Hydrolite
Cal Poly Center a Landmark of Sustainability and Innovation
- Teaser:The Warren J. Baker Center for Science and Mathematics, located at California Polytechnic State University (Cal Poly), San Luis Obispo, is a testament to modern design, sustainability, and educational innovation. Completed in 2013, the six-story, 192,000-square-foot facility serves as a hub for students across the campus, housing classrooms, laboratories, research institutes, administrative offices, and dedicated spaces for studying.
- Article Body Text:
In recognition of its architectural and environmental excellence, the Center for the Built Environment recognized the Baker Center as an Award Winner in 2017.
Sustainable Design and LEED-Gold Certification
The LEED-Gold certified Baker Center demonstrates numerous sustainable features, designed with environmental respect and flexibility in mind. The building replaced an outdated 1950s science facility and became the largest structure on the Cal Poly campus. Funded through bonds and private donations, the $119-million project was designed to be energy-efficient, earthquake-resistant, and fire-code compliant, while also reducing environmental impact.
Arcosa Lightweight’s Contribution: Hydrolite® Aggregate
A key factor in the Baker Center’s construction was the use of Arcosa Lightweight’s Hydrolite® expanded clay aggregate, manufactured in Frazier Park, California. Hydrolite was selected for its lightweight properties, durability, and environmental benefits. The expanded clay material, with their lightweight ceramic shell and honeycomb core, provided the necessary strength while also helping to reduce the building’s structural load, which was particularly important due to the weak soil deposits on site.
The project required 10,000 cubic yards of concrete, and Hanson Ready Mix, the concrete supplier, chose Arcosa’s Frazier Park aggregate to meet the stringent California fire, seismic, and energy efficiency codes. Hydrolite’s permeability and thermal resistance also contributed to the building’s sustainability efforts, further supporting the LEED certification.
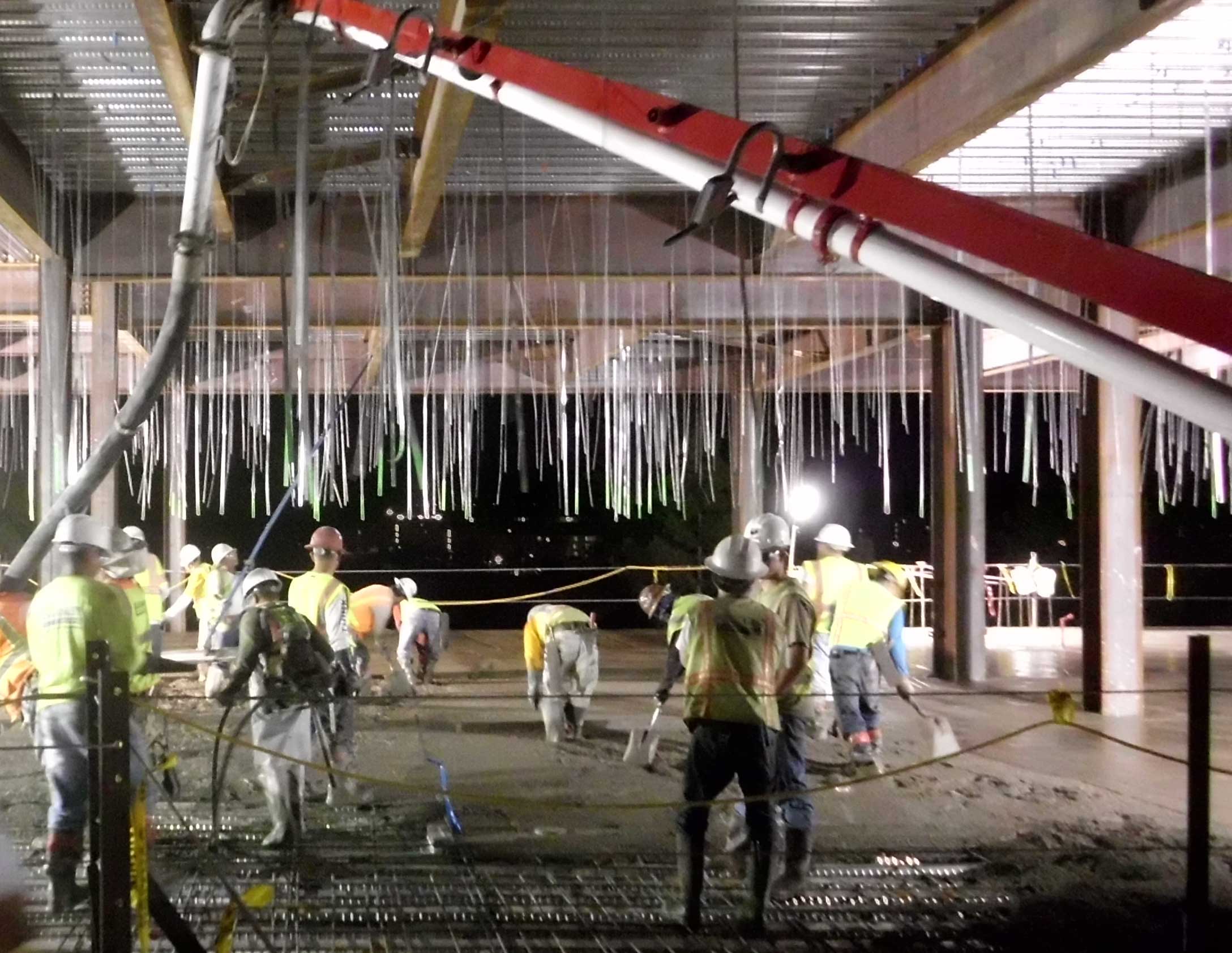
Construction and Performance
The lightweight expanded clay material used in the Warren J. Baker Center’s construction offer several critical benefits:
- Strength and durability: Hydrolite’s lightweight nature made it ideal for construction on weak soil, reducing the overall load on the structure.
- Thermal resistance: The aggregate provided excellent insulation when used under flooring, helping the building meet energy efficiency standards.
- Sustainability: As an environmentally friendly material made from natural clay, Hydrolite was a perfect fit for the project’s sustainability goals.
