southeast
Southeastern United States a Lightweight Concrete Masonry Market
When the city of Fort Payne, Alabama embarked on an initiative to bolster its educational facilities, they chose concrete masonry for a new $19 million elementary school. The 100,000-square-foot building is constructed using lightweight, grey concrete masonry units (CMUs) produced by Kirkpatrick Concrete’s Guntersville, Alabama block division.
“Guntersville Block has been a longtime customer, buying material from our Livingston, Alabama plant,” says Bill Wolfe, Arcosa Lightweight’s Marketing & Technical Manager. “They produce only lightweight block because masons in that market want lighter units for better productivity. It helps keep concrete masonry competitive in the marketplace.”
Masons in Northeast Alabama appreciate the weight reduction, says Spencer Glassco, General Manager of Kirkpatrick’s Northern Division. “We don’t make regular weight block and haven’t for years,” Glassco says. “Most masons prefer our lightweight block, which is 8x8x16 and weighs about 28 pounds compared to 30 pounds. You’d think two pounds wouldn’t make much difference, but if you lift several hundred a day, you know it wears on you.”
Glassco adds that while some of the block used for the school were custom-designed CMUs, most were their traditional 8-inch lightweight units. “Designers specified a custom block for a safe room, and we supplied a special 12-inch block for that application,” Glassco explains. “It required a slightly different mix design with more cement and variations in aggregate to achieve the exact strength they needed.”
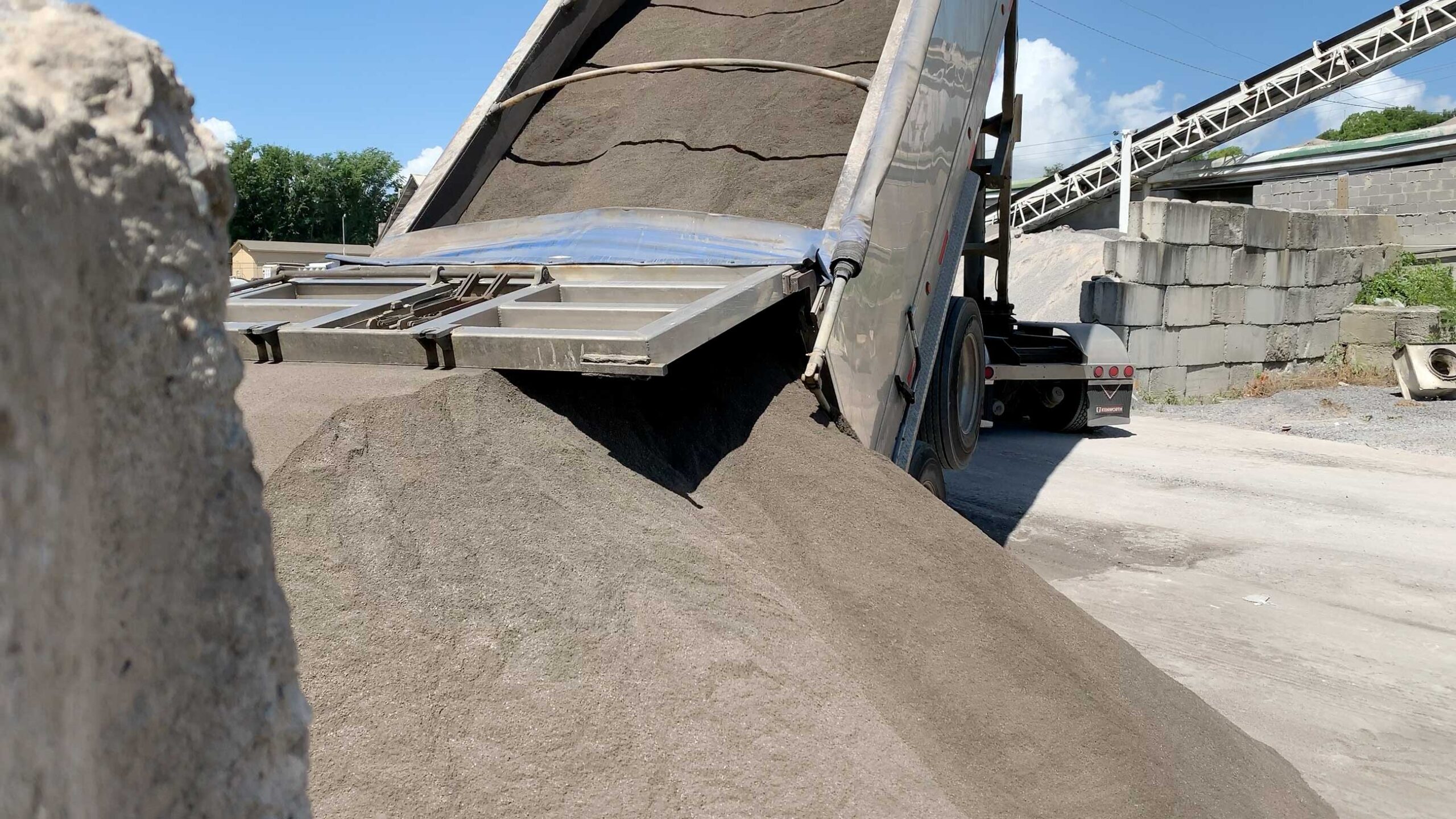
Better for Producers
The production of lightweight units is easier on employees and reduces wear on the manufacturer’s machinery, molds, and equipment. It also lowers transportation costs. “Trucks can haul more blocks when they’re lightweight, which reduces delivery costs,” Wolfe says. “It also reduces congestion at the project site because fewer truckloads are needed.”
