Shasta Arch Bridge Project: Using Arcosa Lightweight Aggregate for High-Performance Concrete Solutions
- Home
- Case Studies
- Structural Lightweight Concrete
- Lightweight Concrete for California Department of Transportation’s Shasta Arch Bridge
Key Insights:
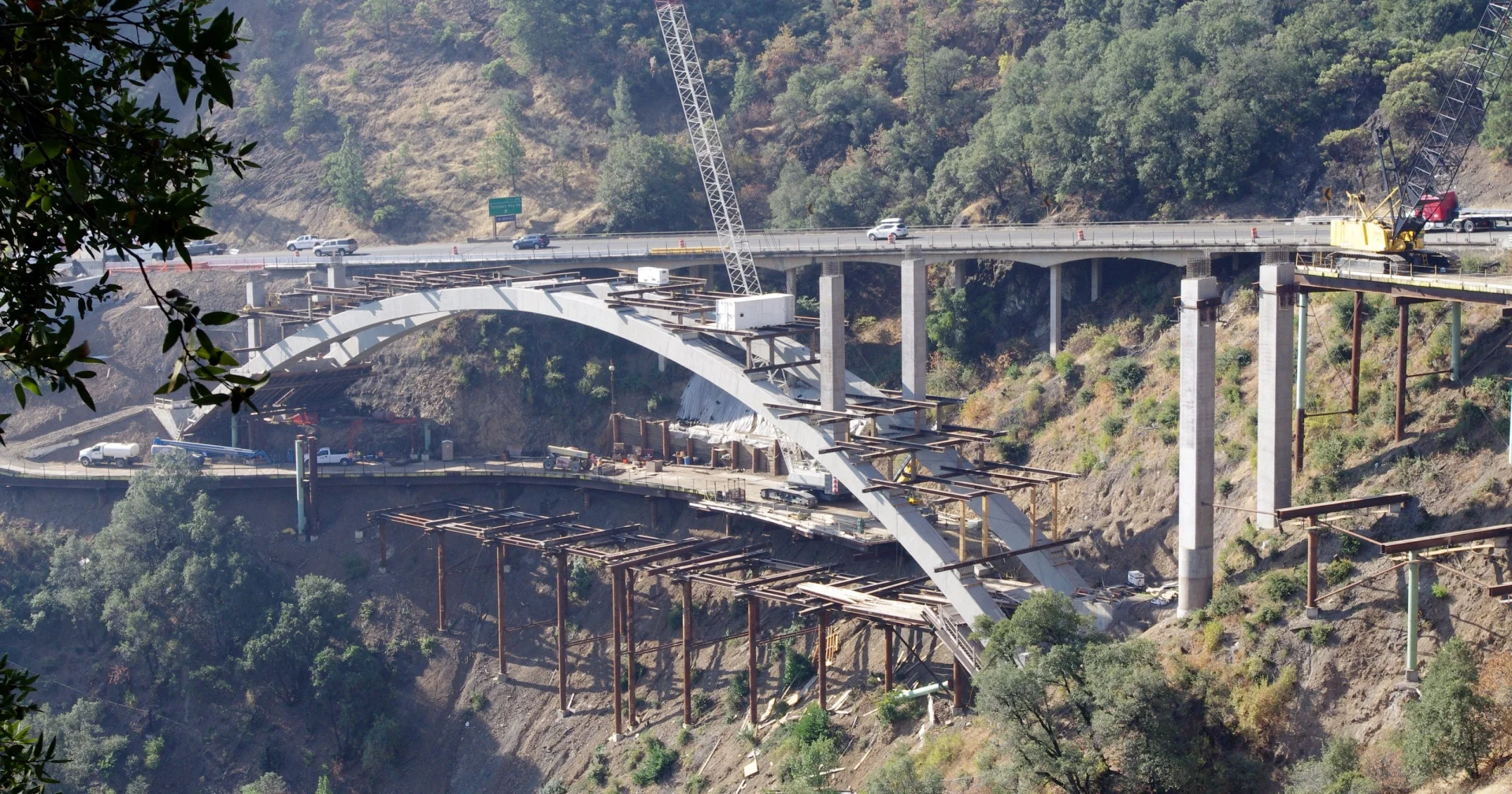
Quick Facts
-
Name: Shasta Arch Bridge Project
-
Location: Northern California
-
Client: California Department of Transportation (Caltrans)
-
Size: 366 ft and 400 ft arch ribs, spanning a steep hillside
How Arcosa Helped
-
Our Solution: Arcosa provided Hydrolite® expanded clay lightweight aggregate, pre-conditioned for consistent moisture content and optimal pumpability, which enabled Caltrans to achieve the necessary strength and reduced load requirements for the bridge.
-
Why Lightweight Works: The use of lightweight concrete decreased the overall structural load, allowing the bridge to perform better under the stress of daily use while maintaining the aesthetic and structural integrity. The lightweight aggregate also helped manage pumpability and temperature in mass concrete sections.
Final Results
-
The lightweight concrete met all project specifications, including compressive strength of 6,000 psi and equilibrium density of 120 pcf. Pumping rates exceeded expectations, and Arcosa’s aggregate contributed to the long-term reliability of the bridge.
