Recap: Lafayette Consolidated Government’s Strategy to Implement Internal Curing
- Home
- Industry News
- Recap: Lafayette Consolidated Government’s Strategy to Implement Internal Curing
Quick Insights
Learn More
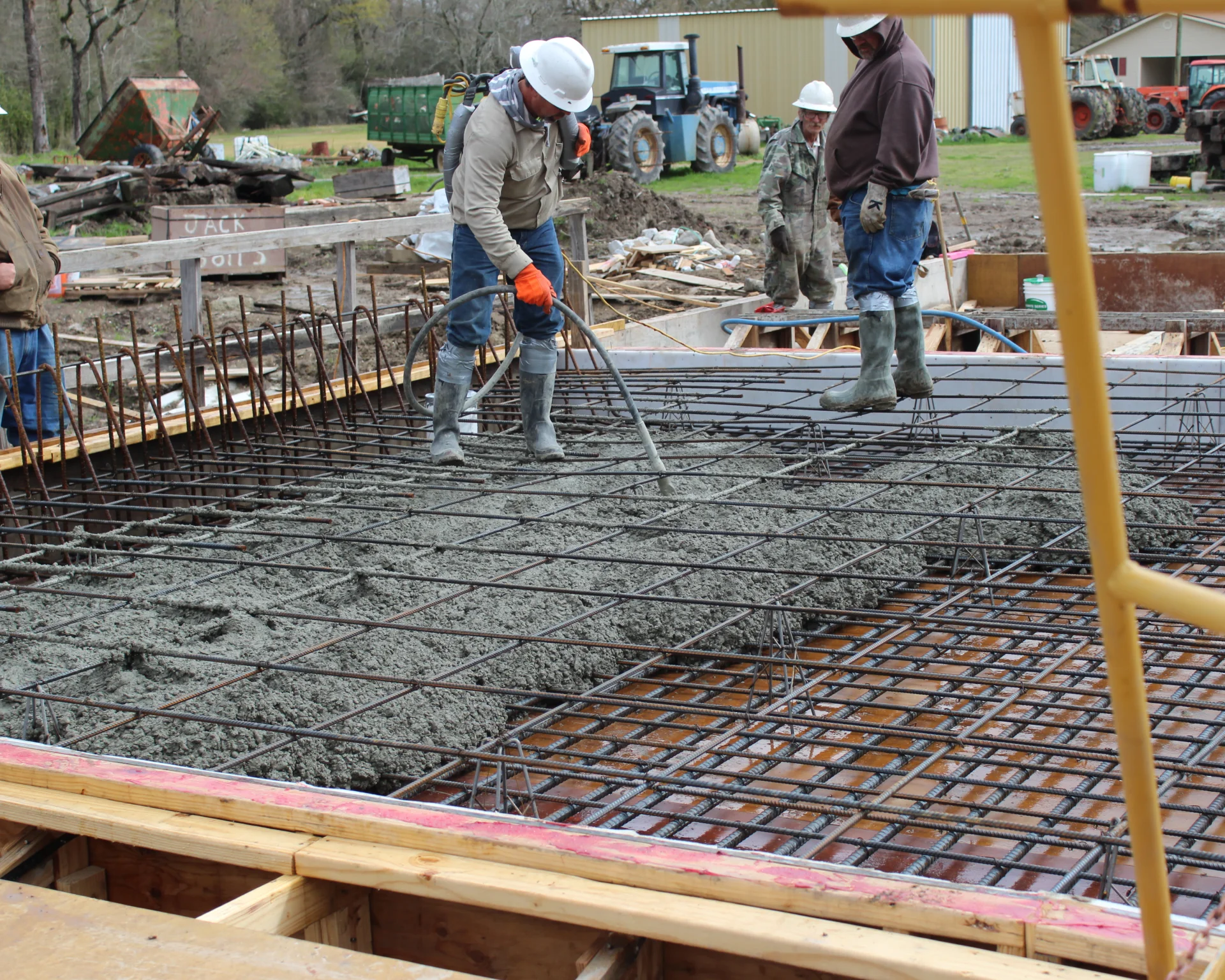
Recap: Lafayette Consolidated Government’s Strategy to Implement Internal Curing
Last Updated: Dec 10, 2024
In October 2024, the Enhancing Performance with Internally Cured Concrete (EPIC2) initiative hosted a national webinar titled “Implementation of Internal Curing by a Local Agency,” spotlighting the successful application of internal curing (IC) in bridge projects across Lafayette, Louisiana.
The session featured insights from Alison C. Lognion, M.S., P.E., Engineer III and Manager at the Lafayette Consolidated Government, and Tyson D. Rupnow, Ph.D., P.E., Associate Director of Research at the Louisiana Transportation Research Center (LTRC). Moderated by Tim Barrett of FHWA’s Turner-Fairbank Highway Research Center, the webinar demonstrated how IC has transformed bridge construction in Lafayette by reducing shrinkage cracking, extending service life, and lowering maintenance costs.
Key Takeaways from the Presentation
The Success of Internal Curing on Lafayette’s Bridge Network
During her presentation, Alison C. Lognion shared that initially, her agency implemented internal curing on six bridges over a three-year period. Since then, they have constructed an additional five bridges with IC.
“We have had multiple different contractors working with the internally cured aggregate, and all of them say the same thing: [it] looks, feels, works like regular concrete, and it actually is easier to work with than regular concrete,” Lognion said.
All of these structures have exhibited remarkably low rates of cracking.