Produced by firing natural clay at 1100-1200°C in a rotating kiln, the rounded pellets of 0-32mm in size have a dry bulk density of approximately 350 kg/m³, making them ideal for lightweight construction while still maintaining strength and durability.
Environmental Impact and Sustainability
The Baker Center’s design and construction focused heavily on sustainability. The use of Arcosa’s Hydrolite® aggregate was a key factor in achieving this goal. Hydrolite is primarily composed of naturally occurring clay, making it environmentally friendly, durable, and resistant to chemical attacks, rot, or frost. The aggregate’s long life span also ensures minimal maintenance and continued performance in a wide range of applications, including lightweight concrete blocks and water filtration systems.
The Warren J. Baker Center for Science and Mathematics stands as a symbol of sustainability and innovation at Cal Poly San Luis Obispo. By utilizing Arcosa Lightweight’s Hydrolite® expanded clay aggregate, the project successfully met stringent environmental, fire, and seismic requirements while reducing the building’s overall load and supporting its LEED-Gold certification. Recognized by the Center for the Built Environment as an Award Winner in 2017, the Baker Center is a model for future sustainable campus developments.
- The Issue: Cal Poly needed a new, sustainable facility to replace an outdated science building from the 1950s. The new Warren J. Baker Center required an efficient, lightweight concrete solution to comply with stringent California fire, seismic, and energy efficiency codes, while maintaining structural integrity over weak soil deposits.
- Why Lightweight Works: Hydrolite®’s lightweight and permeable properties made it ideal for constructing over weak soil. Its thermal resistance contributed to the building’s energy efficiency, while its durability supported the building’s LEED-Gold certification.
- Result: The building met all project specifications, including energy efficiency, fire resistance, and seismic codes. The use of Hydrolite® helped the building achieve LEED-Gold certification, and the project was recognized as a 2017 Award Winner by the Center for the Built Environment.
- Key Quote: “The lightweight expanded clay aggregate provided the necessary strength while reducing the structural load, a key factor in the building’s sustainability and long-term performance.”
- Industry Context: The lightweight nature of Hydrolite® not only reduced the structural load but also contributed to long-term energy savings through its thermal resistance. Its environmentally friendly properties made it a perfect fit for a sustainability-focused project.
