High Rises
Concrete Make with Arcosa Lightweight Lifts Chicago’s River Point Tower
- Teaser:River Point, a 52-story skyscraper soaring 730 feet (213 meters) above Chicago’s West Loop, stands as a testament to the strength and versatility of lightweight concrete. Completed in 2016, the building features 1 million square feet of office space and is located at 444 West Lake Street, between Canal Street and the Chicago River. The building’s iconic parabolic arch at the base is a result of angled support columns designed to accommodate the unique site.
- Article Body Text:
The construction of River Point dispels a common misconception about lightweight concrete: that it is difficult to pump at great heights. Despite the challenging task of delivering concrete 52 stories above the city, crews encountered no issues placing Arcosa Lightweight’s structural concrete across the tower’s floors.
“Lightweight concrete has been pumped some pretty far distances,” says Clint Chapman of Arcosa. “This project is a great example of how, when proportioned and pumped correctly, it can reach impressive heights without difficulty.”
Strong and Fire Resistant
In high-rise construction, each floor must not only support the loads imposed by the levels above, but also meet strict fire-resistance requirements.
“Most lightweight concrete has a built-in fire rating, so it eliminates the need for spray-on fireproofing on the backside of the deck,” explains Chapman. “That’s one of the key benefits to designing with structural lightweight concrete.”
For River Point, Ozinga Chicago supplied lightweight concrete for the building’s slab on metal deck floor system. The mix was specified to reach a compressive strength of 4,000 psi at 28 days and maintain a maximum equilibrium density of 115 pounds per cubic foot. Thanks to its lower heat conductance, lightweight concrete delivers the necessary fire resistance with about one-third less thickness compared to normal weight concrete. Coupled with a density reduction of about 20%, the system reduced floor dead loads by approximately 45%.
Self-Consolidating Concrete
The lightweight concrete used in the Lake Street project also incorporated a self-consolidating concrete (SCC) mixture, which employed a high-range water-reducing admixture, three additional chemical admixtures, and Class C fly ash. The purpose of using SCC was to create a concrete mix that could spread without vibration, making it fluid enough for easy placement at the pump discharge. To further reinforce the structure, steel fibers were added at a rate of 35 pounds per cubic yard.
Challenging Configuration
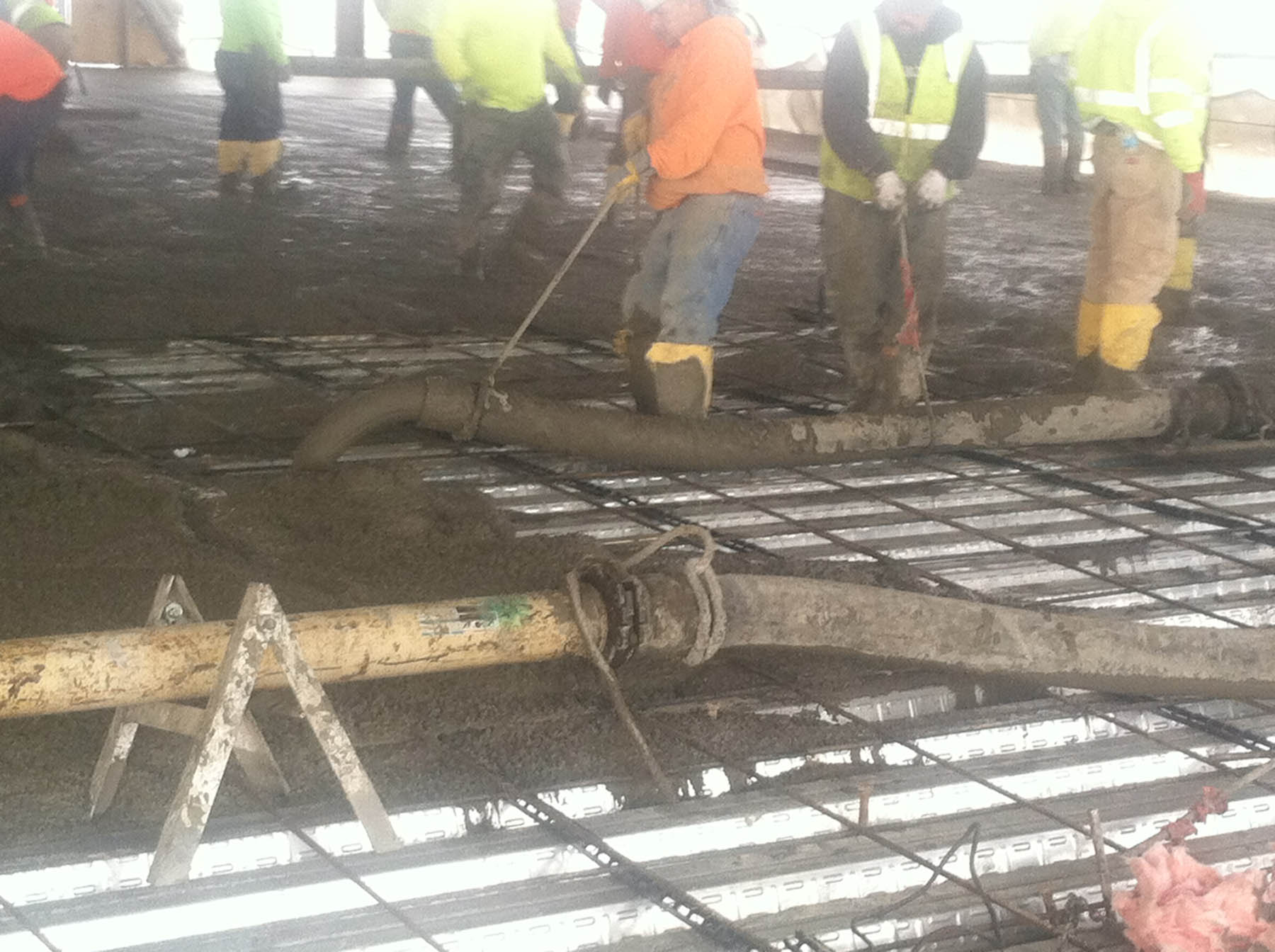
