Bridge Decks
Internal Curing Concrete Proves Its Value in Reducing Cracking and Enhancing Durability for Louisiana Bridge Projects
- Teaser:From an engineering perspective, Mitch Wyble, P.E., City Engineer at Lafayette Consolidated Government, really likes what he sees when he discusses the value of internally cured concrete (ICC), a concrete mixture where a portion of the fine aggregate is replaced with similarly sized prewetted lightweight aggregate (LWA). Wyble first encountered ICC years ago while serving on the Technical Committee of the Concrete and Aggregates Association of Louisiana (CAAL).
- Article Body Text:
As a past CAAL Technical Committee member, Wyble also knew that the Louisiana Department of Transportation & Development (LADOTD) was investigating ICC’s potential for state projects.
“I suggested we use internal curing on this particular bridge,” says Wyble, “knowing that it wouldn’t cost us any more than what the bid was for the typical cast-in-place concrete option.”
For the project, the Louisiana Transportation Research Center (LTRC) handled the mix designs, testing, and evaluation.
Arcosa provided the lightweight aggregate for the ICC, which in turn was used to build two of the five bridge deck spans, one guardrail wall, and one approach slab. The approach slab is 10’ X 30’ while each bridge deck span is 20’ X 30’ and 16 inches thick, according to Bill Wolfe, Marketing & Technical Manager of Arcosa Lightweight.
Project’s Goal
“The goal was to demonstrate the ICC’s value and monitor its performance over time,” says Wolfe, who adds that project completion was made easier due to the use of ICC.”
“Evidently, the concrete sand being used was less than ideal in terms of grading. The replacement of a portion of the sand with lightweight sand that was a little coarser in gradation had the effect of improving the performance of the combined fine aggregates, allowing the concrete to be finished more easily and with less hand trowel work.”
Expert Insight
Tyson Rupnow, Ph.D., P.E., Associate Director of Research at LTRC says the Congress Street Bridge project was based on LADOTD’s goal of reducing the cracking severity on its bridge decks.
“ICC helps reduce cracking, thus allowing us to increase the service life of our deck structures and reduce overall maintenance costs,” says Rupnow.
