Concrete Make with Arcosa Lightweight Lifts Chicago’s River Point Tower
Concrete Make with Arcosa Lightweight Lifts Chicago’s River Point Tower
River Point, a 52-story skyscraper soaring 730 feet (213 meters) above Chicago’s West Loop, stands as a testament to the strength and versatility of lightweight concrete. Completed in 2016, the building features 1 million square feet of office space and is located at 444 West Lake Street, between Canal Street and the Chicago River. The building’s iconic parabolic arch at the base is a result of angled support columns designed to accommodate the unique site.
The construction of River Point dispels a common misconception about lightweight concrete: that it is difficult to pump at great heights. Despite the challenging task of delivering concrete 52 stories above the city, crews encountered no issues placing Arcosa Lightweight’s structural concrete across the tower’s floors.
“Lightweight concrete has been pumped some pretty far distances,” says Clint Chapman of Arcosa. “This project is a great example of how, when proportioned and pumped correctly, it can reach impressive heights without difficulty.”
Strong and Fire Resistant
In high-rise construction, each floor must not only support the loads imposed by the levels above, but also meet strict fire-resistance requirements.
“Most lightweight concrete has a built-in fire rating, so it eliminates the need for spray-on fireproofing on the backside of the deck,” explains Chapman. “That’s one of the key benefits to designing with structural lightweight concrete.”
For River Point, Ozinga Chicago supplied lightweight concrete for the building’s slab on metal deck floor system. The mix was specified to reach a compressive strength of 4,000 psi at 28 days and maintain a maximum equilibrium density of 115 pounds per cubic foot. Thanks to its lower heat conductance, lightweight concrete delivers the necessary fire resistance with about one-third less thickness compared to normal weight concrete. Coupled with a density reduction of about 20%, the system reduced floor dead loads by approximately 45%.
Self-Consolidating Concrete