- Lessons Learned: Lightweight aggregates like Hydrolite® offer dual benefits of reducing structural load and supporting environmental sustainability, making them ideal for large-scale projects with complex demands.
- Call to Action: Consider using Arcosa Lightweight’s Hydrolite® aggregate for future projects requiring reduced structural load, energy efficiency, and compliance with stringent building codes.
- Project: Warren J. Baker Center for Science and Mathematics
- Location: San Luis Obispo, California
- Customer: Hanson Aggregates
- Client: California Polytechnic State University (Cal Poly)
- Project Size: 192,000 square feet, six-story building
Quick Facts:
•
•
•
Key Insights:
Quick Facts:
•
•
•
How Arcosa Helped:
•
•
Final Results
Key Quote
Context:
•
•
Explore Further
Additional Case Studies
HydroLite Lightweight Aggregate Plays Key Role in Record-Breaking Structure
- Teaser: Wilshire Grand Center, which stands at an impressive 1,100 feet, is recognized as one of the tallest buildings in the western United States. The project’s engineers needed to significantly reduce the building’s overall weight to achieve this height, which is why they opted for structural lightweight concrete.
- Article Body Text:
With over 15,000 cubic yards of lightweight aggregate used in the concrete mix—10,000 cubic yards of which incorporated Arcosa’s HydroLite® vacuum saturated lightweight aggregate—the project achieved not only the necessary height but also critical fire resistance and improved pumpability, allowing for more efficient construction.
The structural design of the building incorporates multiple lightweight concrete slabs, with lightweight concrete poured on metal decking to form the floors and core, spanning over 1.2 million square feet across the entire tower.
Pumping No Issue for Lightweight Concrete
The ability to pump lightweight concrete all the way up to project’s soaring height was key to the successful completion of the building, which now features 900 hotel rooms, a 70th-floor sky lobby, and 445,000 square feet of office and retail space.
According to Clint Chapman, Western Region Marketing & Technical Manager for Arcosa Lightweight, the lightweight concrete used for the project was pumped at heights of 1,300 feet, with 1,100 feet of that being vertical pumping.
“The fact that our HydroLite is presoaked made pumping it up to the building’s very high floors more efficient compared to traditional materials,” explains Chapman.