Calling ICC a “great tool for bridge engineers and designers,” Rupnow adds that if the process helps extend bridge service life and strength, then it should be looked at more closely for upcoming projects. That’s already happening, he says, noting that the successful West Congress Street project has already prompted Lafayette Consolidated Government to build another, 150-foot-long bridge plus barrier rails out of ICC.
Test Results
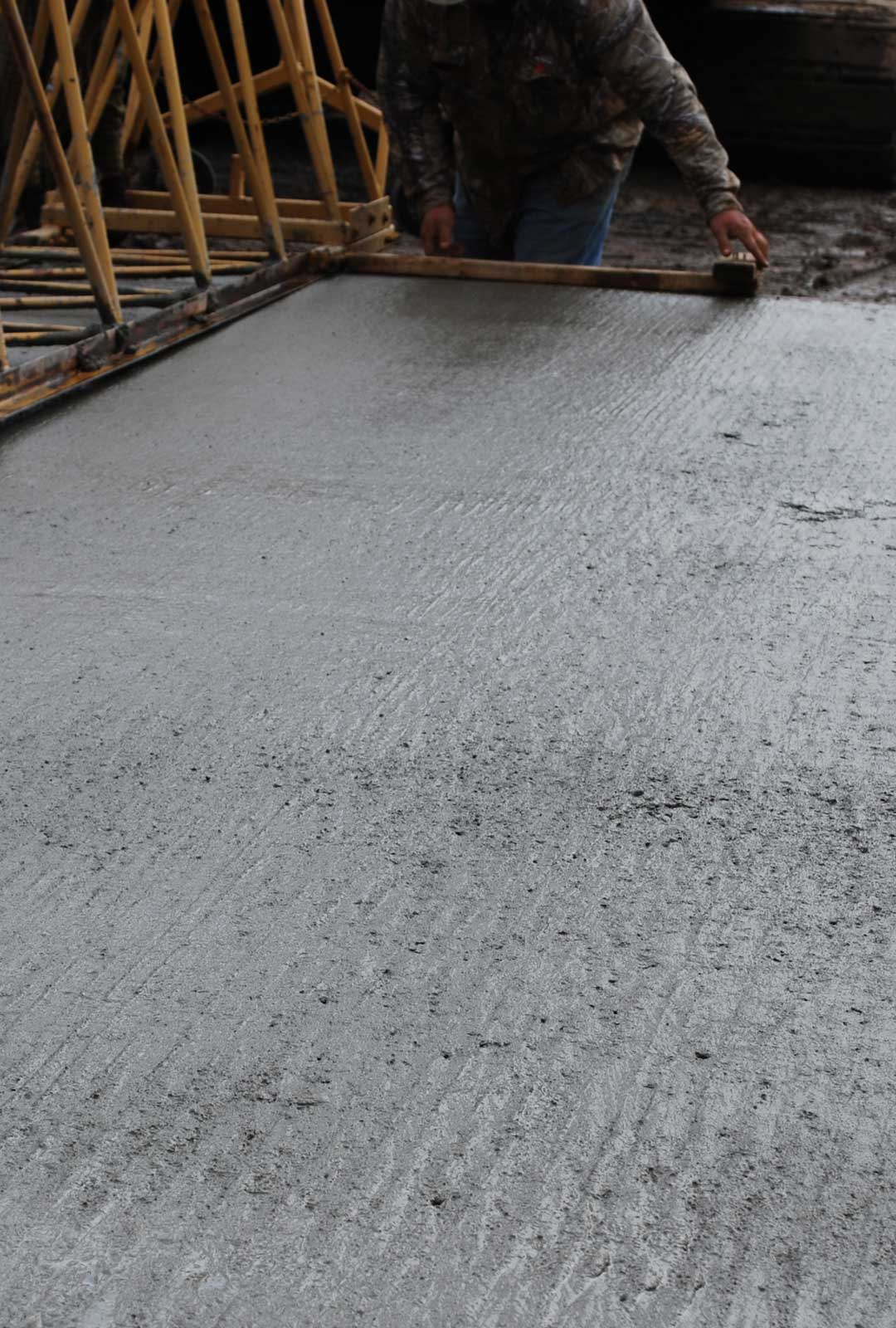
Results from the West Congress test project, released in 2016, indicate “The West Congress project showed reduced cracking at one year over the control sections. The reduced cracking will lead to longer service life and a more durable structure,” said Rupnow. The contractor noted easier finishability characteristics and that, “ICC is just like normal concrete.” Based on the laboratory and field results, a standard lightweight fine aggregate replacement rate between 225 and 275 pcy is suggested for implementation.
LTRC also issued an implementation statement: “The results show that lightweight aggregate fines, when used for internal curing purposes, do not adversely affect the fresh or hardened concrete properties. Hardened properties of strength and surface resistivity are generally improved. The cracking potential has been shown to be reduced through the two documented field applications, even where curing compound was inadvertently not applied. A standard replacement rate between 225 and 275 pcy of lightweight fines is suggested. Combining internal curing with a 7-day wet burlap cure is recommended. Implementation of internal curing technology will provide a benefit to the Department in terms of longer service-life structures with a lower life-cycle cost.”
The Lafayette Consolidated Government Engineering Group, including Mitch Wyble, was commended for their collaboration on this ICC project by LTRC, noting the importance of such partnerships for advancing infrastructure durability.
“They liked what they saw,” says Rupnow. “In the words of the contractor, producer, and engineers, ‘it looks just like regular concrete.’”
Wyble says he knew early on that ICC would be a winning option for the LADOTD – even though the material had yet to be tested by the department. In fact, Wyble’s not surprised at all that the end result was extremely positive. “The job came out beautifully,” says Wyble. “To date, we haven’t seen a single crack in that bridge.”
- The Issue: LADOTD sought to reduce cracking and improve the durability of bridge decks using an innovative internally cured concrete (ICC) solution.
