Environmental Impacts of Lightweight Aggregate
Environmental Impacts of Lightweight Aggregate
This information has shown improvement over recent years due to awareness, process improvements, and improved efficiencies. While designers and green rating systems tend only to evaluate a product cradle-to-gate, numerous products on the market today need a look beyond the manufacturing facility to get the actual impact on the environment.
Life Cycle Inventory
ESCSI completed a production survey of 10 member plants in 2023. All producer members of the ESCSI participated in the study and presented data on expanded shale, clay, and slate (ESCS) lightweight aggregate production. The survey followed the previously used process, lifecycle inventory, and production survey reports to evaluate environmental impacts. The outcomes comply with the ESCS Product Category Rules (PCR) report and cover the cradle-to-gate portion of these documents (Table 1). An in-progress lifecycle assessment (LCA) and the following industry-average environmental product declaration (EPD) will report cradle-to-gate and beyond footprints for ESCS lightweight aggregates and applications.
Production | A1 | A2 | A3 |
---|---|---|---|
Cradle to Gate | Raw Material Supply | Transport | Manufacturing |
The 2023 production survey represents 2,880,000 tonnes (3,175,000 tons) or nearly 3,614,000 m3 (4,726,000 yd3) processed materials with an average bulk moist density of 800 kg/m3 (50 lb./ft3) at a 7% moisture content. This equates to an average dry bulk density of 750 kg/m3 (47 lb./ft3). These values are comparable to previously submitted data. However, energy and emissions indicate significant declines due to continuous plant improvements and enhanced process technology efficiencies.
Embodied Energy | 1.47 GJ/m3 (1.06 MMBtu/yd3) |
Emissions (CO2) | 111 kg/m3 (187 lb./yd3) |
Waste Disposed | 4.15 kg/m3 (6.99 lb./yd3) |
Net Freshwater | 400 liter/m3 (80.8 gal/yd3) |
These values represent the average of the ESCSI member companies’ manufacturing facilities to produce one cubic meter of lightweight aggregate. These values represent only the production phase of the material. The complete PCR that outlines impacts for the construction, use, and end-of-life stages can be downloaded at no cost from the Underwriters Laboratory Website.
Comparative Study on Structural Lightweight Concrete
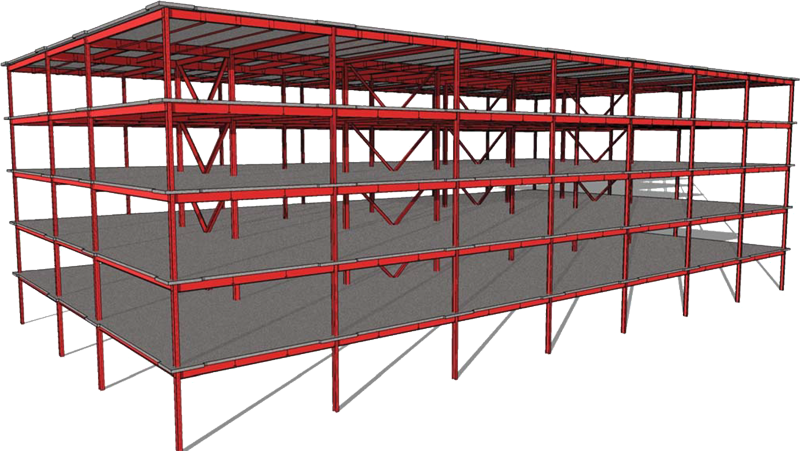
The reduction in concrete densities helps to reduce the use of other energy-intensive construction materials. These benefits were demonstrated in a study conducted by Walter P. Moore that compared the embodied energy in the structural system of a steel-framed building with lightweight concrete (LWC) floor slabs on composite steel deck to the same system using normal weight concrete (NWC). Four structural systems were compared; all had the same floor acceleration, fire rating, and live, wind, and seismic loads.
This study only included the embodied energy of the building’s structural materials. It excluded any transportation energy impacts or the embodied energy in the building envelope (or other systems).
A material inventory was created after performing the structural design for each building scenario. For the concrete mixture proportions, Walter P. Moore used aggregated data from historical concrete mixture proportions used in its practice across the U.S. Energy intensities of the structural materials were taken from the Inventory of Carbon & Energy, version 2, by Hammond and Jones, which reports embodied energy of materials from a cradle-to-gate basis.
The results showed that one of the LWC scenarios had the lowest total embodied energy at 10,520 MMBTU. In contrast, the NWC scenario had a total embodied energy of 10,660 MMBTU for the structure. The study found that the energy required to produce LWA was offset by the following:
- the reduced dead load of the scenario
- the reduced concrete volume due to improved fire performance
- thinner steel decks for a given beam spacing due to the reduced weight of the concrete floor
Lightweight aggregate is an environmentally friendly product with unique features that has been successfully used for well over two millennia. Rotary kiln-produced ESCS has been widely used for the past hundred years in a multitude of applications that contribute to the sustainability of the site and structure, long before the current green movement came to the forefront. It is important to consider all phases of a project’s life and evaluate the impacts on the environment and other materials required to construct and operate a building.