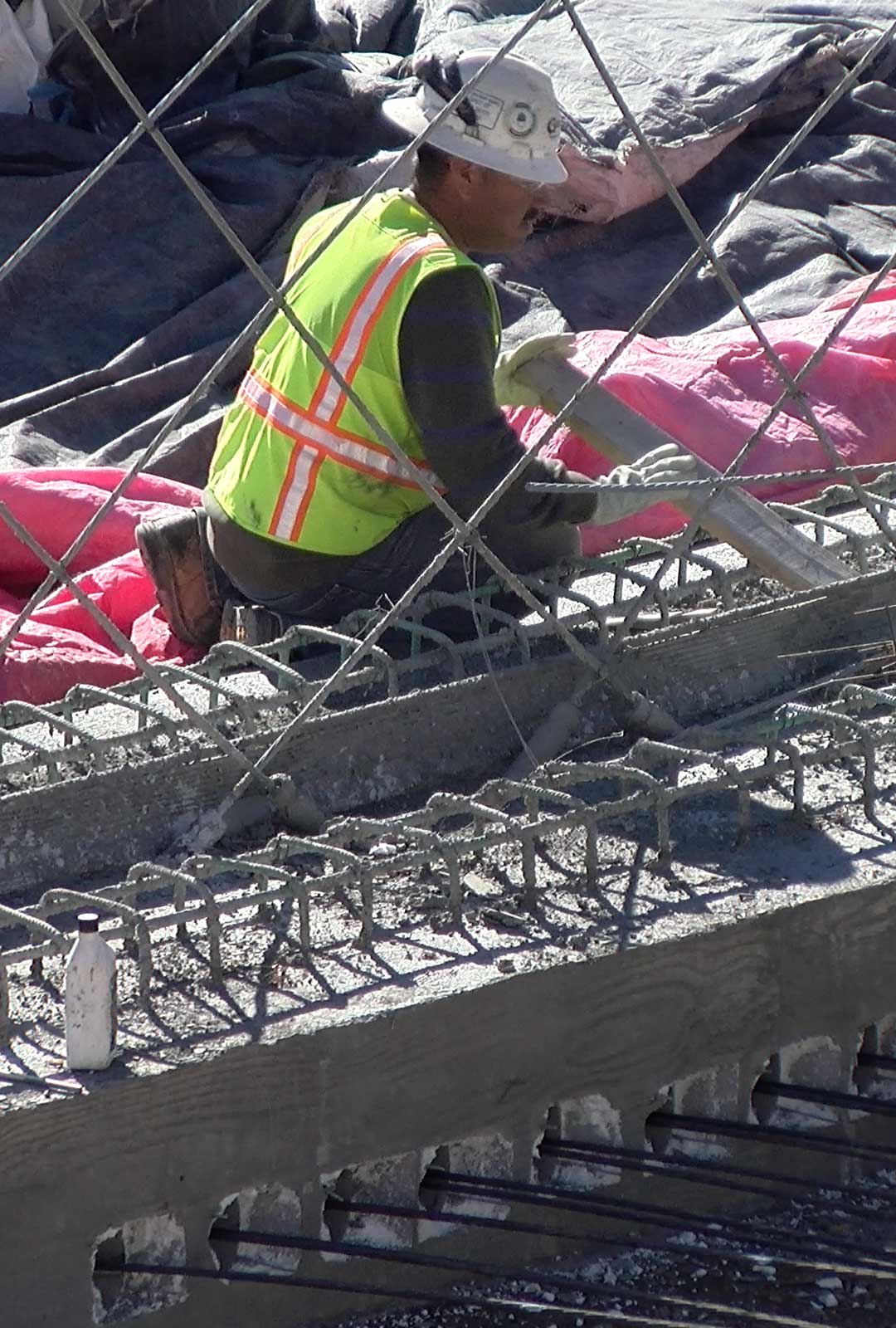
Why Internally Cured Concrete Works
Internally Cured Concrete has been crucial to the success of these projects by reducing shrinkage cracking and enhancing durability.
ICC uses expanded shale, clay, or slate (ESCS) lightweight aggregates, which absorb and gradually release water to sustain hydration throughout the concrete. This ensures a more uniform cure, preventing early-age shrinkage and cracking.