- What Arcosa Did: Arcosa Lightweight provided lightweight aggregate to replace a portion of fine aggregate in the concrete mix, enabling internal curing.
- Why Lightweight Works: Lightweight aggregate improves grading, reduces cracking, and enhances finishability. ICC extended the service life of bridge structures by minimizing cracking.
- Result: Reduced cracking at one year, extended service life, and improved durability in the West Congress project. Based on the results, a lightweight aggregate replacement rate of 225-275 pcy is recommended.
- Key Quote: “The West Congress project showed reduced cracking at one year over the control sections. The reduced cracking will lead to longer service life and a more durable structure.” – Tyson Rupnow, Ph.D., P.E., Associate Director of Research, LTRC
- Industry Context: ICC implementation should include a 7-day wet burlap cure for optimal results.
- Lessons Learned: Internal curing technology provides significant benefits, including a longer structure life with lower life-cycle costs.
- Call to Action: Learn more about Arcosa’s lightweight aggregate solutions for infrastructure projects.
- Project: West Congress Street Bridge ICC Project
- Location: Lafayette Parish, Louisiana
- Customer: Builders Supply
- Client: Lafayette Consolidated Government
- Project Size: Two bridge deck spans, one guardrail wall, and one approach slab
- Related Link 1: Visit Website
Key Insights:
Quick Facts:
•
•
•
How Arcosa Helped:
•
•
Final Results
Key Quote
Context:
•
•
Additional Case Studies
Kansas Department of Transportation (KDOT) Bridge Deck Study: Advancing the Use of Internal Curing
- Teaser:
Since 2016, the Kansas Department of Transportation (KDOT), along with the University of Kansas (KU) and the State of Minnesota, has been studying the use of internal curing to improve bridge deck service life. Traditional concrete bridge decks, with their high cementitious materials content and low water-to-cement ratio, are prone to early age cracking and self-desiccation. - Article Body Text:
Phase one of the study evaluated internal curing (IC) with 100% portland cement concrete mixtures. In this phase, IC was combined with supplementary cementitious materials (SCMs).
The bridge, located near Olathe, Kansas, uses a concrete mix that includes pre-wetted fine lightweight aggregate from Arcosa, along with slag and silica fume. The goal is to reduce early age cracking and improve resistance to chloride penetration, which leads to deterioration. Dan Wadley, Chief of the Bureau of Research for the Kansas Department of Transportation, is overseeing the study, along with Dr. David Darwin, chairman of KU’s Department of Civil, Environmental & Architectural Engineering.
Careful Monitoring
Six months after completion, Wadley spot-checked the decking of the 450-foot structure, looking for signs of premature cracking and gathering data using embedded sensors. These sensors, installed during the September 2021 placement of the internally cured concrete, transmit data on variables such as temperature, helping researchers track strength gain through a maturity curve.
“As part of the research into internal curing that KDOT is doing, they installed sensors in the concrete that record different variables such as temperature, which they can use to calculate strength gain with a maturity curve,” explains Daron Brown, Midwest Regional Sales Manager at Arcosa Lightweight.
“That way, they can continue to monitor that bridge.”