The configuration of the pumping system was a unique challenge. All lightweight, fiber-reinforced SCC was pumped using a stationary Schwing concrete pump. The operation required a 5-inch steel slick line with no reducers, but the route to the upper floors included 16 to 18 elbows, adding extra vertical height due to the bends. At the discharge end, a 5-inch rubber hose was used to direct the concrete into place.
“It was a pretty challenging pump configuration,” says Scott Kelly, Assistant Manager of Quality Control at Ozinga. “But it was the best option for going up 52 floors without losing too much slump—and for keeping the concrete workable and placeable.”
No Unusual Challenges
According to Kelly, the River Point project didn’t pose any unusual challenges for Ozinga, which has extensive experience working on downtown high-rises. “Staging trucks in congested areas, managing time constraints, and overseeing delivery logistics are routine for us,” Kelly says. “Everything went smoothly and according to specification.”
Designed by Pickard Chilton Architects, River Point earned LEED Platinum certification in 2018, further demonstrating the sustainability of the tower. The building is co-owned by Ivanhoé Cambridge, a global real estate investment firm. In addition to its iconic parabolic arch and striking riverfront location, the tower also features a 1.5-acre public park and a landscaped riverwalk—both open to the public—as required by the City of Chicago.
The success of River Point demonstrates the capabilities of structural concrete in overcoming logistical and technical challenges in skyscraper construction. With its strong fire resistance, reduced dead load, and efficient pumpability, lightweight concrete continues to redefine what’s possible for high-rise buildings.
- The Issue: The project required placing lightweight concrete over 52 stories while maintaining consistency and fire resistance in a challenging urban environment.
- What Arcosa Did: Structural lightweight concrete was pumped across the building’s floors, reducing dead loads and providing built-in fire resistance.
- Why Lightweight Works: The lightweight concrete allowed for thinner slabs and reduced the need for additional fireproofing, improving overall efficiency while ensuring strength.
- Result: River Point stands as a sustainable, iconic structure with a LEED Platinum certification and a public park and riverwalk over active rail lines.
- Key Quote: “This project is a great example of how, when proportioned and pumped correctly, lightweight concrete can reach impressive heights without difficulty.” – Clint Chapman, Arcosa Lightweight
- Industry Context: Pumping lightweight concrete over great heights can be challenging, but modern pumping technology and prewetting the aggregate ensure successful placement.
- Lessons Learned: Structural lightweight concrete provides a fire-resistant solution that reduces floor dead loads, creating efficiency in high-rise construction.