Key Quote
Context:
-
Considerations: Pre-saturation of the lightweight aggregate was critical for maintaining pumpability and reducing thermal issues in the mass concrete.
-
Lesson to Learn: Collaborative adjustments in material proportions and pre-conditioning can resolve common challenges in lightweight concrete projects, such as pumpability and temperature control.
Explore Further
Shasta Arch Bridge Project: Using Arcosa Lightweight Aggregate for High-Performance Concrete Solutions
Ric Maggenti, who was a Senior Materials & Research Engineer for the California Department of Transportation (Caltrans) before his retirement, explained, “Lowering demand consisted of changing the structure concrete (stem, bent caps, and deck) from a normal weight, normal strength concrete to a high strength, lightweight concrete.” Maggenti emphasized that lightweight concrete has been successfully used in numerous bridges worldwide, citing the Bay Bridge, which has shown no observable deck distress after more than 80 years of service, and the Napa River Bridge, which continues to perform well even after the 2014 Napa earthquake.
Why High-Performance, High-Strength Lightweight Concrete?
Originally, the bridge was designed using normal weight concrete with a specified compressive strength of 4,000 psi. Maggenti explained, “The increased design strength [for the lightweight concrete] eliminated any need to significantly adjust for rebar developmental lengths, or accounting for lower shear, creep, modulus of elasticity, and modulus of rupture values used in the original design.” By increasing the compressive strength to 6,000 psi, Maggenti noted, “these other property values converge to those of a lower strength normal weight concrete,” addressing concerns such as Alkali Silica Reaction (ASR), Delayed Ettringite Formation (DEF), deck permeability, and cracking.
“The increased design strength eliminated any need to significantly adjust for rebar developmental lengths, or accounting for lower shear, creep, modulus of elasticity, and modulus of rupture values used in the original design.”
Arcosa Lightweight Aggregate for the Shasta Arch Bridge Project
Arcosa’s Hydrolite® expanded clay aggregate, produced in Frazier Park, California, was selected for the project due to its ability to meet the strict performance requirements. Pre-conditioned at the Frazier Park plant, the aggregate arrived at the ready-mix concrete plant in a near-saturated condition, simplifying the production of pumpable lightweight concrete.
Pumping Lightweight Concrete
Maggenti directly addressed concerns about the pumpability of lightweight concrete, stating, “[Caltrans] was not at all subjectively distracted by a belief that lightweight concrete is inherently difficult to pump.” He explained that the difficulty in pumping lightweight concrete arises when the aggregate is not saturated, but that Arcosa’s pre-saturated aggregate eliminated this issue. Maggenti continued, “A 125 pcf concrete imparts by its mass a pressure of 0.87 psi resisting its vertical motion inside the pipe while a 150 pcf concrete imparts by its mass a pressure of 1.04 psi per cubic foot of concrete. That is a 20% increase in force to move normal weight concrete. So why would a lightweight concrete be more difficult to pump than a normal weight concrete?”
Ultimately, the lightweight concrete mix exceeded expectations, with pumping rates occasionally reaching over 100 cubic yards per hour (cy/hr), far surpassing the original target of 60 cy/hr. “The mix pumped better than anybody expected, and no additional pumping agent chemical admixture was used,” Maggenti added.
Mass Concrete Issues
There were concerns about exceeding the maximum allowable temperature in the mass concrete within the diaphragms and bent caps due to the high cementitious content of 900 pounds per cubic yard. Two cooling pipes were installed longitudinally through the bent caps to control the concrete temperature, which had a target of 160°F. While temperatures exceeded this at times due to extreme ambient air temperatures and the difficulty of controlling water temperature in the cooling pipes, the concrete did not overheat.
“Initially it was believed the lightweight aggregate would exacerbate mass concrete issues. However, this was not the case for the Arcosa aggregate. The difference was the amount of water in the lightweight aggregate.” — Ric Maggenti
Maggenti explained that Arcosa’s aggregate, with an absorption rate of over 24%, requires more energy to increase its temperature than traditional mineral aggregates, which helped prevent thermal issues caused by the high cementitious content.
Conclusion
For this project, all of the requirements for a lightweight, air-entrained concrete mix that was pumpable, durable, and high-performing were met. All concrete strengths exceeded the specified requirements for high-strength concrete, and the 120 pcf equilibrium density target was achieved. The results of air content field tests on the plastic concrete were confirmed by petrographic examination of the hardened concrete.
“The requirement for a lighter structure was met by using Arcosa Lightweight Aggregate, producing concrete with a maximum equilibrium density of 120 pcf,” Maggenti stated. The pre-conditioned lightweight aggregate helped lower pump line pressures, allowing the concrete to be pumped efficiently, sometimes at rates exceeding 100 cy/hr. The consistency of the concrete remained stable throughout transport, even with extended durations of up to 1½ hours.
With these unique attributes, it’s no surprise Caltrans labeled the resulting material “Super High Performance Concrete” and anticipates it to be a model for future challenging situations.