TVA Utilizes Internal Curing for Historic Hydroelectric Dam’s Bridge Deck
TVA Utilizes Internal Curing for Historic Hydroelectric Dam’s Bridge Deck
The Wilson Dam bridge deck, part of the iconic 100-year-old hydroelectric dam on the Tennessee River in Muscle Shoals, Alabama, is ready handle another century of traffic. Arcosa Lightweight’s material played a pivotal role in these extensive repairs, ensuring the bridge’s longevity by supporting the Tennessee Valley Authority’s (TVA) first-ever use of internally cured concrete.
This innovative solution will help the historic structure stand the test of time, offering enhanced durability and resilience.
“Our goal was to provide a 100-year bridge deck, and internal curing is a great way to achieve that,” explains Benjamin Byard, Bridge Program Manager at TVA. “Because you keep the internal relative humidity high much longer, you get increased strength before the concrete starts to desiccate. The combination of better strength and delayed drying shrinkage gives you a denser, better concrete. The decrease in cracking and increase in mechanical performance are the values of internal curing.”
Byard also highlighted the new surface, saying,
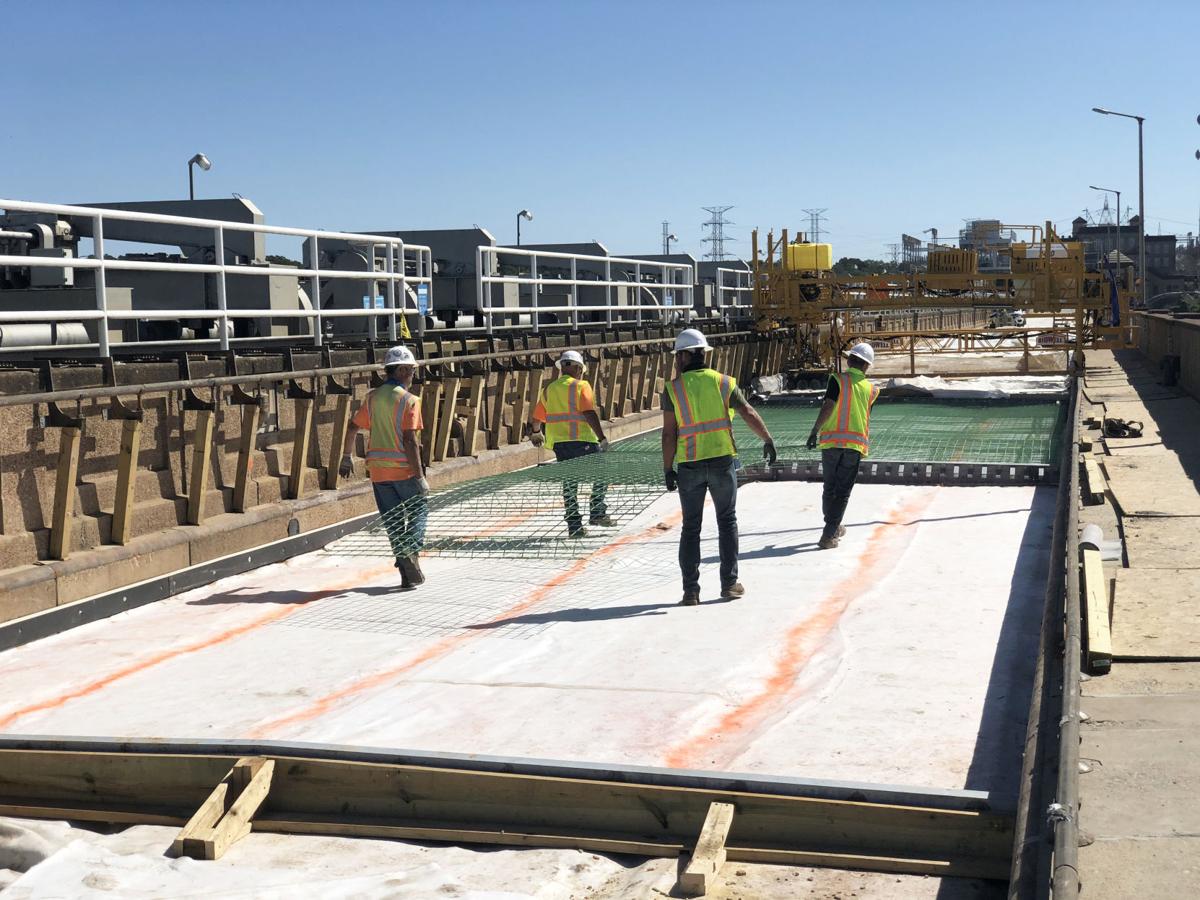
Renovation Overview
The Wilson Dam project included renovations to the dam structure, power-generating equipment, and significant bridge deck repairs. The bridge atop the dam connects Colbert and Lauderdale Counties and was originally constructed between 1918 and 1924. Though traffic slowed after the opening of the nearby Patton Island Bridge in 2008, TVA officials were eager to replace the 1950s-era concrete pavement.