- Call to Action: Discover more ways Arcosa Lightweight supports high-rise developments with innovative concrete solutions.
- Project: River Point Tower
- Location: Chicago, Illinois
- Customer: Ozinga
- Client: Pickard Chilton
- Project Size: 52 stories, 730 feet (213 meters)
Quick Facts:
•
•
•
Key Insights:
Quick Facts:
•
•
•
How Arcosa Helped:
•
•
Final Results
Key Quote
Context:
•
•
Explore Further
Additional Case Studies
HydroLite Lightweight Aggregate Plays Key Role in Record-Breaking Structure
- Teaser: Wilshire Grand Center, which stands at an impressive 1,100 feet, is recognized as one of the tallest buildings in the western United States. The project’s engineers needed to significantly reduce the building’s overall weight to achieve this height, which is why they opted for structural lightweight concrete.
- Article Body Text:
With over 15,000 cubic yards of lightweight aggregate used in the concrete mix—10,000 cubic yards of which incorporated Arcosa’s HydroLite® vacuum saturated lightweight aggregate—the project achieved not only the necessary height but also critical fire resistance and improved pumpability, allowing for more efficient construction.
The structural design of the building incorporates multiple lightweight concrete slabs, with lightweight concrete poured on metal decking to form the floors and core, spanning over 1.2 million square feet across the entire tower.
Pumping No Issue for Lightweight Concrete
The ability to pump lightweight concrete all the way up to project’s soaring height was key to the successful completion of the building, which now features 900 hotel rooms, a 70th-floor sky lobby, and 445,000 square feet of office and retail space.
According to Clint Chapman, Western Region Marketing & Technical Manager for Arcosa Lightweight, the lightweight concrete used for the project was pumped at heights of 1,300 feet, with 1,100 feet of that being vertical pumping.
“The fact that our HydroLite is presoaked made pumping it up to the building’s very high floors more efficient compared to traditional materials,” explains Chapman.
HydroLite® is a vacuum saturated lightweight aggregate produced by Arcosa Lightweight. This process allows the aggregate to absorb water, providing improved pumpability, reduced slump loss, and better consistency during placement. The vacuum saturation also enables the aggregate to maintain internal moisture, contributing to better curing and minimized cracking in the concrete.
Chapman also notes that the LWC used for the project also helped achieve the project’s strict fire rating requirements without needing additional fireproofing layers.

Placement Team
Turner Construction, the general contractor, led the build, with Conco Cement Company handling the concrete pumping, and Catalina Pacific Concrete, a division of CalPortland, providing the ready-mix. Arcosa Lightweight supplied the lightweight aggregate for the concrete that was used on the metal decking surrounding the building’s core and elevator towers.
Arcosa’s structural lightweight aggregate was manufactured at its Frazier Park, California plant, with the ready-mix supplier replacing standard weight granite with the lighter HydroLite aggregate.
“The HydroLite reduces the concrete’s unit weight from 147 pounds per cubic foot to just 115 pounds per cubic foot,” Chaman notes.
Exceeding Expectations Through Teamwork
The Wilshire Grand Center project is a prime example of exceptional collaboration among the general contractor, the ready-mix concrete supplier, the concrete placement subcontractor, the pumping subcontractor, and the lightweight aggregate supplier.
“This project showcases the value of a cohesive team,” says Chapman. “Everyone worked together seamlessly to ensure the success of this monumental build.”
- The Issue: Reducing the building’s overall weight to achieve the height of the tallest structure in the western U.S., while ensuring that the lightweight concrete could be efficiently pumped to extreme heights during construction.
- What Arcosa Did: Supplied HydroLite® Lightweight Aggregate to produce over 10,000 cubic yards of lightweight concrete.
- Why Lightweight Works: Lightweight concrete helped reduce the building’s overall weight, met fire rating requirements without additional fireproofing, and allowed for efficient pumping to heights of over 1,100 feet.
- Result: The use of structural lightweight concrete enabled the successful construction of the tallest building in the western United States, reducing material weight while meeting key fire safety and engineering requirements.
- Key Quote: “The fact that our HydroLite is presoaked made pumping it up to the building’s very high floors more efficient compared to traditional materials.” — Clint Chapman, Western Region Marketing & Technical Manager for Arcosa Lightweight
- Industry Context: Structural and fire safety requirements needed to be balanced with the demand for efficient construction.
