Lightweight Aggregate Creates New Land for Cruise Ship Terminal
Lightweight Aggregate Creates New Land for Cruise Ship Terminal
Port Canaveral, one of the world’s busiest maritime operations, now operates an advanced docking berth capable of handling today’s larger cruise ships. To achieve this, Arcosa provided the lightweight aggregate needed to extend the port into the water, creating stable ground for the expanded infrastructure.
Jack Moore, Geotechnical Market Manager at Arcosa, explains, “Developers essentially created new land by extending the existing port into the water, using our lightweight aggregate to provide the necessary stability.”
Major Expansion
In 2012, Port Canaveral launched a $163-million campaign to improve and redevelop Cruise Terminal 3 (CT-3), which originally opened in 1983. A significant portion of this initiative included a $35-million rebuild of the existing wharf to accommodate today’s fleet of ultra-large cruise ships. The project began in 2018 with the demolition of an outdated, open-pile pier.
The new berth is a 1,309-foot-long facility designed for the Mardi Gras, the largest ship ever built for Carnival Cruise Line. The berth’s construction utilized expensive steel pipe and sheet piling. To ensure the project remained cost-effective, lightweight aggregate from Arcosa was used to fill behind the sheet piles.
“The low density and high internal friction angle of Arcosa’s lightweight aggregate played a crucial role in reducing lateral pressures on the sheet piles,” says Moore.
Lightweight aggregate weighs about half as much as traditional fill materials like quarried stone. This advantage, combined with its high internal friction angle, reduced lateral forces by more than half, contributing to the stability of the structure.
“Lightweight aggregate’s low density and high friction angle make it an ideal choice for reducing lateral earth pressures and applied vertical stresses,” Moore adds.
Product Placement
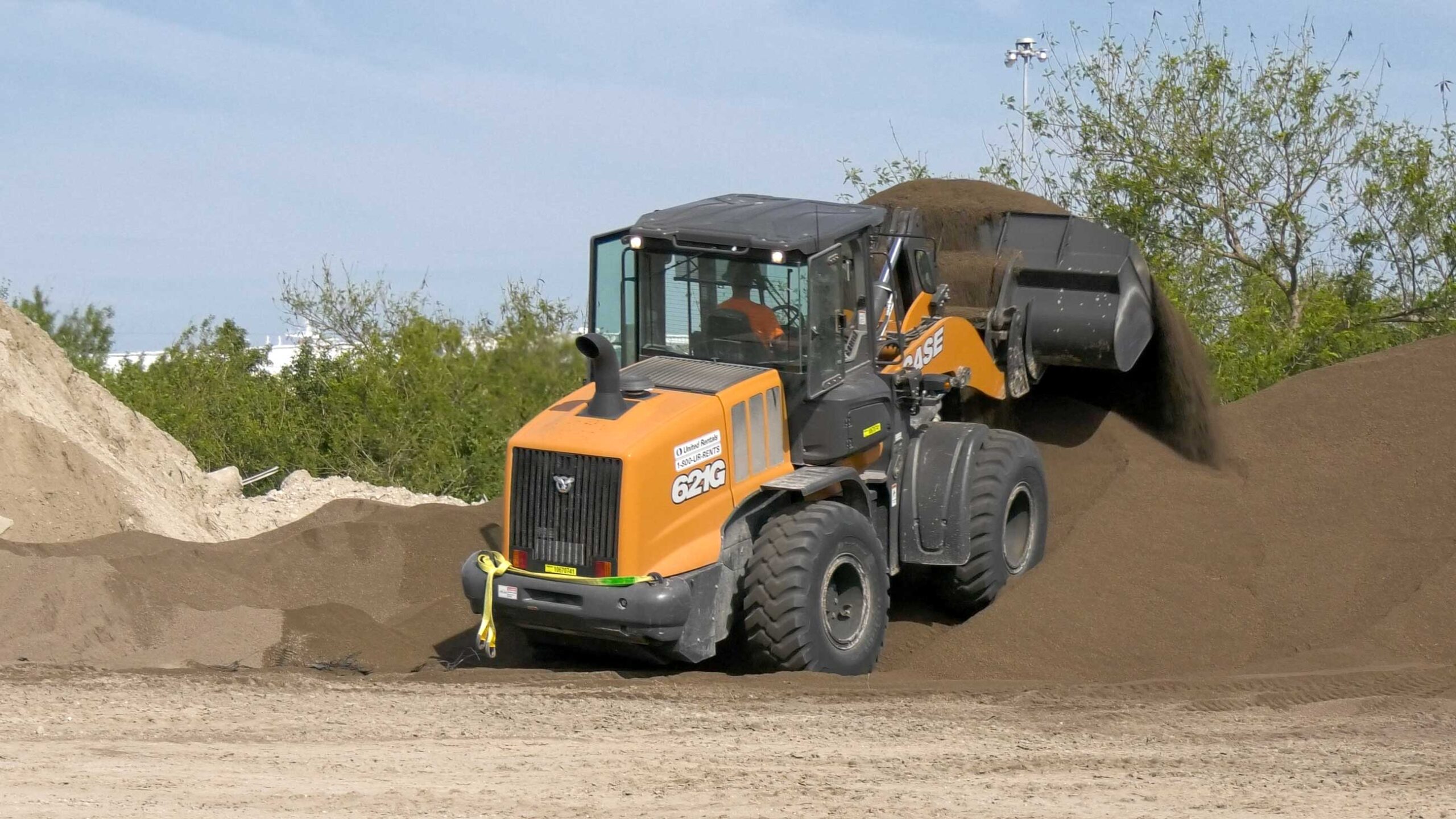
On the jobsite, lightweight aggregate does not require special handling procedures. Crews easily placed the material using standard loaders, rollers, and plate compactors.
“Compaction is quicker and requires fewer passes compared to conventional fill,” explains Moore. “This allowed for faster fill placement and higher efficiency on-site.”
For this project, lightweight aggregate was delivered by both rail and truck. The material traveled roughly 600 miles from Livingston, Alabama, to the site.
“We used 550 railcars to deliver approximately 60,000 cubic yards of lightweight aggregate,” says Moore. “Everything was coordinated smoothly, ensuring that delivery and placement went off without a hitch.”
Successful Completion