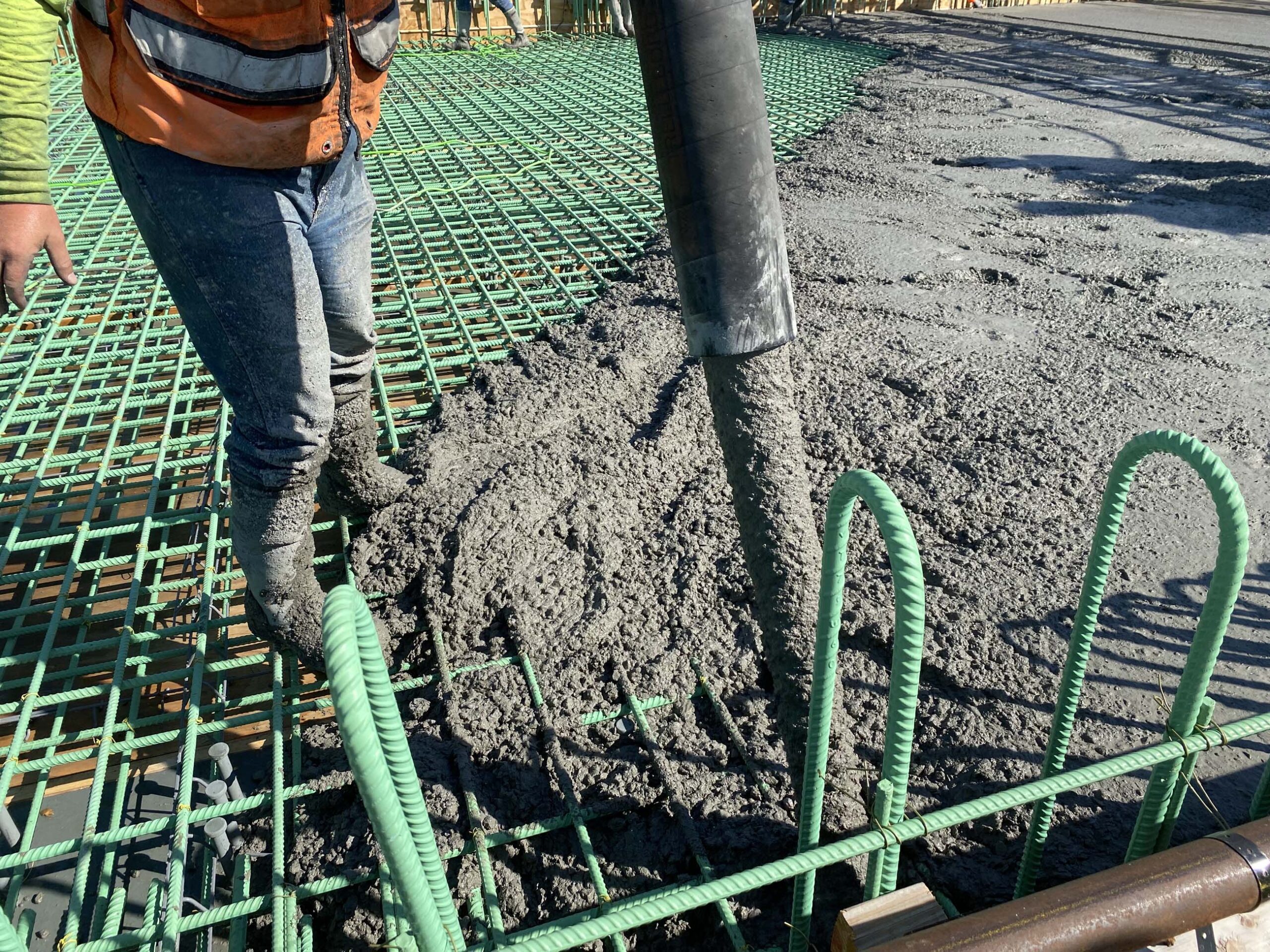
Pyramid Constructors placed approximately 800 cubic yards of concrete in one continuous pour that started at 3:30 AM and concluded 14 hours later at 5:15 PM. The concrete supplier, carefully controlled the concrete mix by adding ice to maintain the desired temperature range of the concrete, even as ambient temperatures fluctuated.
Wadley notes in this placement, crews were careful to ensure the fresh concrete was covered with burlap within 15 minutes of placement. He also noted that finishing aids, which are typically 90% water, were not used in the concrete.
“The sensors helped us monitor the temperature of the deck as it cured,” says Wadley. “The ready mix producer did a great job keeping the mix consistent and adding the right amount of ice to keep the concrete temperatures in the 80s like we wanted.”
The success of this project highlights the importance of best construction practices to prevent cracking in bridge decks, particularly in the areas of consolidation, finishing, and curing.