HydroLite® is a vacuum saturated lightweight aggregate produced by Arcosa Lightweight. This process allows the aggregate to absorb water, providing improved pumpability, reduced slump loss, and better consistency during placement. The vacuum saturation also enables the aggregate to maintain internal moisture, contributing to better curing and minimized cracking in the concrete.
Chapman also notes that the LWC used for the project also helped achieve the project’s strict fire rating requirements without needing additional fireproofing layers.
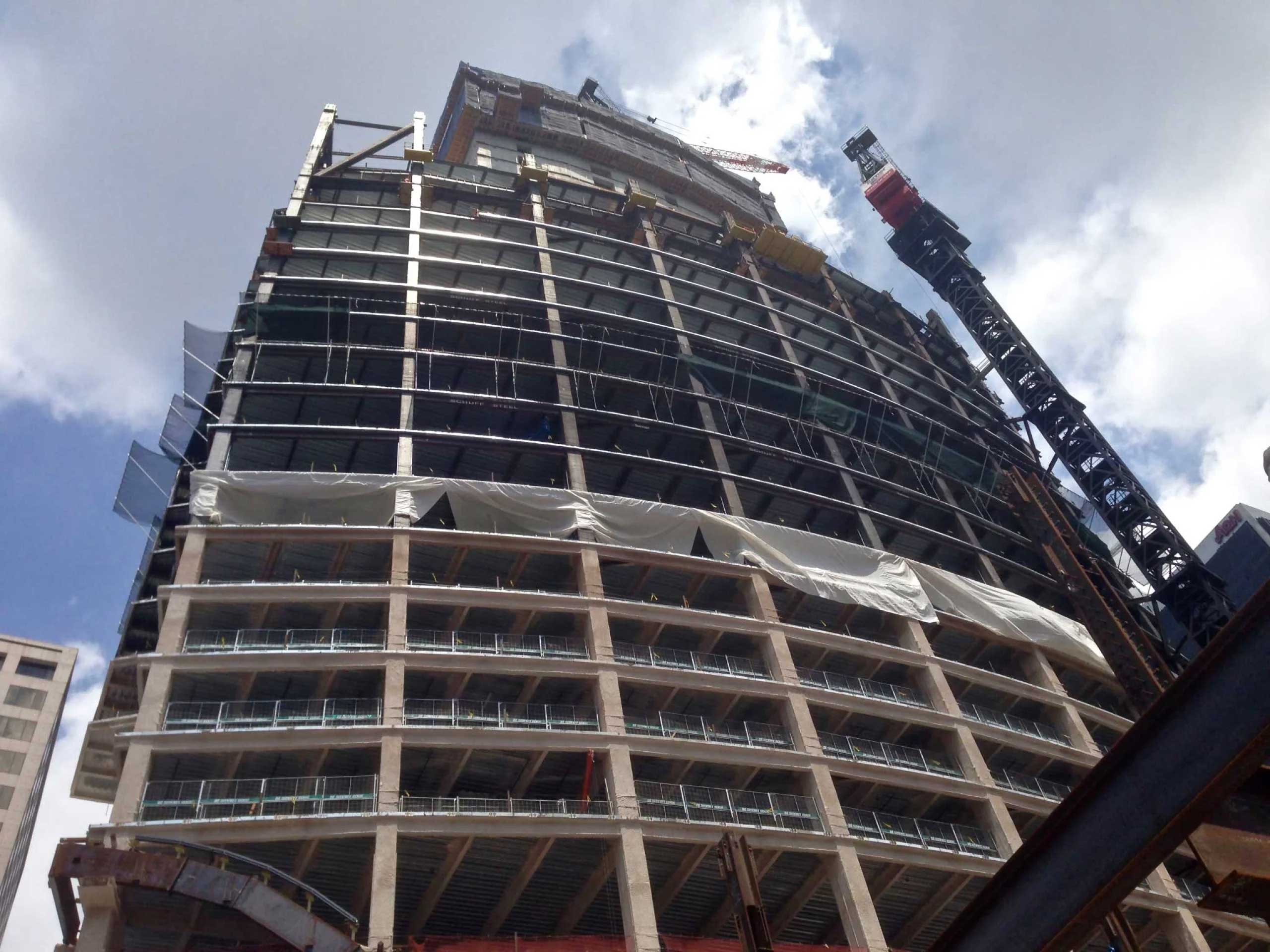
Placement Team
Turner Construction, the general contractor, led the build, with Conco Cement Company handling the concrete pumping, and Catalina Pacific Concrete, a division of CalPortland, providing the ready-mix. Arcosa Lightweight supplied the lightweight aggregate for the concrete that was used on the metal decking surrounding the building’s core and elevator towers.
Arcosa’s structural lightweight aggregate was manufactured at its Frazier Park, California plant, with the ready-mix supplier replacing standard weight granite with the lighter HydroLite aggregate.
“The HydroLite reduces the concrete’s unit weight from 147 pounds per cubic foot to just 115 pounds per cubic foot,” Chaman notes.
Exceeding Expectations Through Teamwork
The Wilshire Grand Center project is a prime example of exceptional collaboration among the general contractor, the ready-mix concrete supplier, the concrete placement subcontractor, the pumping subcontractor, and the lightweight aggregate supplier.
“This project showcases the value of a cohesive team,” says Chapman. “Everyone worked together seamlessly to ensure the success of this monumental build.”
- The Issue: Reducing the building’s overall weight to achieve the height of the tallest structure in the western U.S., while ensuring that the lightweight concrete could be efficiently pumped to extreme heights during construction.
- What Arcosa Did: Supplied HydroLite® Lightweight Aggregate to produce over 10,000 cubic yards of lightweight concrete.
- Why Lightweight Works: Lightweight concrete helped reduce the building’s overall weight, met fire rating requirements without additional fireproofing, and allowed for efficient pumping to heights of over 1,100 feet.
- Result: The use of structural lightweight concrete enabled the successful construction of the tallest building in the western United States, reducing material weight while meeting key fire safety and engineering requirements.