Bill Wolfe, Marketing & Technical Manager for Arcosa Lightweight, explains: “Internally cured concrete acts just like ordinary concrete, but with the additional benefit of reduced cracking and leakage. Once we demonstrated its effectiveness, Denver Water saw the results firsthand, and made it standard practice to use ICC in many of their tank replacement projects.”
Addressing Slab Placement Challenges
Placing large concrete slabs without joints is a challenge, especially in Colorado’s dry and windy climate. Erik Holck, P.E., Semi-Retired Civil Engineering Consultant, who spent 24 years at Denver Water, notes, “We constantly looked to improve the durability of our facilities, and Internally Cured Concrete was a great way to improve the quality, performance, and long-term durability of our large-scale treated water tanks.”
For the Lone Tree Tank No. 2 project, Holck and Robert Bates of Bates Engineering chose an ICC mixture to ensure both the base and roof slabs could withstand the harsh climate without succumbing to shrinkage cracking.
Lightweight Aggregate Utilized
To meet the specific project requirements, Aggregate Industries, now part of Holcim US, produced the high-performance ICC using prewetted expanded shale lightweight aggregates sourced from Arcosa’s Boulder, Colorado, operation. The aggregates helped achieve the desired strength, placing, and finishing characteristics for the slabs, walls, and columns.
According to Wolfe,
“By using ICC, we were able to speed up construction while ensuring long-term durability. The ICC mixture allowed the contractor to strip and set forms faster, which helped keep the project on schedule.”
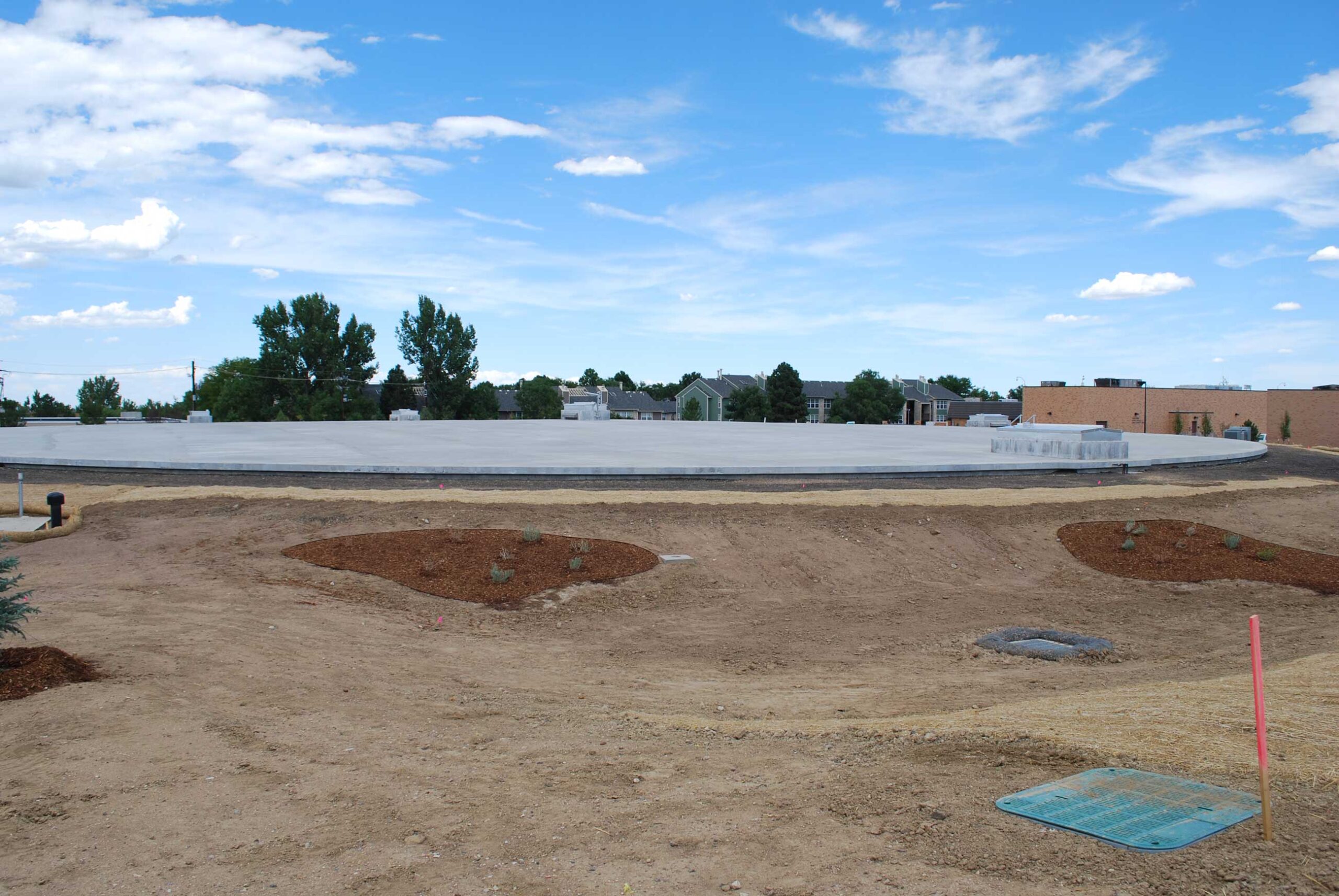
Broader Infrastructure Upgrades
Denver Water manages 31 treated water storage tanks across its service area. Since adopting ICC, eight of these tanks have undergone major upgrades, significantly reducing shrinkage cracking and enhancing durability. These upgrades are part of Denver Water’s broader initiative to improve infrastructure and deliver safe, reliable water to over 1.5 million people in the Denver metro area.
Internally Cured Concrete has proven to be a highly effective solution for reducing shrinkage cracking, improving durability, and streamlining construction schedules. As Holck explains,
“The qualities of ICC that make it so effective are its ability to reduce shrinkage cracking, enhance hydration, and decrease permeability.”
With successes in projects like Lone Tree, Highlands, and Ashland, Denver Water plans to continue utilizing ICC across future tank projects to ensure long-term performance and reliability for its critical water infrastructure.