Guntersville Block receives up to six shipments of lightweight aggregate per week, which they store alongside other aggregates and sands. “The customer receives the material just like their normal-weight materials,” Wolfe notes. “They handle the pre-wetting in the mixing process. They batch the lightweight aggregate with some of the mix water to get a pre-wet cycle, then proceed with their normal production process.”
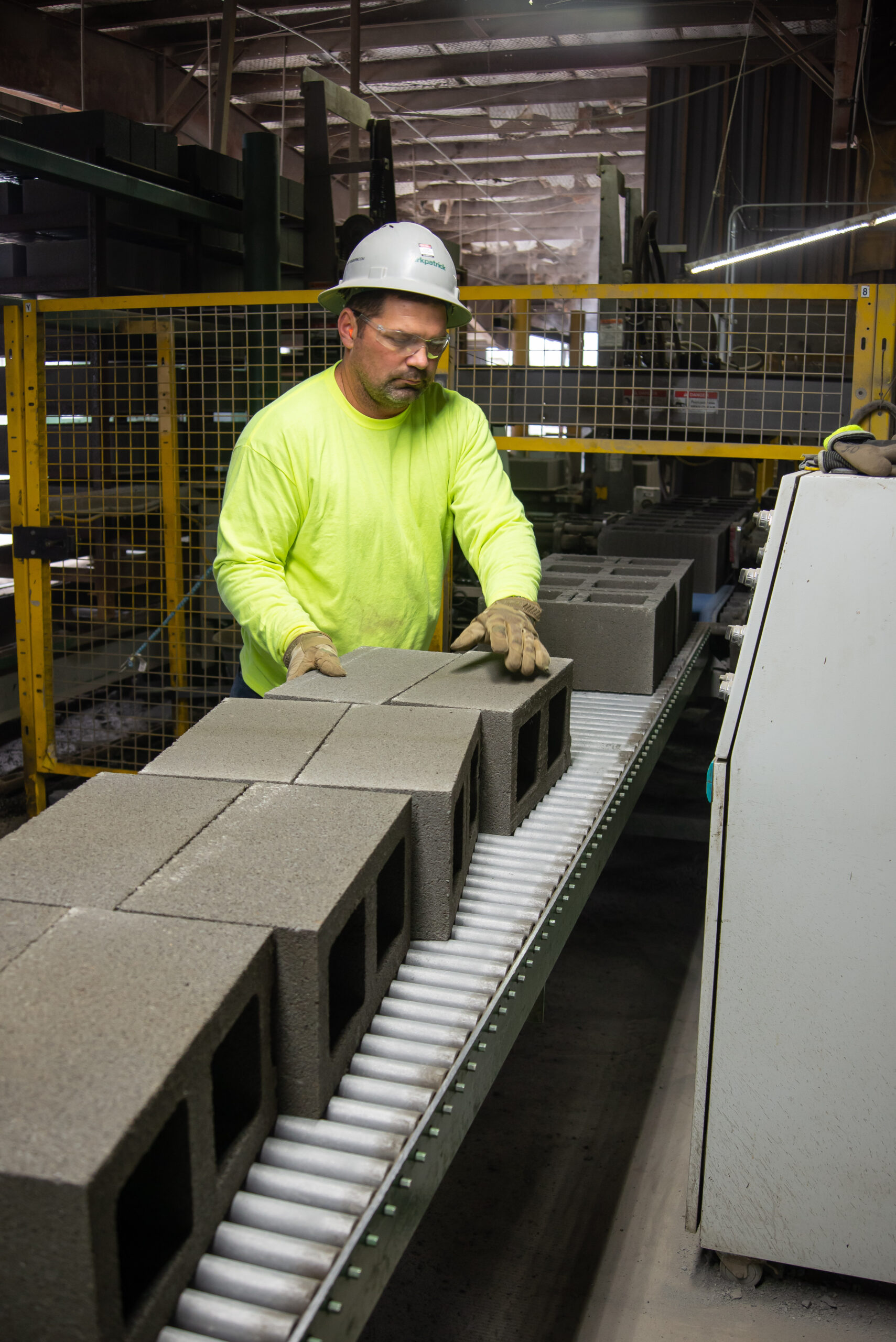
Concrete masonry also offers design flexibility, non-combustibility, and durability, making it a perfect choice for school projects. “A lot of times, you need a fire-rated corridor,” Wolfe says. “Concrete masonry won’t burn, and it’s easy to demonstrate its fire rating based on current building codes. It’s also very durable. It’s not easy to damage a concrete masonry wall like you can with other wall surfaces.”
A Sense of Pride
“Anytime you can help a community with a project like this that’s going to affect their children for years to come, it’s something we take pride in,” says Spencer Glassco. “We do the very best we can to service the project and make it work well for everyone.”