- Lessons Learned: Lightweight concrete not only meets engineering needs but also improves project logistics by facilitating easier material handling and placement at extreme heights.
- Call to Action: Learn more about the use of HydroLite® Lightweight Aggregate in high-rise construction at Arcosa Lightweight.
- Project: Wilshire Grand Center
- Location: Los Angeles, CA
- Customer: Catalina Pacific Concrete
- Client: Hanjin Group
- Project Size: 15,000+ cubic yards of structural lightweight concrete on metal deck
Key Insights:
Quick Facts:
•
•
•
How Arcosa Helped:
•
•
Final Results
Key Quote
Context:
•
•
Explore Further
Additional Case Studies
Salesforce Tower Chicago: Pioneering Sustainability with Structural Lightweight Concrete
- Teaser:
Salesforce Tower Chicago, standing at an impressive 60 stories above the Chicago River, is a groundbreaking project in more ways than one. As the first building in the city to require and measure Environmental Product Declarations (EPDs) to quantify embodied carbon of construction materials, this achievement is largely attributed to the use of structural lightweight concrete. - Article Body Text:
“We worked with one of the largest ready-mix producers in Chicago, and despite site access limitations, they successfully adjusted the mix design to maintain the specified unit weight while pumping lightweight concrete to 60 stories without issue,” says Kevin Cavanaugh, Sales and Marketing Representative for Arcosa Lightweight.
The Role of Structural Lightweight Concrete in High-Rise Construction
Structural lightweight concrete (LWC), made with expanded clay or shale (ESC) aggregate, is a tried-and-true solution for commercial building construction. It not only addresses weight and durability concerns but also provides significant cost savings. Thanks to the use of LWC, fewer construction materials were required, and the construction schedule was accelerated.
LWC allows for thinner gauge steel decking, fewer steel beams, and thinner concrete slabs, due to its superior fire resistance. If normal weight concrete (NWC) had been used instead, additional steel beams and thicker slabs would have been required to meet fire resistance standards, increasing the dead load and complicating the construction process.
In fact, using NWC would have required thicker steel decking to provide the necessary stiffness to carry the extra dead load. Extra steel beams would have been required in each of the 22 column bays across all 58 stories. The use of LWC, however, reduced the number of crane picks, streamlining the construction process.
Improved Sustainability and Reduced Emissions
At 837 feet tall, the Salesforce Tower saw significant sustainability gains through the use of LWC. The building experienced a 27% reduction in concrete volume and a 9% reduction in steel usage, which contributed to an overall 19% decrease in carbon emissions.
“Using lightweight concrete means you’re able to use thinner floor slabs, which in turn means fewer raw materials, less equipment to transport and place the concrete, and less energy consumption. It’s an exponential effect across the entire building—making it a sustainable choice all around,” explains Cavanaugh.
Strength, Durability, and Flexibility
Despite being lighter, the strength of structural lightweight concrete is comparable to traditional concrete, leading to reduced load-bearing requirements. This translates into cost savings in both materials and foundations. The use of ESC aggregate ensures the concrete’s durability while providing architects and engineers with more design flexibility and options for the structure.
“Less material and a faster schedule. That sounds like a win-win to me,” concludes Cavanaugh.
The success of Salesforce Tower Chicago highlights the value of structural lightweight concrete made with Arcosa Lightweight in modern high-rise construction. Its ability to reduce material use, speed up construction schedules, and enhance sustainability makes it the ideal choice for developers looking to build tall while minimizing their environmental footprint.
- The Issue: Reduce the embodied carbon of construction materials such as concrete and steel, while maintaining structural integrity for a high-rise building.
- What Arcosa Did: Arcosa provided lightweight aggregate for the structural lightweight concrete, which reduced the building’s overall weight and contributed to sustainability goals.
- Why Lightweight Works: Lightweight concrete enabled the use of thinner slabs and fewer materials, resulting in a 19% reduction in carbon emissions, less steel usage, and improved construction logistics.
- Result: 27% reduction in concrete volumes, 9% reduction in steel usage, and a 19% overall reduction in carbon emissions.
- Key Quote: “Less material and a faster schedule—that’s a win-win.” – Kevin Cavanaugh, Arcosa Sales and Marketing Representative
- Industry Context: Lightweight concrete offers sustainability benefits and cost savings without sacrificing strength or durability, making it a versatile option for high-rise construction.