“When the driving surface was removed in 2019, extensive damage was found. Cracks formed in the unreinforced concrete, allowing water to infiltrate and cause deterioration,” explains Byard. This led to the decision to resurface the bridge with internally cured concrete to extend its lifespan and reduce future maintenance needs.
Local Supplier
Matthew Moore, Quality Control Lead at CEMEX for the North Alabama region, says Ready Mix USA has extensive experience batching concrete with lightweight aggregate, most recently on a major new hospital which opened very near the Wilson Dam. But this project was somewhat unique. “We’ve used a lot of lightweight aggregate through the years and this project was a little different,” says Moore. “Basically, the internally cured concrete is designed to a weight and to an air spec and like I said, we have to take a little more care with the lightweight and make sure it’s kept wet at the plant.”
The concrete used in the renovation was batched from Ready Mix USA’s Florence Industrial Park plant. “For this job, we used the Florence plant on the north side of the river as our main facility, with Tuscumbia on the south side as backup,” says Moore.
Specifying Internal Curing
“It’s lightweight fine aggregate, similar to sand, that’s pre-soaked before batching the concrete,” explains Bill Wolfe, Marketing & Technical Manager at Arcosa Lightweight. “By replacing a portion of the concrete sand with pre-wet lightweight aggregate, internal moisture is provided to keep the hydration process going longer as the concrete cures.”
A Special Landmark