Next Steps
As the study progresses, additional maturity tests and crack surveys will be conducted. The data collected will help refine specifications for Internally-Cured Low-Cracking High-Performance Concrete (IC-LC-HPC), with the ultimate goal of using internal curing more widely in various infrastructure projects.
“My hope is that we can use internal curing more frequently and on a wider range of applications simply because it works so well. On the paving side, it helps reduce curling and warping. On the bridge side, it reduces cracking quite a bit,” says Wadley.
Widespread Benefits
According to Daron Brown, many Departments of Transportation have seen similar results, with internal curing reducing premature cracking and extending the service life of concrete structures.
“They like the benefits it provides as far as producing a better concrete mixture. With less cracking, they’re going to get a longer service life out of their pavements or their bridge decks, wherever they decide to use it,” says Brown.
- The Issue: KDOT sought to reduce early age cracking and improve the durability of concrete bridge decks using internal curing. Traditional concrete bridge decks, with high cementitious content and low water-to-cement ratios, are prone to cracking and self-desiccation, leading to long-term maintenance issues.
- What Arcosa Did: Arcosa supplied pre-wetted fine lightweight aggregate for the concrete mix. The aggregate retains moisture, enabling internal curing, which helps maintain optimal hydration and reduces shrinkage in the concrete.
- Why Lightweight Works: The lightweight aggregate ensures that the concrete maintains internal moisture, preventing early-age desiccation and reducing the likelihood of cracking. This helps the bridge deck resist chloride penetration and extends its lifespan.
- Result: KDOT placed 800 cubic yards of internally cured concrete in a continuous pour. Sensors embedded in the deck monitor temperature and strength development, providing real-time data to evaluate the concrete’s performance and the benefits of internal curing.
- Key Quote: “The ready mix producer did a great job keeping the mix consistent and adding the right amount of ice to keep the concrete temperatures in the 80s like we wanted.” — Dan Wadley, Chief of the Bureau of Research, KDOT
- Industry Context: The KDOT study is closely monitoring the bridge deck through embedded sensors to assess the performance of internally cured concrete. This approach, using lightweight aggregate, aims to reduce cracking and increase the long-term durability of the bridge.
- Lessons Learned: Internally cured concrete, facilitated by lightweight aggregate, helps prevent early-age shrinkage and cracking, improving the durability and service life of bridge decks.
- Call to Action: Arcosa Lightweight’s pre-wetted fine aggregate provides a proven solution for infrastructure projects that require enhanced durability and resistance to cracking, making it a valuable choice for bridge decks and other applications.
- Project: KDOT Bridge Deck Study
- Location: Olathe, Kansas
- Client: Kansas Department of Transportation (KDOT)
- Project Size: 450-foot bridge deck
Key Insights:
Quick Facts:
•
•
•
How Arcosa Helped:
•
•
Final Results
Key Quote
Context:
•
•
Additional Case Studies
State DOTs See Benefits in Internally Cured Bridge Decks
- Teaser: Faced with the challenge of maintaining aging infrastructure while optimizing taxpayer dollars, state Departments of Transportation are turning to innovations like internally cured concrete to improve bridge deck durability. Worn surfaces not only inconvenience drivers but also lead to frequent, costly repairs. By integrating advanced materials and data-driven decision-making, DOTs are extending the lifespan of critical infrastructure, reducing environmental impact, and improving safety for the public.
- Article Body Text:
Because bridge decks are exposed to weathering from both above and below, they are particularly susceptible to deterioration. Unsafe bridges, or those under repair, disrupt traffic flow and cause delays. Several state DOTs, including New Jersey, Indiana, Illinois, and Louisiana, have turned to internally cured concrete (ICC) for bridge decks, reaping significant benefits from this innovation.
Internally cured concrete incorporates pre-wetted lightweight aggregates (LWA) into the concrete mix. These aggregates provide internal moisture during curing, ensuring complete cement hydration. This process not only strengthens the concrete but also reduces stresses and strains that typically lead to cracking.