The new berth at Port Canaveral Cruise Terminal #3 incorporates steel pipe and sheet piling bulkhead walls, a steel pipe pile tieback A-frame, and monopile and multi-pile shore and offshore mooring dolphins. It now accommodates next-generation Oasis-class cruise ships, which span over 1,300 feet and hold more than 6,000 passengers and 2,000 crew members.
Additional Case Studies
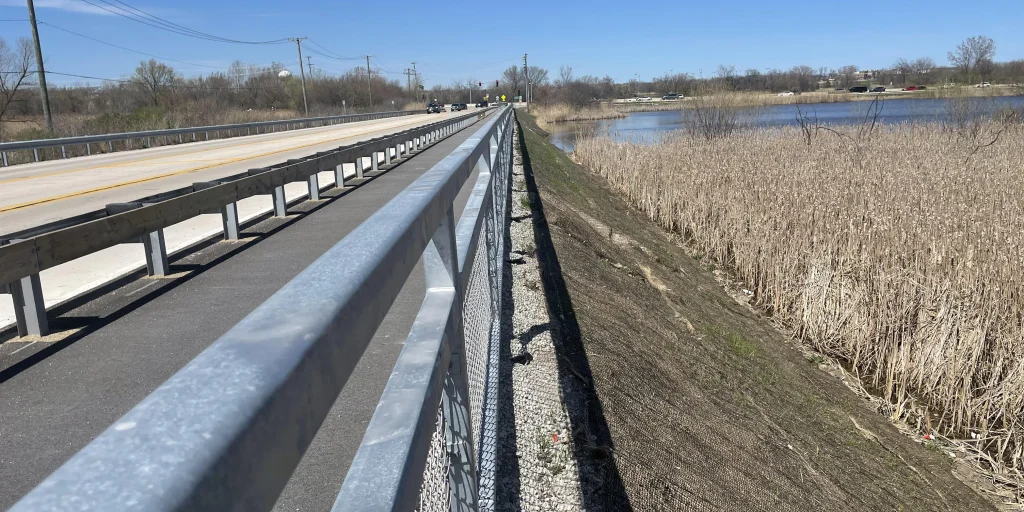
Expanded Bike Trail Benefits from Innovative Use of Lightweight Aggregate
Bike riders in Orland Park, IL, a suburb near Chicago, have an expanded bike trail thanks to Arcosa’s lightweight aggregate, supplied by the company’s Brooklyn, Indiana plant. Orland Park is a growing area committed to improving recreational facilit…
Read More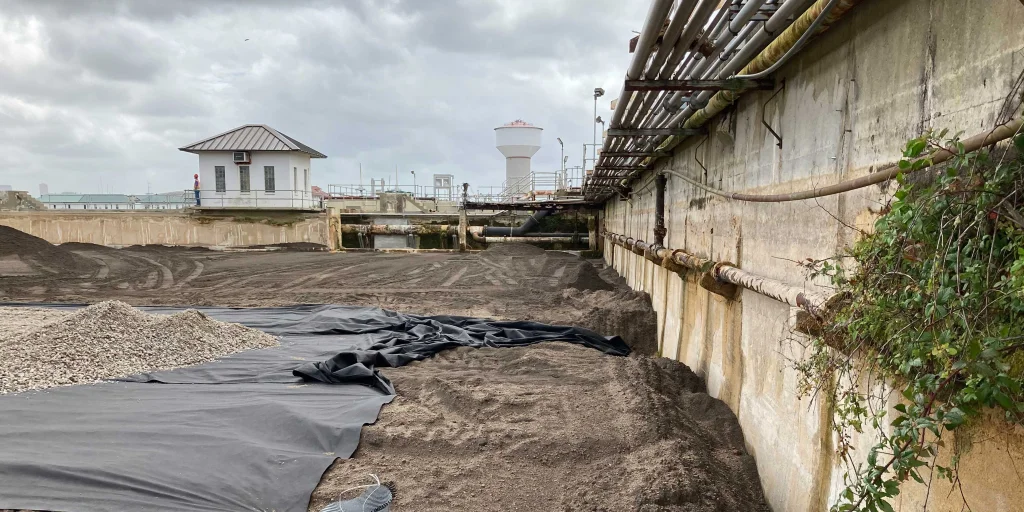
Modernizing Infrastructure at the Carrollton Water Plant
The Carrollton Water Plant, a critical infrastructure asset for the east bank of Louisiana’s Orleans Parish, supplies around 135 million gallons of treated water daily to homes across New Orleans. Arcosa Lightweight stabilized the land for a new ded…
Read More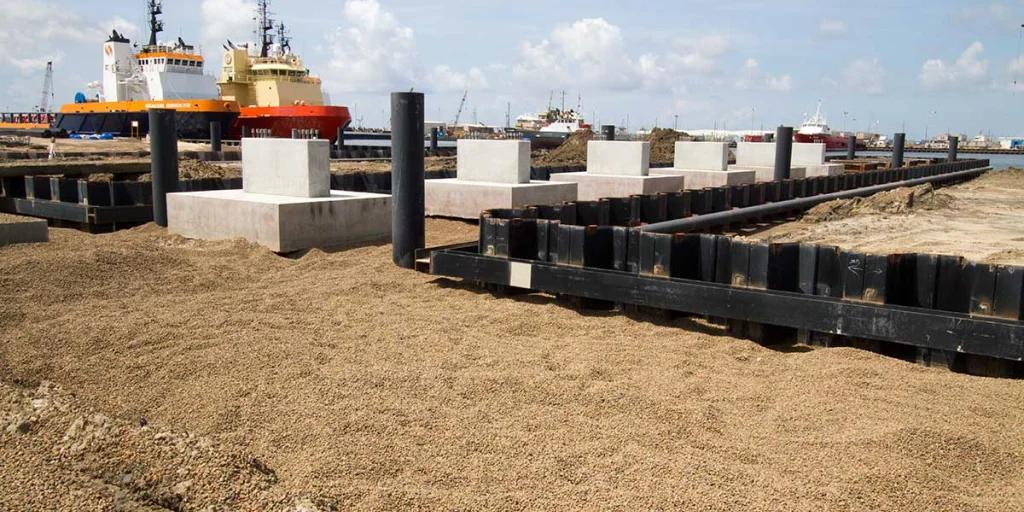
Arcosa Lightweight Aggregate Used to Create Vital Port Space
Arcosa Lightweight is frequently used in expansion projects that create vital port space along the southern tip of Louisiana. The most recent expansion project at Port Fourchon, located in Lafourche Parish, created 300 new acres for development and…
Read More