The Wilson Dam region is significant for the TVA, as it was the agency’s original headquarters when founded in 1933. “Helping restore Wilson Dam, the only neoclassical-style dam built by the U.S. Army Corps of Engineers in the TVA system, has been the highlight of my career,” says Byard.
The bridge reopened to traffic in December 2020, following completion of the renovations. Byard is confident in the project’s success: “If I’m doing a bridge deck, by golly, it’s going to be internally cured. For a relatively minor increase in cost, you get a lot more bang for your buck in performance.”
Additional Case Studies
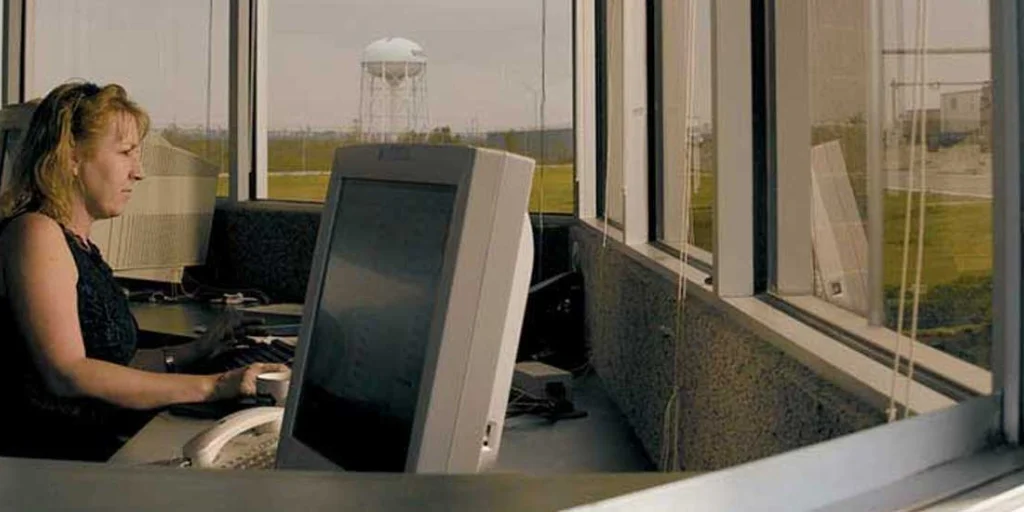
A Look Back at the Union Pacific Dallas Intermodal Terminal (DIT)
The Union Pacific Dallas Intermodal Terminal (DIT) project stands as a testament to the transformative benefits of lightweight aggregate in improving the durability, strength, and overall performance of concrete paving. Notably, it remains one of th…
Read More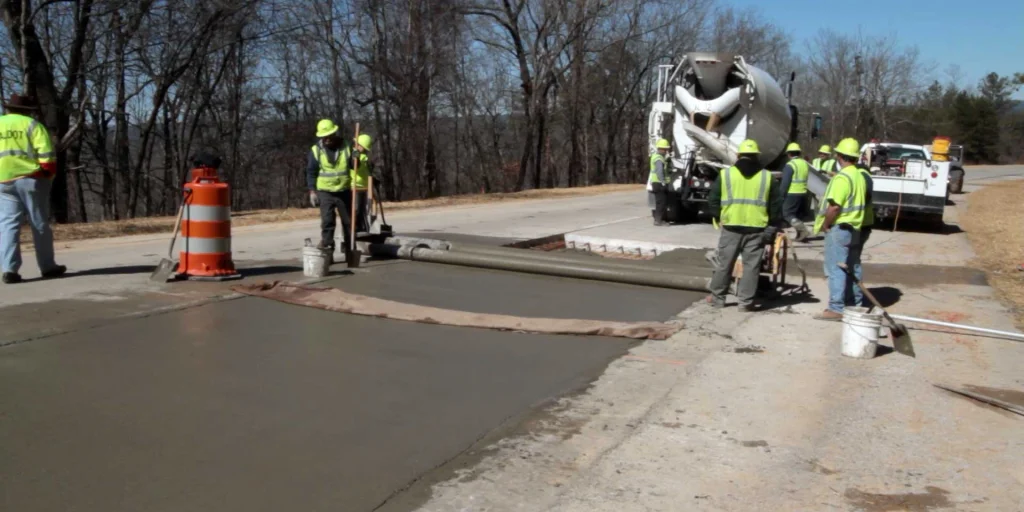
Internal Curing Gains Ground in Highway Construction: A Durable Solution
Internal curing is being recognized as a significant advancement in concrete technology. Today, the integration of lightweight aggregate (LWA) into concrete offers enhanced performance by reducing cracking, improving durability, and extending the se…
Read More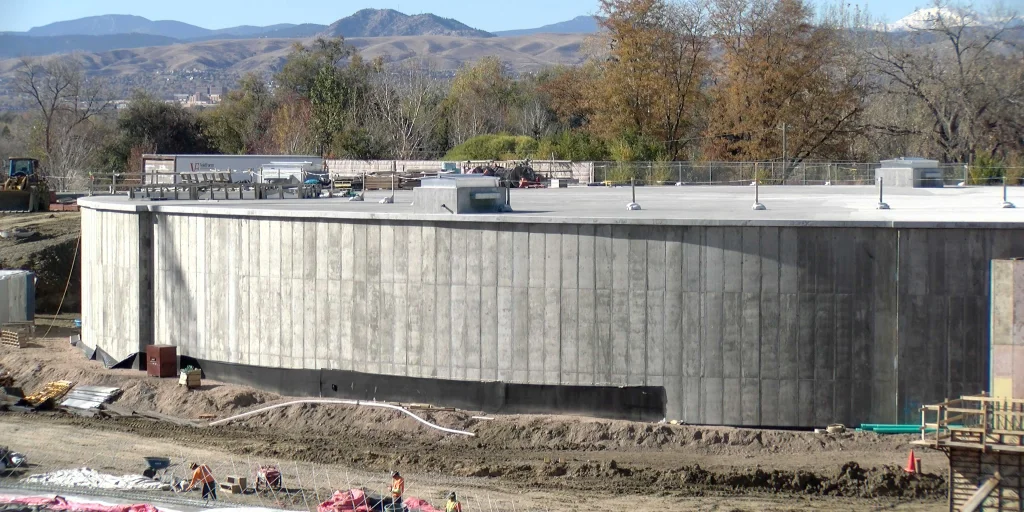
Internally Cured Concrete Enhances Water Tank Durability in Denver Water Projects
Denver Water is committed to ensuring safe and reliable water for its customers. To achieve this, the utility continually upgrades its system by replacing aging, large-capacity water storage tanks with more durable designs that are less susceptible…
Read More