The lightweight concrete used in the Lake Street project also incorporated a self-consolidating concrete (SCC) mixture, which employed a high-range water-reducing admixture, three additional chemical admixtures, and Class C fly ash. The purpose of using SCC was to create a concrete mix that could spread without vibration, making it fluid enough for easy placement at the pump discharge. To further reinforce the structure, steel fibers were added at a rate of 35 pounds per cubic yard.
Challenging Configuration
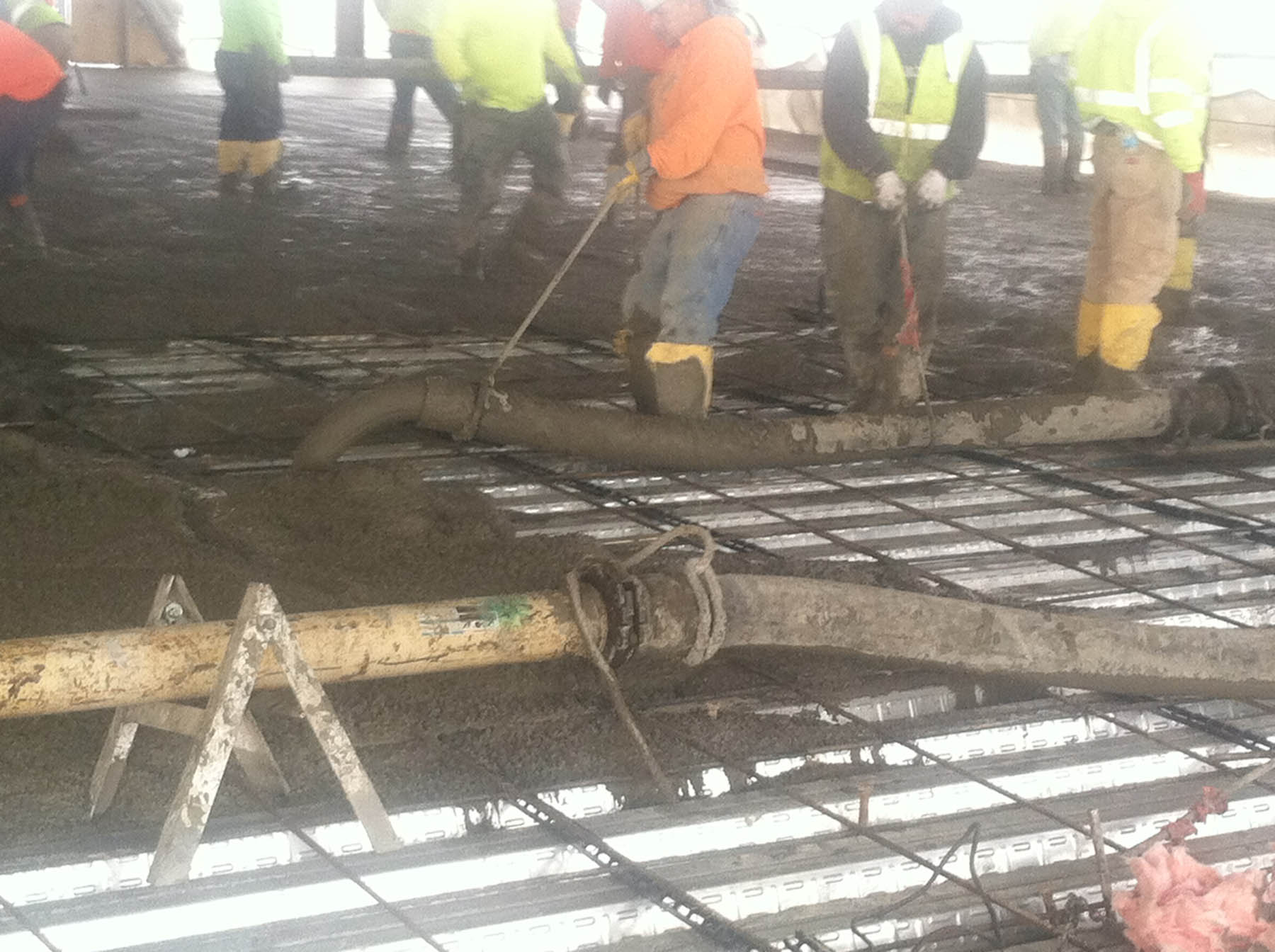
The configuration of the pumping system was a unique challenge. All lightweight, fiber-reinforced SCC was pumped using a stationary Schwing concrete pump . The operation required a 5-inch steel slick line with no reducers, but the route to the upper floors included 16 to 18 elbows, adding extra vertical height due to the bends. At the discharge end, a 5-inch rubber hose was used to direct the concrete into place.
“It was a pretty challenging pump configuration,” says Scott Kelly, Assistant Manager of Quality Control at Ozinga. “But it was the best option for going up 52 floors without losing too much slump—and for keeping the concrete workable and placeable.”
No Unusual Challenges
According to Kelly, the River Point project didn’t pose any unusual challenges for Ozinga, which has extensive experience working on downtown high-rises. “Staging trucks in congested areas, managing time constraints, and overseeing delivery logistics are routine for us,” Kelly says. “Everything went smoothly and according to specification.”
Designed by Pickard Chilton Architects, River Point earned LEED Platinum certification in 2018, further demonstrating the sustainability of the tower. The building is co-owned by Ivanhoé Cambridge, a global real estate investment firm. In addition to its iconic parabolic arch and striking riverfront location, the tower also features a 1.5-acre public park and a landscaped riverwalk—both open to the public—as required by the City of Chicago.
The success of River Point demonstrates the capabilities of structural concrete in overcoming logistical and technical challenges in skyscraper construction. With its strong fire resistance, reduced dead load, and efficient pumpability, lightweight concrete continues to redefine what’s possible for high-rise buildings.