- Key Quote: “The fact that our HydroLite is presoaked made pumping it up to the building’s very high floors more efficient compared to traditional materials.” — Clint Chapman, Western Region Marketing & Technical Manager for Arcosa Lightweight
- Industry Context: Structural and fire safety requirements needed to be balanced with the demand for efficient construction.
- Lessons Learned: Lightweight concrete not only meets engineering needs but also improves project logistics by facilitating easier material handling and placement at extreme heights.
- Call to Action: Learn more about the use of HydroLite® Lightweight Aggregate in high-rise construction at Arcosa Lightweight.
- Project: Wilshire Grand Center
- Location: Los Angeles, CA
- Customer: Catalina Pacific Concrete
- Client: Hanjin Group
- Project Size: 15,000+ cubic yards of structural lightweight concrete on metal deck
Key Insights:
Quick Facts:
•
•
•
How Arcosa Helped:
•
•
Final Results
Key Quote
Context:
•
•
Explore Further
Additional Case Studies
Shasta Arch Bridge Project: Using Arcosa Lightweight Aggregate for High-Performance Concrete Solutions
- Teaser:The newly completed Shasta Arch Bridge, with its striking design and sweeping arches, serves as a crucial route for travelers in Northern California. Built with Super High Performance Concrete containing Arcosa’s lightweight aggregate, the bridge’s reduced structural load enhances both its durability and aesthetic appeal, ensuring long-term reliability for all who traverse this remote and scenic area.
- Article Body Text:
Ric Maggenti, who was a Senior Materials & Research Engineer for the California Department of Transportation (Caltrans) before his retirement, explained, “Lowering demand consisted of changing the structure concrete (stem, bent caps, and deck) from a normal weight, normal strength concrete to a high strength, lightweight concrete.” Maggenti emphasized that lightweight concrete has been successfully used in numerous bridges worldwide, citing the Bay Bridge, which has shown no observable deck distress after more than 80 years of service, and the Napa River Bridge, which continues to perform well even after the 2014 Napa earthquake.
Why High-Performance, High-Strength Lightweight Concrete?
Originally, the bridge was designed using normal weight concrete with a specified compressive strength of 4,000 psi. Maggenti explained, “The increased design strength [for the lightweight concrete] eliminated any need to significantly adjust for rebar developmental lengths, or accounting for lower shear, creep, modulus of elasticity, and modulus of rupture values used in the original design.” By increasing the compressive strength to 6,000 psi, Maggenti noted, “these other property values converge to those of a lower strength normal weight concrete,” addressing concerns such as Alkali Silica Reaction (ASR), Delayed Ettringite Formation (DEF), deck permeability, and cracking.
“The increased design strength eliminated any need to significantly adjust for rebar developmental lengths, or accounting for lower shear, creep, modulus of elasticity, and modulus of rupture values used in the original design.”
Arcosa Lightweight Aggregate for the Shasta Arch Bridge Project
Arcosa’s Hydrolite® expanded clay aggregate, produced in Frazier Park, California, was selected for the project due to its ability to meet the strict performance requirements. Pre-conditioned at the Frazier Park plant, the aggregate arrived at the ready-mix concrete plant in a near-saturated condition, simplifying the production of pumpable lightweight concrete.
Pumping Lightweight Concrete
Maggenti directly addressed concerns about the pumpability of lightweight concrete, stating, “[Caltrans] was not at all subjectively distracted by a belief that lightweight concrete is inherently difficult to pump.” He explained that the difficulty in pumping lightweight concrete arises when the aggregate is not saturated, but that Arcosa’s pre-saturated aggregate eliminated this issue. Maggenti continued, “A 125 pcf concrete imparts by its mass a pressure of 0.87 psi resisting its vertical motion inside the pipe while a 150 pcf concrete imparts by its mass a pressure of 1.04 psi per cubic foot of concrete. That is a 20% increase in force to move normal weight concrete. So why would a lightweight concrete be more difficult to pump than a normal weight concrete?”
Ultimately, the lightweight concrete mix exceeded expectations, with pumping rates occasionally reaching over 100 cubic yards per hour (cy/hr), far surpassing the original target of 60 cy/hr. “The mix pumped better than anybody expected, and no additional pumping agent chemical admixture was used,” Maggenti added.