- The Issue: Placing large concrete slabs for water storage tanks without construction joints in a low-humidity and windy climate presented challenges related to shrinkage cracking and durability.
- What Arcosa Did: Arcosa provided prewetted expanded shale lightweight aggregates in collaboration with Aggregate Industries (Holcim US) to create an Internally Cured Concrete (ICC) mixture that reduced shrinkage cracking and improved durability.
- Why Lightweight Works: The prewetted lightweight aggregates helped achieve the desired strength, placing, and finishing properties for the slabs, walls, and columns, ensuring long-term durability and reducing shrinkage cracking.
- Result: ICC was successfully used in the renovation of the Lone Tree Tank No. 2, reducing shrinkage cracking and accelerating the construction timeline.
- Key Quote: “Internally Cured Concrete is a great way to improve the quality, performance, and long-term durability of large-scale treated water tanks.” – Erik Holck, P.E., Former Denver Water Engineer
- Industry Context: Low-shrinkage concrete and ICC proved to be the best methods for combating the challenges of Colorado’s climate, ensuring better curing and enhanced structural durability.
- Lessons Learned: Using ICC and prewetted lightweight aggregates significantly enhances durability and helps reduce shrinkage cracking, especially in challenging environments like Colorado.
- Call to Action: Learn more about how Arcosa Lightweight aggregates can help address complex construction challenges in large infrastructure projects.
- Project: Water Tank Replacements
- Location: Lone Tree, Colorado
- Customer: Holcim US
- Client: Denver Water
- Project Size: 1,300 CY of ICC used for floor slabs, 1,800 CY for roof slabs
Key Insights:
Quick Facts:
•
•
•
How Arcosa Helped:
•
•
Final Results
Key Quote
Context:
•
•
Explore Further
Additional Case Studies
TVA Utilizes Internal Curing for Historic Hydroelectric Dam’s Bridge Deck
- Teaser: The Wilson Dam bridge deck, part of the iconic 100-year-old hydroelectric dam on the Tennessee River in Muscle Shoals, Alabama, is ready handle another century of traffic. Arcosa Lightweight’s material played a pivotal role in these extensive repairs, ensuring the bridge’s longevity by supporting the Tennessee Valley Authority’s (TVA) first-ever use of internally cured concrete.
- Article Body Text:
This innovative solution will help the historic structure stand the test of time, offering enhanced durability and resilience.