Additional Case Studies
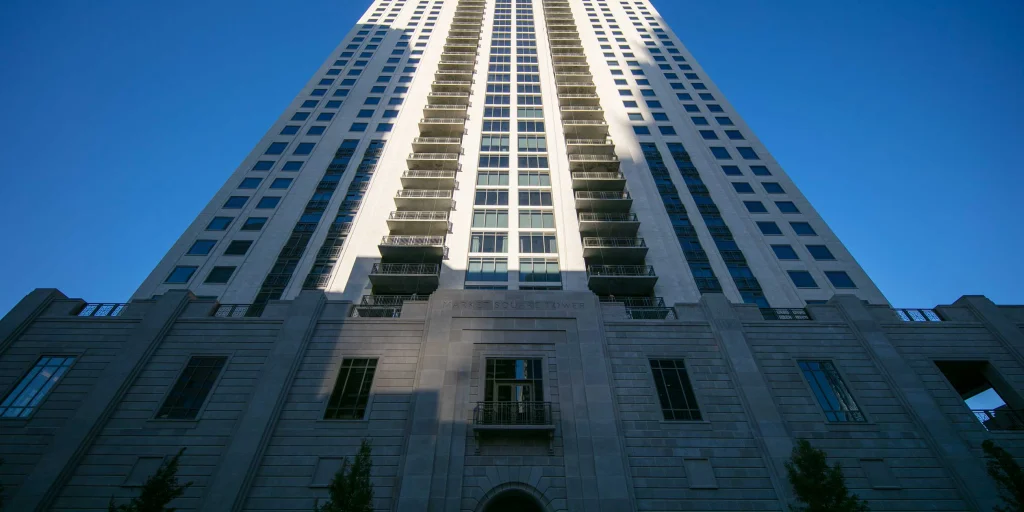
Structural Lightweight Concrete Elevates Houston’s Skyline
Market Square Tower, a 40-story residential building, rises 502 feet over downtown Houston, Texas and features 463 luxury apartments. The impressive height of the skyscraper was made possible through the use of structural lightweight concrete, which…
Read More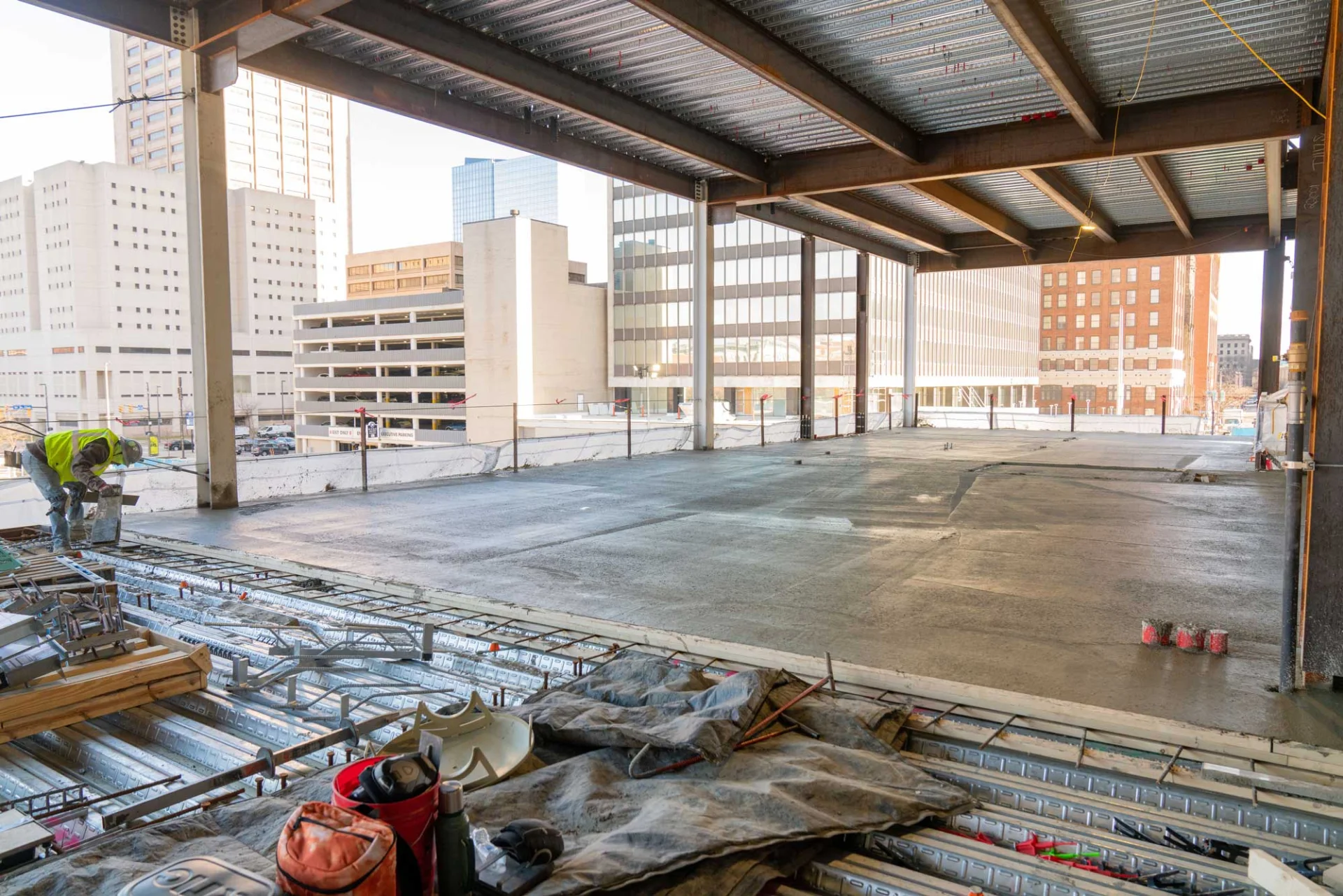
Sherwin-Williams’ Global Headquarters: Lightweight Concrete for a Landmark Project