Mass Concrete Issues
There were concerns about exceeding the maximum allowable temperature in the mass concrete within the diaphragms and bent caps due to the high cementitious content of 900 pounds per cubic yard. Two cooling pipes were installed longitudinally through the bent caps to control the concrete temperature, which had a target of 160°F. While temperatures exceeded this at times due to extreme ambient air temperatures and the difficulty of controlling water temperature in the cooling pipes, the concrete did not overheat.
“Initially it was believed the lightweight aggregate would exacerbate mass concrete issues. However, this was not the case for the Arcosa aggregate. The difference was the amount of water in the lightweight aggregate.” — Ric Maggenti
Maggenti explained that Arcosa’s aggregate, with an absorption rate of over 24%, requires more energy to increase its temperature than traditional mineral aggregates, which helped prevent thermal issues caused by the high cementitious content.
Conclusion
For this project, all of the requirements for a lightweight, air-entrained concrete mix that was pumpable, durable, and high-performing were met. All concrete strengths exceeded the specified requirements for high-strength concrete, and the 120 pcf equilibrium density target was achieved. The results of air content field tests on the plastic concrete were confirmed by petrographic examination of the hardened concrete.
“The requirement for a lighter structure was met by using Arcosa Lightweight Aggregate, producing concrete with a maximum equilibrium density of 120 pcf,” Maggenti stated. The pre-conditioned lightweight aggregate helped lower pump line pressures, allowing the concrete to be pumped efficiently, sometimes at rates exceeding 100 cy/hr. The consistency of the concrete remained stable throughout transport, even with extended durations of up to 1½ hours.
With these unique attributes, it’s no surprise Caltrans labeled the resulting material “Super High Performance Concrete” and anticipates it to be a model for future challenging situations.
- The Issue: Caltrans needed to reduce structural demand and dead loads after unexpected conditions during the Shasta Arch Bridge construction. The original design with normal weight concrete had to be revised to lightweight concrete to lighten the structure without sacrificing durability.
- What Arcosa Did: Arcosa provided Hydrolite® expanded clay lightweight aggregate, pre-conditioned for consistent moisture content and optimal pumpability, which enabled Caltrans to achieve the necessary strength and reduced load requirements for the bridge.
- Why Lightweight Works: The use of lightweight concrete decreased the overall structural load, allowing the bridge to perform better under the stress of daily use while maintaining the aesthetic and structural integrity. The lightweight aggregate also helped manage pumpability and temperature in mass concrete sections.
- Result: The lightweight concrete met all project specifications, including compressive strength of 6,000 psi and equilibrium density of 120 pcf. Pumping rates exceeded expectations, and Arcosa’s aggregate contributed to the long-term reliability of the bridge.
- Key Quote: “The mix pumped better than anybody expected, and no additional pumping agent chemical admixture was used.” — Ric Maggenti, retired Senior Materials & Research Engineer, Caltrans
- Industry Context: Pre-saturation of the lightweight aggregate was critical for maintaining pumpability and reducing thermal issues in the mass concrete.
- Lessons Learned: Collaborative adjustments in material proportions and pre-conditioning can resolve common challenges in lightweight concrete projects, such as pumpability and temperature control.
- Call to Action: Consider using Arcosa Lightweight Aggregate for future projects requiring reduced structural load, high strength, and enhanced performance in challenging environments.