- Lessons Learned: Lightweight concrete can be effectively pumped to great heights, even with site access limitations, while maintaining desired structural properties.
- Call to Action: Discover more about Arcosa Lightweight Aggregates and their applications in large-scale commercial construction projects.
- Project: Salesforce Tower Chicago
- Location: Chicago, Illinois
- Customer: Ready-mix partner in Chicago
- Client: Salesforce
- Project Size: 60 stories, 837 feet tall
Key Insights:
Quick Facts:
•
•
•
How Arcosa Helped:
•
•
Final Results
Key Quote
Context:
•
•
Explore Further
Additional Case Studies
Sherwin-Williams’ Global Headquarters: Lightweight Concrete for a Landmark Project
- Teaser: Sherwin-Williams is constructing its new global headquarters in Cleveland, Ohio, a development that will feature a two-story pavilion, a 36-floor office tower, and a multi-level parking garage. The project, which will redefine the Cleveland skyline, benefits from the use of Arcosa Lightweight aggregate in the structural lightweight concrete floors of the office tower.
- Article Body Text:
“Our lightweight aggregate, manufactured at our Brooks, Kentucky facility, has significantly reduced the building’s floor weight, lowering construction costs,” said Arcosa Sales Representative Jeff Hochendoner.
The expanded shale aggregate was shipped by rail from Kentucky to Arcosa’s Cleveland, OH terminal. Longtime ready-mix partner, Cuyahoga Concrete, a division of the Osborne Company, handled the transportation of the lightweight aggregate to their plant for wetting and stockpiling.
“Kurt Bell of Cuyahoga has closely collaborated with our sales and logistics teams to ensure smooth lightweight aggregate deliveries for this complex project,” noted Hochendoner. “He continues to stay on top of the project’s progress and the evolving material requirements.”
The aggregate was pre-wet and batched at Cuyahoga’s plant near the Cuyahoga River. After delivery to the job site, the lightweight concrete undergoes quality testing and is pumped by Hydracrete Pumping Company, which sends it up multiple stories for placement on the building’s metal floor decking.
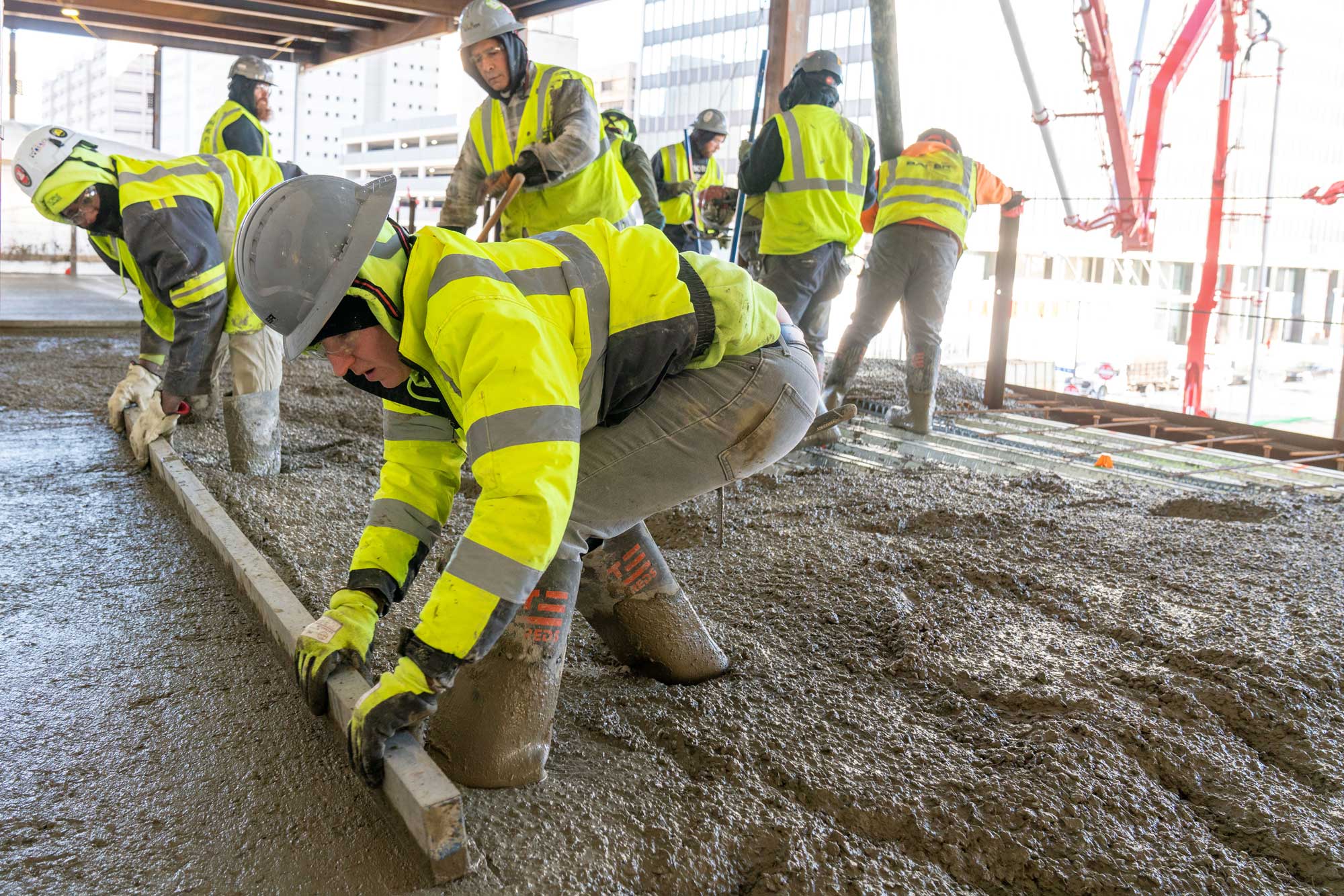
About Structural Lightweight Concrete (SLC)
Structural lightweight concrete (SLC) offers design flexibility and significant cost savings by reducing dead load, minimizing supporting steel, and allowing for smaller foundations. Arcosa’s expanded shale or clay (ESC) lightweight aggregate has a ceramic composition, ensuring an excellent bond and elastic compatibility with the cementitious matrix of the concrete.