“Our goal was to provide a 100-year bridge deck, and internal curing is a great way to achieve that,” explains Benjamin Byard, Bridge Program Manager at TVA. “Because you keep the internal relative humidity high much longer, you get increased strength before the concrete starts to desiccate. The combination of better strength and delayed drying shrinkage gives you a denser, better concrete. The decrease in cracking and increase in mechanical performance are the values of internal curing.”
Byard also highlighted the new surface, saying,
“The new surface is composed of reinforced ‘internally cured’ concrete, which should stand the test of time.”
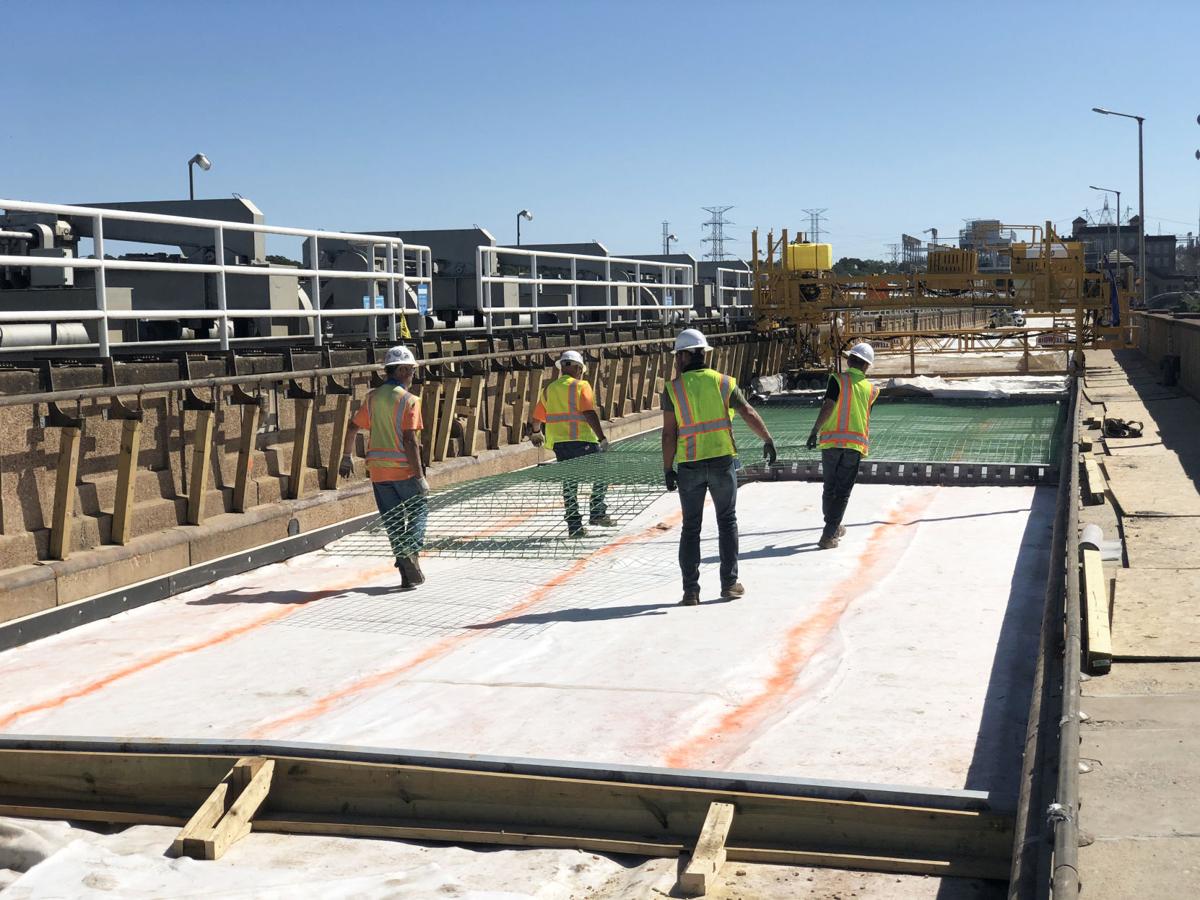
Renovation Overview
The Wilson Dam project included renovations to the dam structure, power-generating equipment, and significant bridge deck repairs. The bridge atop the dam connects Colbert and Lauderdale Counties and was originally constructed between 1918 and 1924. Though traffic slowed after the opening of the nearby Patton Island Bridge in 2008, TVA officials were eager to replace the 1950s-era concrete pavement.