- Project: Shasta Arch Bridge Project
- Location: Northern California
- Client: California Department of Transportation (Caltrans)
- Client: Salesforce
- Project Size: 366 ft and 400 ft arch ribs, spanning a steep hillside
- Related Link 1: Visit Website
Key Insights:
Quick Facts:
•
•
•
How Arcosa Helped:
•
•
Final Results
Key Quote
Context:
•
•
Explore Further
Structural Lightweight Concrete
Article: Shasta Bridge Improved by Pumping a Lightweight Concrete Solution
Additional Case Studies
Sutter Health Mills-Peninsula Medical Center: Seismic Safety and Sustainable Concrete Solutions
- Teaser:
California’s Sutter Health Mills-Peninsula Medical Center (MPMC), completed in 2011, is a state-of-the-art 241-bed, not-for-profit general medical and surgical facility located in Burlingame, California. The six-story, 450,000-square-foot facility offers a wide range of services, including emergency care, ICU, inpatient, and outpatient services. Designed to meet the community’s growing healthcare needs, MPMC also had to comply with California’s strict seismic and safety regulations. - Article Body Text:
In a June 2012 interview with Health Facilities Management magazine, Sutter Health’s facility and property services representative noted, “The medical center is designed to withstand an 8.5 magnitude earthquake centered in Burlingame.” They continued, “Hopefully, we won’t get the seismic occurrence that would do extreme damage to our neighborhood, but if we do, I think we’re in a situation where we will continue to operate and provide the medical care that the community will need after a seismic occurrence like that.”
Lightweight Concrete Specified
Central Concrete, a subsidiary of Vulcan Materials Company, is a major supplier of both lightweight and standard weight concrete in the region. Central Concrete delivered 5,500 cubic yards of lightweight concrete for the project. Arcosa Lightweight’s Boulder, Colorado plant supplied nearly 30 rail cars filled with vacuum-saturated structural lightweight aggregate, which were transported to the site to meet the project’s needs.
Arcosa’s Hydrolite®, a vacuum saturation process, allows for immediate saturation of the lightweight aggregate, minimizing the need for “maintenance moisture” at the customer’s batch plant.
This process enabled “ship it – use it” inventory control, significantly enhancing the pumpability of the lightweight concrete while providing improved inventory management capabilities to the ready-mix producers.
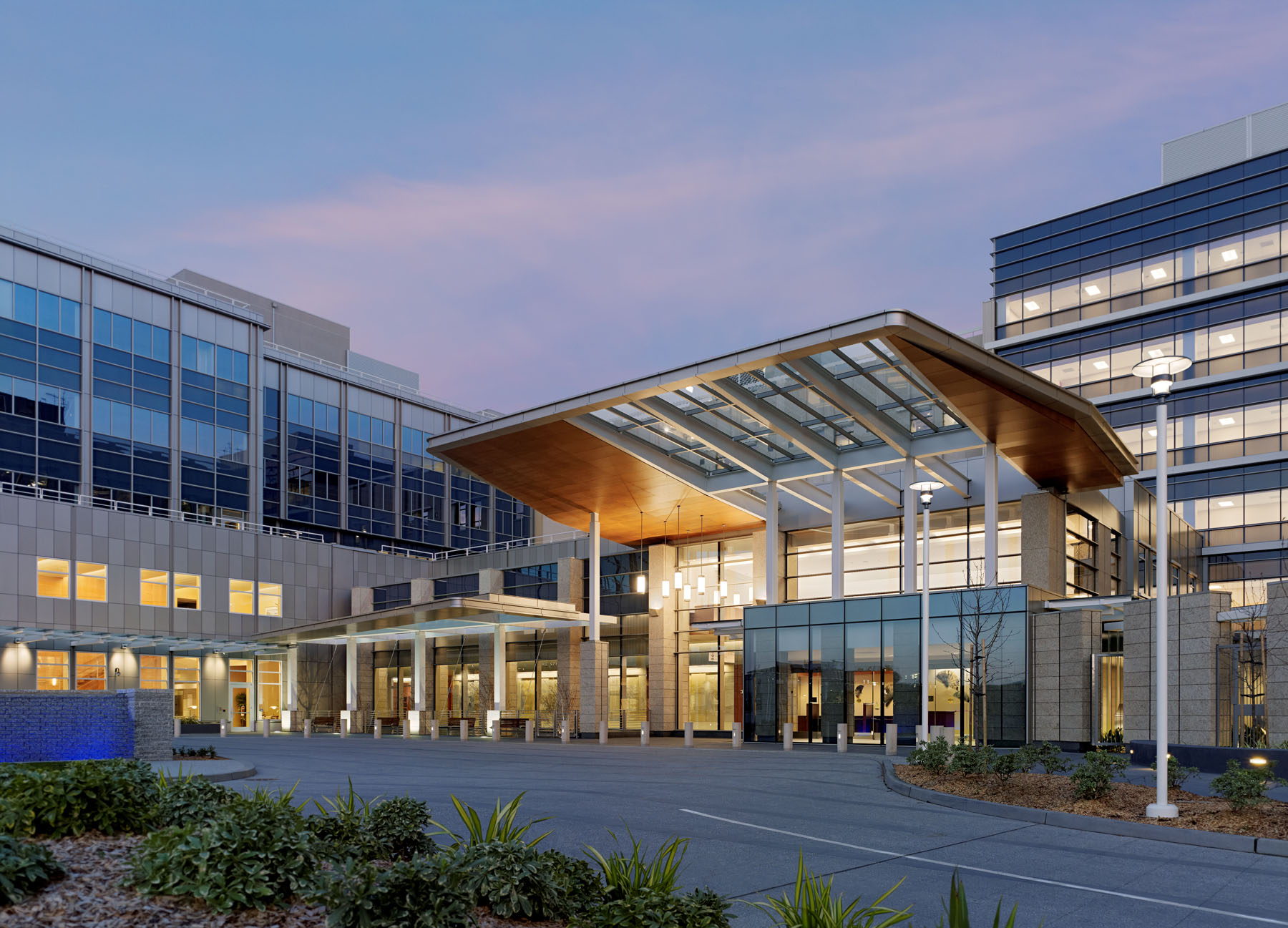
Dramatic Gateway
The Mills-Peninsula Medical Center was designed by Anshen & Allen, a San Francisco architectural firm acquired by Stantec Inc. in 2010.