Compared to standard concrete, lightweight concrete using ESC offers superior thermal properties, higher fire ratings, and reduced autogenous shrinkage. It improves the contact zone between the aggregate and cement, reduces micro-cracking due to better elastic compatibility, and enhances sound absorption. It is also highly suitable for pumping applications, providing logistical efficiency on complex projects.
A Major Investment in Cleveland’s Future
Sherwin-Williams chairman and CEO, John G. Morikis, described the new facility as “a next-generation workplace to serve our customers, retain and attract employees, and offer opportunities to celebrate the Sherwin-Williams brand, while acting as a catalyst for future development around our new campus.”
Cleveland Mayor Justin M. Bibb praised the decision, saying, “The city applauds Sherwin-Williams’ further investment in Cleveland and Northeast Ohio with world-class facilities designed for the workforce of the future.”
The multi-phase move-in process is expected to occur in 2025, marking a major milestone for Sherwin-Williams and the city of Cleveland.
- The Issue: Reduce construction costs while maintaining structural integrity for a large-scale office tower.
- What Arcosa Did: Arcosa provided structural lightweight aggregate for the office tower’s concrete floors, significantly reducing dead load and construction costs.
- Why Lightweight Works: The use of expanded shale aggregate reduced the overall weight of the structure, minimizing the need for additional supporting steel and foundation materials.
- Result: Lightweight aggregate allowed for cost-efficient construction of the high-rise office tower.
- Key Quote: “Our lightweight aggregate has significantly reduced the weight of the building’s floors, keeping construction costs down.” – Jeff Hochendoner, Arcosa Sales Representative
- Industry Context: Lightweight concrete offers advantages such as thermal efficiency, reduced micro-cracking, and improved fire ratings.
- Lessons Learned: Leveraging lightweight aggregate for high-rise structures can lead to significant cost savings and design flexibility.
- Call to Action: Learn more about Arcosa Lightweight Aggregates and their applications in large-scale construction.
- Project: Sherwin-Williams Global Headquarters
- Location: Cleveland, Ohio
- Customer: Cuyahoga Concrete (Ready-mix partner)
- Client: Sherwin-Williams
- Project Size: 1-million-square-foot facility, 36-floor office tower
Key Insights:
Quick Facts:
•
•
•
How Arcosa Helped:
•
•
Final Results
Key Quote
Context:
•
•
Explore Further
Additional Case Studies
Structural Lightweight Concrete Elevates Houston’s Skyline
- Teaser: Market Square Tower, a 40-story residential building, rises 502 feet over downtown Houston, Texas and features 463 luxury apartments. The impressive height of the skyscraper was made possible through the use of structural lightweight concrete, which allowed the tower to reach its maximum height despite challenging geotechnical conditions.