By balancing moisture levels throughout the slab, ICC reduces shrinkage cracks at the surface and minimizes curling and warping. This improvement in performance helps to prevent water and deicing salts from penetrating the concrete, significantly reducing steel reinforcement corrosion and extending the lifespan of bridge decks to over 75 years. Additionally, for jointed concrete slabs, reduced warping leads to smoother pavements and a more comfortable ride for drivers.
A Continued Mandate for Internal Curing
Since 2015, research into internally cured concrete (ICC) has consistently demonstrated its benefits in enhancing bridge deck durability. Early projects by the Louisiana Transportation Research Center (LTRC), such as those on US Route 80 and West Congress Street, showed a significant reduction in cracking compared to conventional concrete.
Tyson Rupnow, Ph.D., P.E., Associate Director of LTRC, commented:
“The reduction in cracking, even in sections without external curing, was striking. The bridges have now been in place for several years with excellent results.”
As a result of these early successes, the Lafayette Consolidated Government (LCG) now mandates ICC for bridge deck construction. This positive outcome has inspired broader adoption of ICC in other states, such as Indiana, Illinois, and New Jersey, which have integrated ICC under the Every Day Counts (EDC-7) initiative. Ongoing research continues to confirm ICC’s potential to extend the lifespan of bridge decks beyond 75 years, significantly reducing the need for maintenance and repairs.
Incremental Steps in the Midwest
Both Indiana and Illinois DOTs have continued their incremental approach to adopting internally cured concrete (ICC) for bridge decks. Though ICC is not yet mandated, both states have developed special provisions to guide mix design and placement, based on trial projects initiated in partnership with Purdue University.
Tony Zander, Area Engineer in INDOT’s Pavement Division, described their efforts:
“We launched pilot projects using lightweight fine aggregates for internal curing as part of high-performance concrete tests. These projects, such as the twin bridge structure on Interstate 69, have provided valuable data, and we continue to monitor crack reduction and chloride penetration.”
As of 2024, both states have gathered substantial data, but additional research is still necessary to determine the most effective structure types for ICC. These trials are part of broader efforts under FHWA’s Every Day Counts (EDC-7) program, which encourages the adoption of innovative materials and methods to improve infrastructure resilience.
Expanding ICC Adoption in Illinois
The Illinois Department of Transportation (IDOT) began exploring ICC as a way to mitigate shrinkage-related cracking in bridge decks as early as 2010. James Krstulovich, Project Support Engineer, Illinois Department of Transportation, District 6, emphasized that ICC has proven to be an effective solution for reducing cracking.
“Based on extensive research, we developed special provisions for ICC, which have already been implemented in four districts across Illinois,” said Krstulovich.
As of 2024, four out of nine districts in Illinois have adopted these provisions, and two bridge projects using ICC have been completed successfully. Contractors and producers have reported no significant difficulties when using ICC, and feedback has been overwhelmingly positive.
“There’s virtually no difference between working with ICC and regular concrete for our teams,” Krstulovich said. “The benefits happen in the background, and our finishers don’t notice any major changes in their workflow.”
With results looking promising, Krstulovich anticipates that more districts will adopt ICC in the coming years, thanks to its proven benefits in reducing maintenance costs and extending bridge deck service life. Illinois is also participating in the FHWA’s Every Day Counts (EDC-7) program to further expand ICC usage.
- The Issue:State Departments of Transportation (DOTs) need to reduce early-age cracking and extend the lifespan of bridge decks, while optimizing taxpayer funds and reducing long-term maintenance costs.
- Why Lightweight Works: ICC minimizes shrinkage cracks and enhances concrete strength by providing internal moisture during curing.
- Result: States like New Jersey, Indiana, and Illinois have successfully adopted ICC, showing reduced cracking and longer-lasting infrastructure.
- Key Quote: “The benefits of internally cured concrete happen in the background, with contractors noticing minimal differences in the workflow.” – James Krstulovich, Project Support Engineer, Illinois DOT, District 6
- Industry Context: Adoption of ICC is part of a nationwide effort under EDC-7 to encourage states to use innovative methods that extend infrastructure service life.