The facility provides a dramatic gateway to the city of Burlingame, combining aesthetic appeal with essential healthcare functions. The structural and seismic engineering for the project was overseen by Rutherford + Chekene (R+C), one of California’s leading structural and geotechnical engineering firms. Engineers Dominic Campi, Thomas Lauck, and William Holmes ensured that the facility adhered to the fire and seismic safety standards set by The Office of Statewide Health Planning and Development (OSHPD).
Today, Mills-Peninsula Medical Center operates as a not-for-profit organization affiliated with Sutter Health, delivering compassionate and innovative healthcare to the residents of San Mateo County.
- The Issue: Sutter Health required a state-of-the-art facility that complied with California’s stringent seismic safety regulations. The new Mills-Peninsula Medical Center needed to be constructed using a material that could meet seismic standards, minimize structural load, and enhance pumpability for easy construction.
- What Arcosa Did: Arcosa supplied Hydrolite®, a vacuum-saturated lightweight aggregate from its Boulder, Colorado plant. This allowed the concrete mix to meet both strength and seismic safety standards, while minimizing structural load and improving ease of use.
- Why Lightweight Works: Hydrolite®’s vacuum saturation process minimized the need for additional moisture, allowing for efficient “ship it – use it” inventory control. This enhanced the pumpability of the lightweight concrete and supported the high demands of a seismically safe structure.
- Result: The facility was built using 5,500 cubic yards of lightweight concrete, with a maximum fresh density of 125 pounds per cubic foot and a dry density of 116 pounds per cubic foot, easily meeting the engineer’s specifications.
- Key Quote: “This process enabled ‘ship it – use it’ inventory control, significantly enhancing the pumpability of the lightweight concrete while providing improved inventory management capabilities to the ready-mix producers.”
- Industry Context: Seismic safety was a key concern for the project. The use of Arcosa’s Hydrolite® lightweight aggregate ensured compliance with California’s strict seismic and fire safety standards.
- Lessons Learned: Pre-saturation and the ease of handling lightweight aggregate improve both construction efficiency and long-term structural performance, particularly in regions requiring seismic resilience.
- Call to Action: Arcosa Lightweight offers tailored solutions for large-scale infrastructure and healthcare projects, ensuring compliance with seismic, fire, and safety standards while reducing overall structural load.
- Project: Sutter Health Mills-Peninsula Medical Center
- Location: Burlingame, California
- Customer: Central Concrete
- Client: Sutter Health
- Project Size: 450,000 square feet
Key Insights:
Quick Facts:
•
•
•
How Arcosa Helped:
•
•
Final Results
Key Quote
Context:
•
•