“When the driving surface was removed in 2019, extensive damage was found. Cracks formed in the unreinforced concrete, allowing water to infiltrate and cause deterioration,” explains Byard. This led to the decision to resurface the bridge with internally cured concrete to extend its lifespan and reduce future maintenance needs.
Local Supplier
Matthew Moore, Quality Control Lead at CEMEX for the North Alabama region, says Ready Mix USA has extensive experience batching concrete with lightweight aggregate, most recently on a major new hospital which opened very near the Wilson Dam. But this project was somewhat unique. “We’ve used a lot of lightweight aggregate through the years and this project was a little different,” says Moore. “Basically, the internally cured concrete is designed to a weight and to an air spec and like I said, we have to take a little more care with the lightweight and make sure it’s kept wet at the plant.”
“The material does require additional handling, storage, and keeping it wet,” says Moore. “It has over 20% absorption, compared to about 1% for normal aggregates, so we closely monitored the moisture content and its impact on the mix.”
The concrete used in the renovation was batched from Ready Mix USA’s Florence Industrial Park plant. “For this job, we used the Florence plant on the north side of the river as our main facility, with Tuscumbia on the south side as backup,” says Moore.
Specifying Internal Curing
“It’s lightweight fine aggregate, similar to sand, that’s pre-soaked before batching the concrete,” explains Bill Wolfe, Marketing & Technical Manager at Arcosa Lightweight. “By replacing a portion of the concrete sand with pre-wet lightweight aggregate, internal moisture is provided to keep the hydration process going longer as the concrete cures.”
Wolfe also emphasized the performance benefits: “Internal curing reduces early-age shrinkage, which helps reduce cracking in the pavement and extends the service life of the structure.”
A Special Landmark
The Wilson Dam region is significant for the TVA, as it was the agency’s original headquarters when founded in 1933. “Helping restore Wilson Dam, the only neoclassical-style dam built by the U.S. Army Corps of Engineers in the TVA system, has been the highlight of my career,” says Byard.
The bridge reopened to traffic in December 2020, following completion of the renovations. Byard is confident in the project’s success: “If I’m doing a bridge deck, by golly, it’s going to be internally cured. For a relatively minor increase in cost, you get a lot more bang for your buck in performance.”
- The Issue: The 100-year-old bridge deck atop Wilson Dam, part of a historic hydroelectric dam, required extensive repairs due to severe cracking and deterioration. TVA sought to extend the bridge deck’s lifespan with modern materials and processes while maintaining the structure’s historic significance.
- What Arcosa Did: Arcosa supplied lightweight aggregate to CEMEX / Ready Mix USA, which produced internally cured concrete for the bridge deck. This innovative solution provided internal moisture that significantly improved the concrete’s strength, reduced cracking, and extended its service life.
- Why Lightweight Works: The lightweight fine aggregate used in the internally cured concrete helped retain moisture, allowing for a longer hydration process. This improved the mechanical performance of the concrete, ensuring increased durability and reduced maintenance needs over time.
- Result: Over 30,000 cubic yards of internally cured concrete were produced using Arcosa’s lightweight aggregate. The newly restored bridge deck, completed in December 2020, gains enhanced performance and durability.
- Key Quote: “The new surface is composed of reinforced ‘internally cured’ concrete, which should stand the test of time.” — Benjamin Byard, Bridge Program Manager, TVA
- Industry Context: Internally cured concrete allowed TVA to improve the bridge deck’s strength and durability while addressing long-term maintenance concerns. The lightweight aggregate provided the necessary moisture for internal curing, preventing early-age shrinkage and reducing cracking.
- Lessons Learned: Using lightweight aggregate for internally cured concrete offers long-term benefits, including increased lifespan, reduced cracking, and overall lower maintenance costs, making it ideal for large-scale infrastructure projects.
- Call to Action: Arcosa Lightweight’s solutions are ideal for projects requiring enhanced concrete durability and performance, particularly in historic renovations and critical infrastructure applications.
- Project: Wilson Dam Renovation
- Location: Muscle Shoals, Alabama
- Customer: CEMEX / Ready Mix USA
- Client: Tennessee Valley Authority (TVA)
- Project Size: 100-year-old hydroelectric dam, major bridge deck renovation
Key Insights:
Quick Facts:
•
•
•
How Arcosa Helped:
•
•
Final Results
Key Quote
Context:
•
•