“We went back recently to go look at these bridges and do a crack survey. Out of all the bridges mentioned, including these, and five or six others since then, we found six total cracks in all these 11 bridges. And we were shocked. We didn’t expect it. In our first pilot project on West Congress Street, the first bridge, you could see the difference in shrinkage cracking on the control sections versus the ICC sections. It was very clear; you didn’t have to know where ICC was. It was very clear out in the field where ICC was used because of the non-existent cracking.”
Lognion added, “We have many bridges coming out now, and the contractors are used to supplying these mix designs with internally cured concrete.”
Rupnow highlighted Louisiana’s use of internal curing as a model for turning research into a real-world application.
“We’ve completed nearly 600 research projects over the course of the last 40 years of existence,” Rupnow noted, “and this is one of the best examples of implementation in recent years, where somebody took our results and applied them appropriately in the field.”
This statement underscores IC’s role as a high-impact solution, significantly reducing cracking and enhancing the resilience of bridge structures under high traffic loads, while demonstrating how well-executed research can address infrastructure challenges in practical, lasting ways.
Longevity Predictions and Maintenance Savings
Service life modeling from LTRC suggests that IC-treated bridges could exceed a 100-year lifespan, yielding substantial taxpayer benefits and significant maintenance savings for the Lafayette Department of Public Works.
According to Rupnow, “In some of the limited modeling we’ve done, we truly believe that Lafayette Consolidated Government is going to have these structures with service lives, with their resistivity requirements, with their ICC requirements, and the significant reduction in cracking that they’re seeing. We believe they’re going to see service life exceeding 100 years. Modeling showed numbers, in most cases, exceeding 125 years of predicted service life. These structures are going to be there for a lifetime, you know, a true lifetime.”
Practical Insights and Lessons Learned
Adjustments in Curing Practices for Hot Climates
Due to Louisiana’s extreme heat and humidity, traditional 14-day wet curing practices are challenging to maintain.
“When we did the pilot project, we were at a pigmented curing compound covered with a 14-day wet burlap cure requirement. Since then, they’ve stripped off the curing compound because it only allowed water to go one direction: through it,” Rupnow said. “They realized their fallacy there, and so they changed the specs, and then they retained a 14-day wet cure for a period of time.”
Rupnow continued, “Construction got involved about four years ago, and they basically stated, our contractors aren’t wet curing for 14 days. It’s nearly impossible to do. It’s really costly. And so that has been changed to 10 or seven days now. And a lot of the work that we’ve done, we believe that we can probably reduce that to a three-day wet cure, and then after they pull the burlap, spray it with a white pigmented curing compound for the remainder, just because that internally cured aggregate is providing that cure water.”
Effective Techniques for Aggregate Saturation
The speakers emphasized that proper saturation of lightweight aggregates is crucial to the success of IC. They discussed effective methods, including using sprayers or specialized four-sided bins with drains to achieve optimal saturation levels.
“One producer… decided to get a four-sided bin and put his aggregate in there to super saturate it… it was a super simple method,” Lognion explained.
She added that they observed no significant difference in results, whether the ready mix producer used sprinklers or an enclosed bin for saturation. “As long as they’re following the ASTM standards and preparing the aggregate to be super saturated and then drained out, it provides the capacity to reduce autogenous shrinkage. But we haven’t seen any difference from the owner’s standpoint.”
Testing Procedures and Ensuring Consistency
Lognion emphasized the agency has a strict requirement that the centrifuge method be used in testing procedures to ensure accurate measurement of aggregate moisture. This approach, which involves spinning aggregate samples at high speed to remove excess water, ensures the aggregate reaches a saturated surface dry (SSD) state, crucial for maintaining proper water-cement ratios in IC applications.
Addressing Other Common Concerns and Questions
Pumpability of Internally Cured Concrete
Lognion affirmed that IC performs comparably, if not better, than traditional concrete in terms of workability and pumping ease.
“It’s normal concrete,” she noted. “It actually finishes better than normal concrete. But as far as pumpability, all of the bridges that I mentioned, I’ve seen some in construction, some just from a manager point of view, but I’ve been there when they pumped multiple decks, and they poured all the barrier rails, and done the approach slabs, and I’ve never seen an issue from the pumps.”
Durability Under Heavy Traffic and Freeze-Thaw Conditions
Lognion confirmed that IC-treated bridges in Lafayette experience heavy loads from sugar cane haulers and hold up well under these conditions.
“We have a lot of sugar cane around the West Congress Street Bridge,” she said. “And that’s heavy, heavy loading. It’s about to be harvest season, and you just know, these cane trucks, most likely are overloaded.”
Opportunities for Wider Adoption
Both LTRC and FHWA are committed to supporting the wider adoption of IC across U.S. infrastructure projects. For those interested in firsthand experience, David North from LADOTD’s Shreveport district has offered to conduct guided tours of the US 80 bridge to showcase IC’s benefits in action.
“He is a very forward-thinking gentleman,” said Rupnow. “Loves innovation and research, and he’s fully on board. When he offers that, I will tell you that is a true offer, and I would probably join whoever wishes to go, just so I can go look at the deck again.”
Conclusion
The EPIC2 webinar provided an in-depth look at how Lafayette’s adoption of internal curing has set a new standard for durable, low-maintenance bridge infrastructure. The success of IC in Lafayette, backed by research from LTRC, offers a model for other municipalities interested in reducing maintenance cycles and improving the longevity of concrete structures.