- Article Body Text:
Market Square opened in 2017 as the tallest residential building in downtown Houston. It remains famous for its Sky Pool—a glass-bottom pool that extends 10 feet beyond the building’s edge—offering both breathtaking and thrilling views.
Market Square Tower was designed by Jackson & Ryan Architects, with Guy Jackson, AIA, Principal Emeritus, leading the project. Jackson explains that geotechnical conditions at the site would have limited the building’s height if traditional materials had been used. “It’s a 40-story building next to a 12-story garage I did back in the 80’s and that presented some geotechnical issues with the foundations.”
“We couldn’t go as tall as we did go without using lightweight structural concrete for the frame. We’d be three or four floors shorter if we’d used conventional concrete,” he added.
By reducing the dead load, Arcosa Lightweight’s structural concrete made it possible to overcome these challenges, enabling the tower to rise to its full 40 stories.
Bill Wolfe, Marketing & Technical Manager at Arcosa Lightweight, explains that structural lightweight concrete not only solves geotechnical challenges but also offers design flexibility and substantial cost savings, including reduced dead load, improved seismic response, enhanced fire ratings, and less reinforcing steel. These combined benefits made Arcosa’s lightweight aggregate the perfect choice for Market Square Tower.
Dispelling the Myths About Pumping Lightweight Concrete
This project also dispels a common myth: that lightweight concrete can’t be pumped to great heights. “We have example after example of projects where we’ve done just that,” says Wolfe. “We’ve pumped concrete to over 50 stories in Chicago, and 60 stories in Los Angeles at the Wilshire Grand Project. These examples show that lightweight concrete can be pumped successfully to great heights.”
Wolfe emphasized that Arcosa’s lightweight concrete performs exceptionally well in high-rise applications, where both height and weight are critical factors. In addition to its pumpability, lightweight concrete provided other vital benefits for the Market Square Tower, such as improved fire resistance and reduced structural load, which allowed the building to be taller without increasing foundation stresses.
609 Main at Texas: Another Success Story
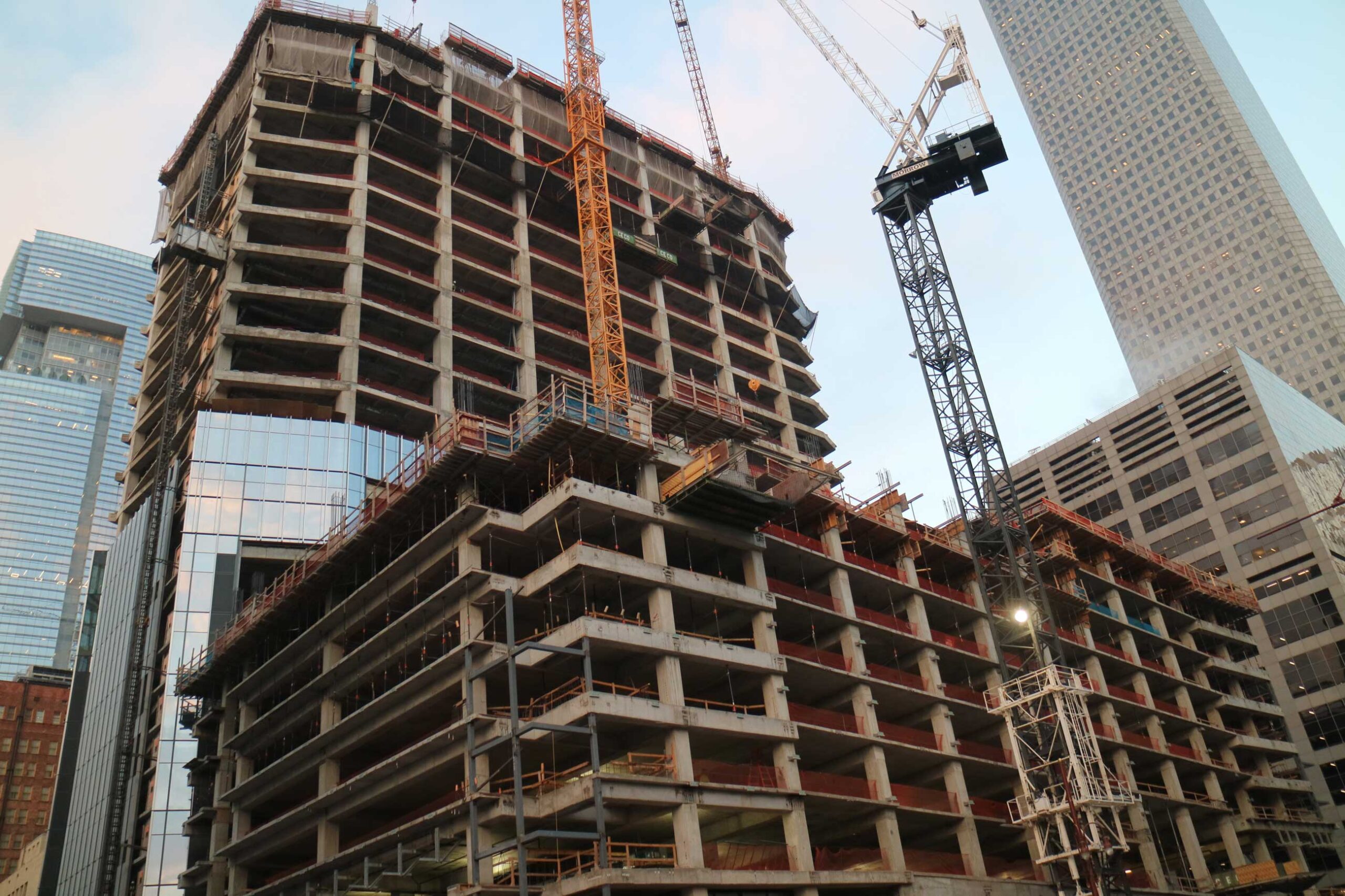
Wolfe also notes another Houston high-rise project, 609 Main at Texas, pumped lightweight concrete several stories and obtained an extra benefit from the use of the product: achieving high compressive strengths.
