A Look Back at the Union Pacific Dallas Intermodal Terminal (DIT)
A Look Back at the Union Pacific Dallas Intermodal Terminal (DIT)
The Union Pacific Dallas Intermodal Terminal (DIT) project stands as a testament to the transformative benefits of lightweight aggregate in improving the durability, strength, and overall performance of concrete paving. Notably, it remains one of the largest internal curing paving projects in the United States, with over 250,000 cubic yards of concrete used.
Located south of Dallas, Texas, this expansive facility endures daily use by heavy trucks transporting millions of tons of cargo annually. The DIT supports numerous businesses that depend on intermodal rail freight to export Texas-made products and receive global imports.
Reflecting on the project’s success, Clint Chapman, Western Region Marketing & Technical Manager at Arcosa Lightweight, shared insights into the innovative approach taken during construction:
Construction Highlights
The construction phase presented a range of challenges, spanning Texas’ seasonal extremes from cold, wet conditions to hot, dry climates. Despite these environmental variations, the 3-inch maximum slump concrete mix proved easy to place and finish, consistently exceeding expectations. The specified 28-day compressive strength surpassed its target by an average of 1000 PSI, and the 28-day flexural strength was achieved within just 3 days.
The UP DIT pavement was also among the first large-scale concrete paving projects to utilize internal curing techniques.
In a 2007 Concrete international article entitled Better Pavements Through Internal Hydration, Victor H. Villarreal, P.E., MBA, FACI (now with Master Builders Solutions) noted that the 2005 paving project used concrete from a double central-mix batch plant set up at the site.