- Lessons Learned: ICC, supported by EDC-7, provides a cost-effective, sustainable solution for extending the lifespan of bridge decks across the U.S.
- Call to Action: Learn more about EDC-7 and its nationwide impact on ICC adoption at FHWA’s Every Day Counts website.
- Related Link 1: Visit Website
Key Insights:
Quick Facts:
•
•
•
How Arcosa Helped:
•
•
Final Results
Key Quote
Context:
•
•
Explore Further
Fact Sheet: Enhancing Performance with Internally Cured Concrete
Additional Case Studies
U.S. 80 Bridge: A Successful Early Test for ICC Bridge Decks
- Teaser: When the Louisiana Department of Transportation & Development (LADOTD) planned to build a bridge on U.S. 80 over the Kansas City Southern railroad, they chose to incorporate internally cured concrete (ICC) to improve durability and performance. As an early successful test project, this effort demonstrated ICC’s potential to significantly enhance the lifespan of bridge decks.
- Article Body Text:
ICC is a concrete mixture in which some fine aggregate is replaced with pre-wetted lightweight aggregate (LWA), providing adequate moisture from within the mixture to replace water lost due to chemical shrinkage. Known for its strength and reduced shrinkage, ICC has been used successfully on bridge decks.
Wanting to leverage these advantages, LADOTD implemented a demonstration project to test ICC’s value. In this case, the U.S. 80 bridge over the KCS railroad was constructed with portions of the structure incorporating ICC.
According to Bill Wolfe, Director of Technical Sales at Arcosa Lightweight, the company provided lightweight aggregate for the ICC process across two of the five bridge spans, each approximately 270 feet in length. The first span used 300 pounds of pre-soaked lightweight fine aggregate per cubic yard of concrete, while the second used 150 pounds.
“Even with less internal curing moisture, the process still offers high value,” says Wolfe.
Two Decks in Place
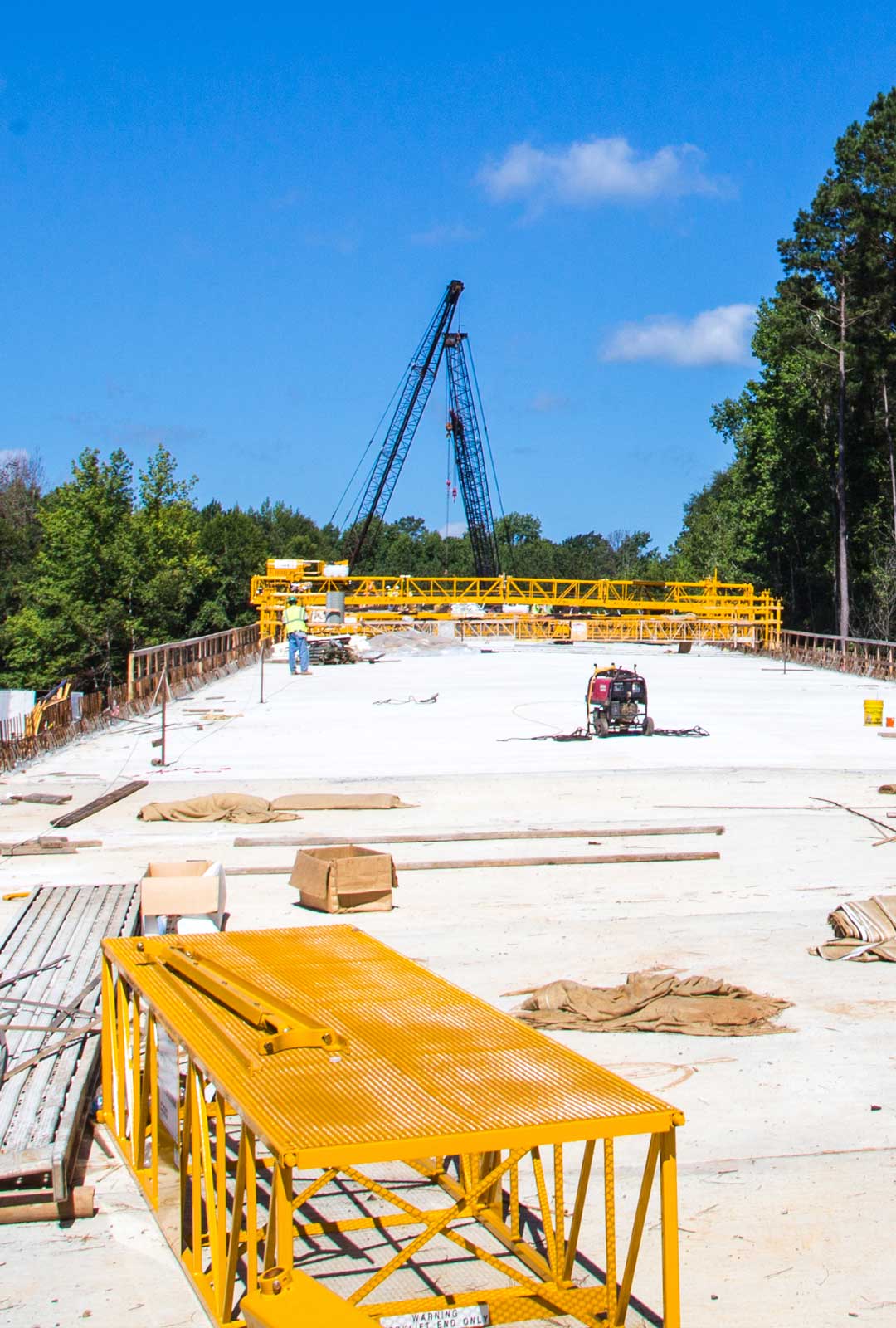
With the two ICC decks in place, LADOTD then monitored their performance compared to the three spans without ICC. That work was part of a research project conducted by the Louisiana Transportation Research Center (LTRC).
In LTRC’s final report, the authors noted: “This project showed significantly less cracking over the control about nine months after placement of the ICC sections.”