Sherwin-Williams is constructing its new global headquarters in Cleveland, Ohio, a development that will feature a two-story pavilion, a 36-floor office tower, and a multi-level parking garage. The project, which will redefine the Cleveland skyline…
Read More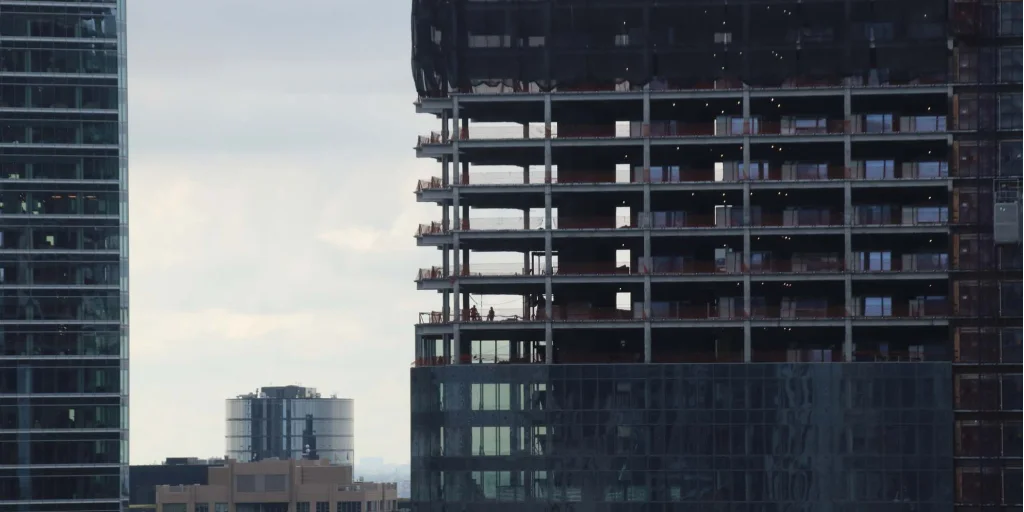
case-studies/structural-lightweight-concrete/salesforce-tower-chicago
Salesforce Tower Chicago, standing at an impressive 60 stories above the Chicago River, is a groundbreaking project in more ways than one. As the first building in the city to require and measure Environmental Product Declarations (EPDs) to quantify…
Read More