Villarreal wrote that the Union Pacific project was, at the time, “the largest project in the world that took advantage of the internal hydration concept of prewetted lightweight aggregate in low-slump paving.” and that “in contrast to conventional paving mixtures, cracking has been extremely minimal.” He goes on to say:
How Internal Curing for Pavements Differ
Concrete mixtures typically utilized for rigid pavements typically have a lower cement content than bridge deck concrete mixtures.
In the report Evaluation of Internally Cured Concrete for Paving Applications, researchers Chetana Rao, Ph.D., and Michael I. Darter, Ph.D., P.E. concluded that:
These effects when combined lead to significant positive impact on slab fatigue damage and slab cracking in jointed concrete pavements.
Thanks to this method, and the superior performance of the concrete mix, the pavement remains virtually crack-free after years of continuous use.
Additional Case Studies
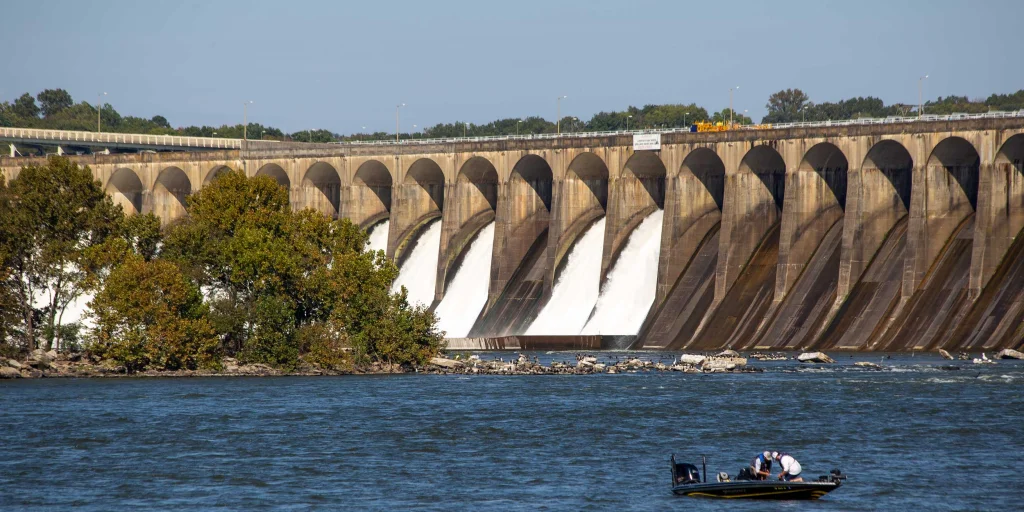
TVA Utilizes Internal Curing for Historic Hydroelectric Dam’s Bridge Deck
The Wilson Dam bridge deck, part of the iconic 100-year-old hydroelectric dam on the Tennessee River in Muscle Shoals, Alabama, is ready handle another century of traffic. Arcosa Lightweight’s material played a pivotal role in these extensive repair…
Read More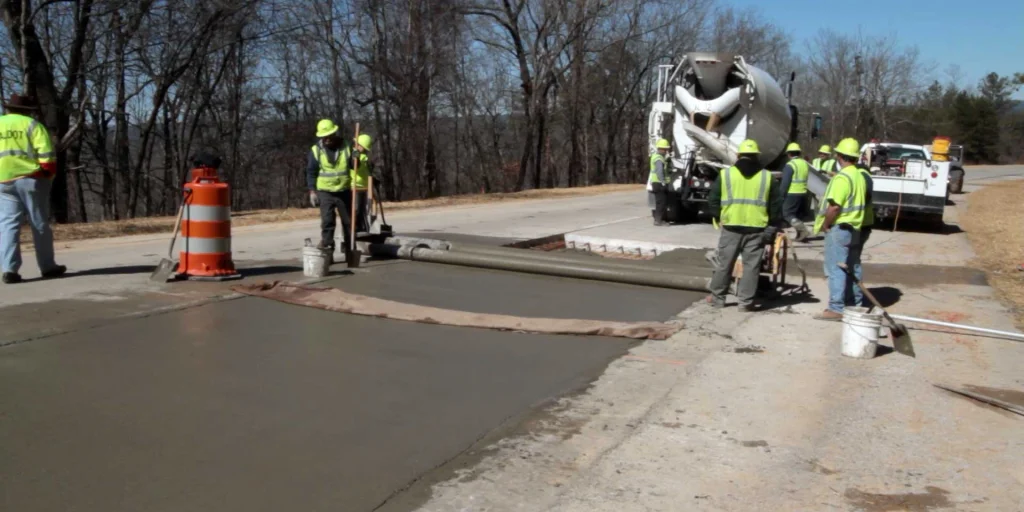
Internal Curing Gains Ground in Highway Construction: A Durable Solution
Internal curing is being recognized as a significant advancement in concrete technology. Today, the integration of lightweight aggregate (LWA) into concrete offers enhanced performance by reducing cracking, improving durability, and extending the se…
Read More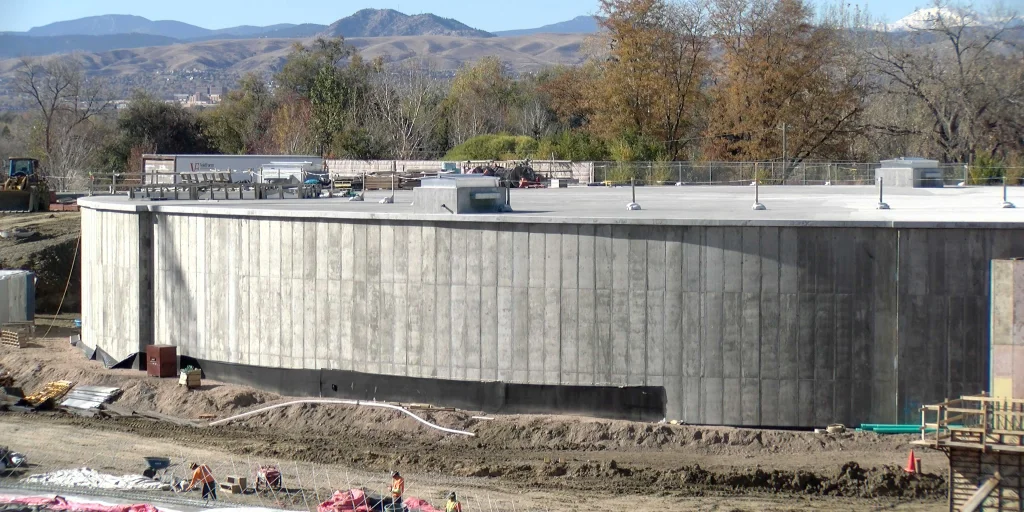
Internally Cured Concrete Enhances Water Tank Durability in Denver Water Projects
Denver Water is committed to ensuring safe and reliable water for its customers. To achieve this, the utility continually upgrades its system by replacing aging, large-capacity water storage tanks with more durable designs that are less susceptible…
Read More