“The reduced cracking will lead to longer service life and a more durable structure.”
“The contractor noted easier finishability characteristics and that, “ICC is just like normal concrete.”
Arcosa’s customer, Builders Supply Company, Inc., was ready mix supplier for the project and serves all of Northwest and Central Louisiana.
Ken Viers, formerly of Builders Supply, today serves as a QC Representative at Ready Mix USA’s Opelika, Alabama operation. Looking back at the Louisiana Bridge project he says:
“Compared to our usual materials, ICC substantially increased concrete compressive strength. It was a real eye-opener.”
Builders Supply adapted its delivery processes to incorporate the ICC mix, with smooth execution and positive results.
Following the successful test, LTRC now suggests a standard lightweight fine aggregate replacement rate between 225 and 275 pcy for implementation.
- The Issue: LADOTD needed a durable solution for constructing the U.S. 80 bridge over the Kansas City Southern railroad tracks, aiming to reduce cracking and increase strength
- What Arcosa Did: Arcosa supplied lightweight aggregate (LWA) for the internally cured concrete (ICC) process.
- Why Lightweight Works: ICC provides internal moisture, reducing shrinkage and improving compressive strength.
- Result: Internal curing increases concrete’s resistance to early cracking, allowing the production of higher-performance concretes that may last more than 75 years.
- Key Quote: “Compared to our usual materials, ICC substantially increased concrete compressive strength. It was a real eye-opener.” – Ken Viers
- Industry Context: Successful early test projects such are why the Federal Highway Administration (FHWA) says these “higher-durability concrete mixtures can last several times longer than traditional concretes”.
- Lessons Learned: ICC provides durable, long-lasting results with minimal adjustments to traditional processes.
- Project: U.S. 80 Bridge
- Location: U.S. 80, Louisiana
- Customer: Builders Supply Company
- Client: Louisiana Department of Transportation & Development (LADOTD)
- Project Size: Five bridge spans, two incorporating ICC
Key Insights:
Quick Facts:
•
•
•
How Arcosa Helped:
•
•
Final Results
Key Quote
Context:
•
•