“What’s unique about 609 Main was the project’s specified compressive strength of the lightweight concrete,” Wolfe says. “It goes as high as 7,200 psi which dispels another myth about lightweight concrete that you can’t achieve high compressive strengths.”
As Wolfe explains, modern pumping technology, combined with a better understanding of how to use lightweight aggregate effectively, has made these advancements possible. Prewetting the lightweight aggregate is a crucial step, ensuring the material doesn’t absorb water during pumping, which helps maintain consistency and minimizes slump loss.
The Market Square Tower and other high-rise projects in Houston showcase the value of Arcosa’s lightweight aggregate in overcoming geotechnical challenges and allowing buildings to soar to new heights. With improved performance, enhanced fire resistance, and the ability to reach high compressive strengths, lightweight concrete continues to be a key material for innovative high-rise construction.
- The Issue: Overcome geotechnical limitations at the downtown Houston site to maximize the building’s height.
- What Arcosa Did: Structural lightweight concrete reduced the dead load, allowing the building to reach 40 stories despite geotechnical challenges.
- Why Lightweight Works: The lightweight concrete provided essential fire resistance, seismic response improvements, and reduced reinforcing steel requirements, making the building structurally sound.
- Result: Market Square Tower became the tallest residential building in downtown Houston upon its completion in 2017 and is famous for its Sky Pool, which offers breathtaking views.
- Key Quote: “We couldn’t go as tall as we did go without using lightweight structural concrete for the frame. We’d be three or four floors shorter if we’d used conventional concrete,” – Guy Jackson, AIA, Principal Emeritus
- Industry Context: The use of lightweight concrete dispelled myths about its pumpability and high compressive strength in tall buildings.
- Lessons Learned: Prewetting lightweight aggregate is critical to ensuring consistency and reducing slump loss when pumping to great heights.
- Call to Action: Learn how Arcosa Lightweight continues to play a crucial role in overcoming geotechnical challenges for high-rise buildings.
- Project: Market Square Tower
- Location: Houston, Texas
- Customer: CEMEX
- Client: Jackson & Ryan Architects
- Project Size: 502 feet (153 meters), 40 stories
Key Insights:
Quick Facts:
•
•
•
How Arcosa Helped:
•
•
Final Results
Key Quote
Context:
•
•